Tech Tip: Recycling Wash Water
Water-Saving Basics & Best Practices
Maintaining clean wash water is essential – and whether you’re adding a first wash plant or tweaking an existing one – certain basics and best practices may help you avoid the common pitfalls in wet processing.
“It’s a whole new world out there in wet processing. Most ‘easily mined’ reserves are long gone – and we’re short on aggregate folks who’ve washed rocks all their lives,” says Lauren DeBow, washing applications engineer for Superior Industries. DeBow and her team assist producers with thorough applications analysis and customized wash plant solutions. “Washing is a unique process for each and every operation,” she stresses.
“If you’re reusing dirty water in your wash system, you’re putting all the dirt, debris, clay, and fines right back on the product you’re trying to clean – while at the same time causing wear, tear, clogging, and buildup on the equipment, water pipes and spray bars,” stresses DeBow.
She points out the basics about three common methods of recycling and reusing wash water – while sharing several “best practices” in wet processing.
Traditional Settling Ponds
A simple concept – dirty water is pumped to a settling pond – and over time and with gravity, the particles settle out naturally, and the fresh water floats off naturally to the next level of the pond and is reused. The disadvantages are space requirements, and permitting restrictions that make it harder to establish settling ponds.
There are also evaporation issues and maintenance costs – which can be hefty when having to dig out sediments to ensure the depth needed for required settling.
On the plus side, settling ponds may work well for operations whose pond management may include a larger footprint and the successful use of flocculants for greater settling efficiencies.
Ultra-Fines Recovery Systems
An ultra-fines recovery system offers the advantage of removing a good portion of material down to a #400-mesh, keeping more fines out of the pond, and resulting in less digging during pond maintenance.
A UFR also provides a stackable material that can become a saleable product, resulting in minimized waste. Also, the water remains much cleaner and requires less processing before reusing it.
One of the downfalls of UFRs is an occasional situation where the wastewater travels too far downstream in the pond – requiring the need for additional flocculants to separate out particles – as there are not enough larger particles present to stimulate the settling process. The latter results in a “double dipping” during the process. However, as long as a UFR can minimize the need to dig out the pond, there is a savings in operating costs.
Clarification Systems
Growing in usage, clarification systems start with something as simple as a thickener, or the use of a clarification tank. No matter the option, there are space requirements and flocculant requirements. Yet clarification systems are becoming more popular as they’re less likely to incur permitting issues, and they allow operations to eliminate the use of a settling pond.
Clarification systems discharge a sludge waste product that’s typically pumped off to a designated area where it must sit and dry. Sometimes, this waste product requires the use of filter or belt presses that pull out extra moisture, creating a solid, stackable cake that’s potentially used as a fill product.
Certainly, the biggest drawback is the large capital investment required – often over $1 million for a simple setup. But depending upon the cycle time of the complete clarification system (which can create a bottleneck), it delivers extremely clean water back into the wash circuit.
"Washing is a unique process for each and every operation."
- Lauren DeBow: Washing Equipment Specialist
Finding The Right Solution
Efficiency improves when optimizing all the equipment in the wash plant. For example, if sand screws are not running properly, an operation may be washing out valuable product and sending it to the pond. Conduct a thorough plant audit to evaluate the performance of each piece of equipment in the plant.
Again, each wet processing operation is different, and the right solutions depend upon specific parameters such as material type, moisture content, specification requirements, size of footprint, permitting restrictions, financial limitations, water rates, water availability, and more. Proper analysis by an experienced applications engineer is advised. Avoid “cookie-cutter” or “one-size-fits-all” equipment approaches.
The best practice is relying upon highly targeted, customized solutions.
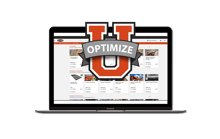
OptimizeU - Strategic Learning
Pursue greater production with comprehensive online courses in crushing, screening, conveying, and washing. Check out the premiere training resource in the construction aggregates industry.
Related Content
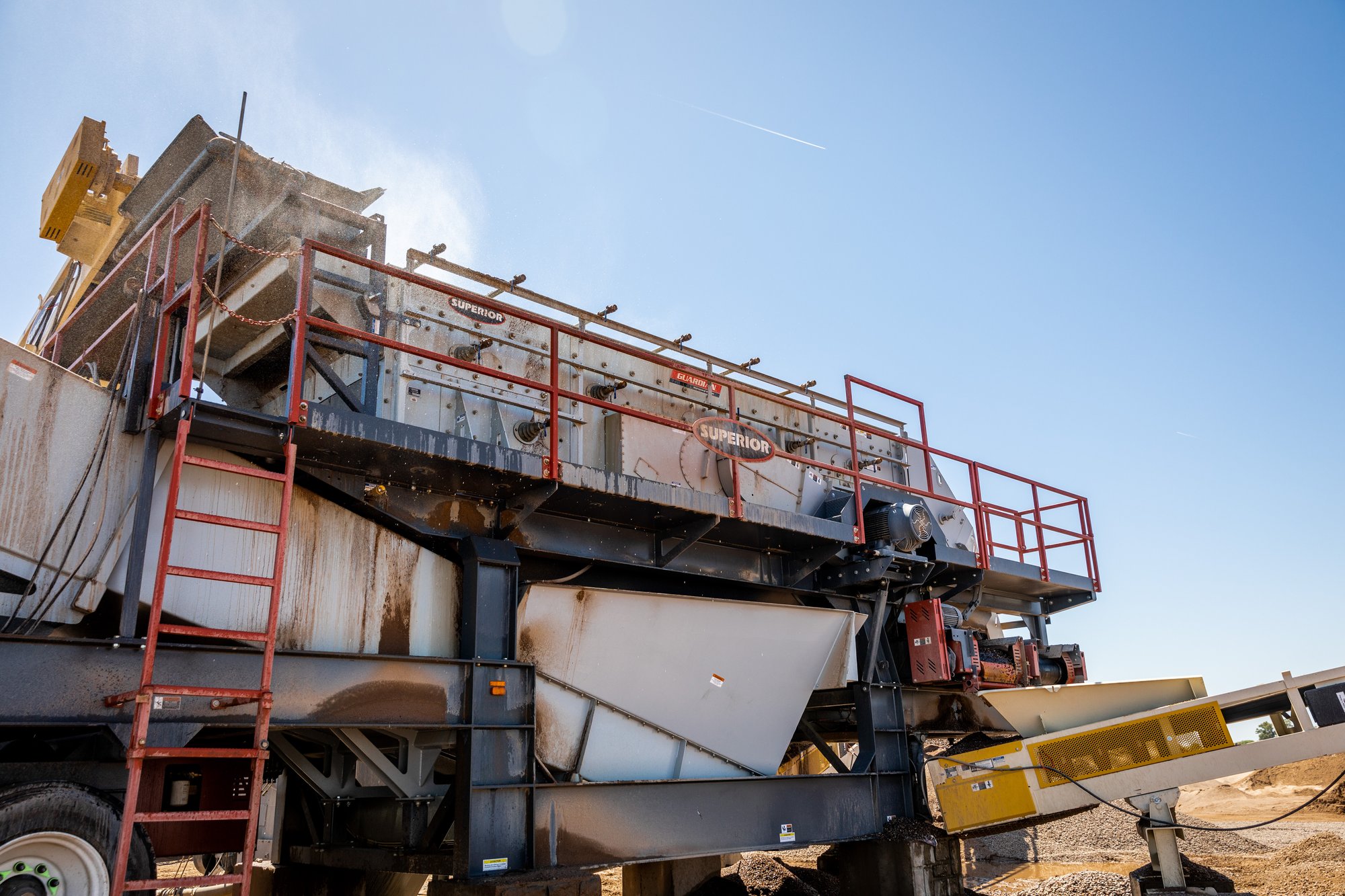
Faster Sand Sales and Lower Costs: Desert Aggregates’ Success with Modular Sand Plant
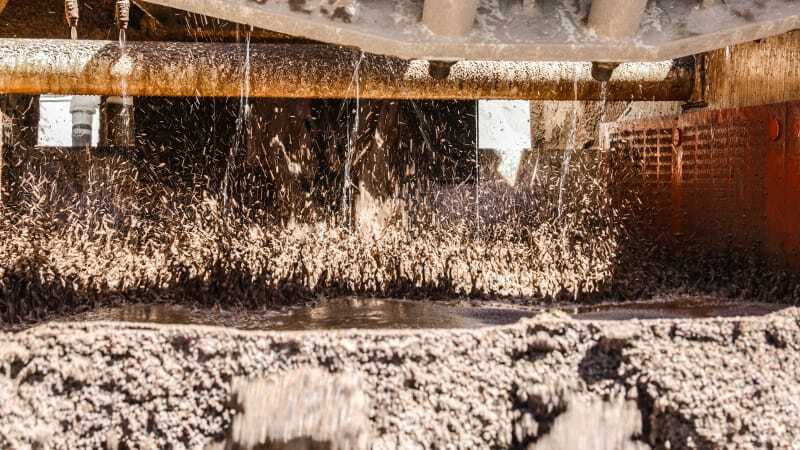
New Value From Crusher Fines: A Low-Water Solution for Manufactured Sand
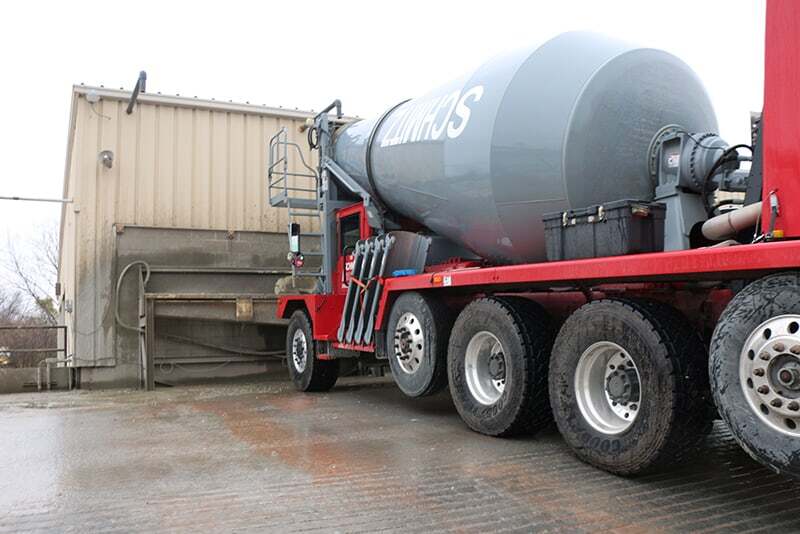