CASE STUDY
Capital Sand Company
- Jackson, Missouri
- LOCATION
- Frac Sand
- INDUSTRY
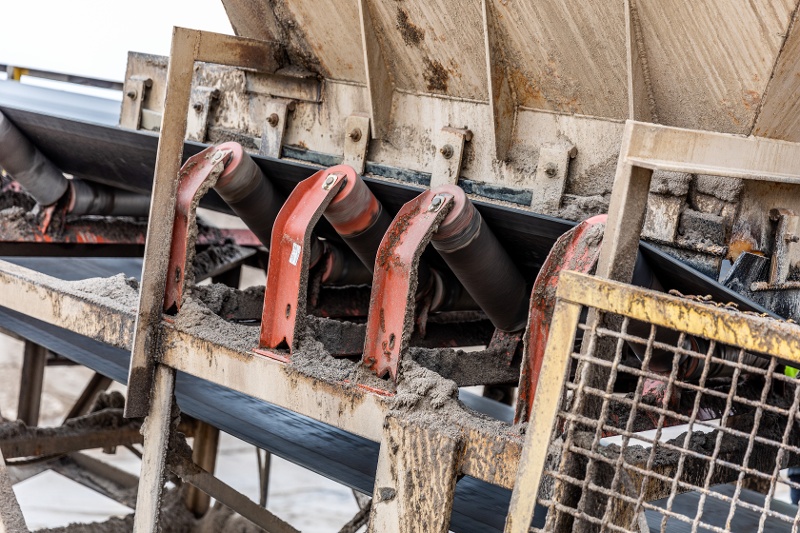
The Challenge
Capital Sand Company, Missouri's largest frac sand producer, faced persistent idler bearing failures at their critical wet feed hopper conveyor belt.
Plant Manager, Brandon Baker, frequently encountered issues with noisy roller sets and bearings wearing out prematurely due to contamination from wet and sticky feed materials. This frequent breakdown caused significant maintenance downtime, impacting the efficiency and cost-effectiveness of their operations.
“More than a year later, the new idler sets are still in place and we minimized maintenance downtime by eliminating the need for too frequent shutdowns to replace failed idlers.”
The Solution
To address the challenge, Capital Sand transitioned from a standard seal idler bearing seal design to the advanced SpinGuard® Titanium™ Seals by Superior Industries.
This next-generation seal technology was specifically chosen for its performance in moisture heavy, abrasive environments. The Titanium Seals were installed on the idlers at the wet feed hopper conveyor belt, providing enhanced protection against material contamination and wear.
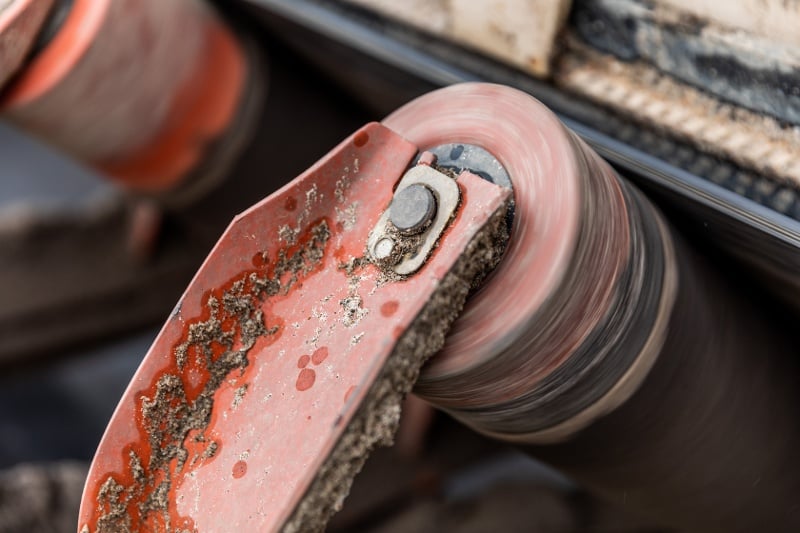
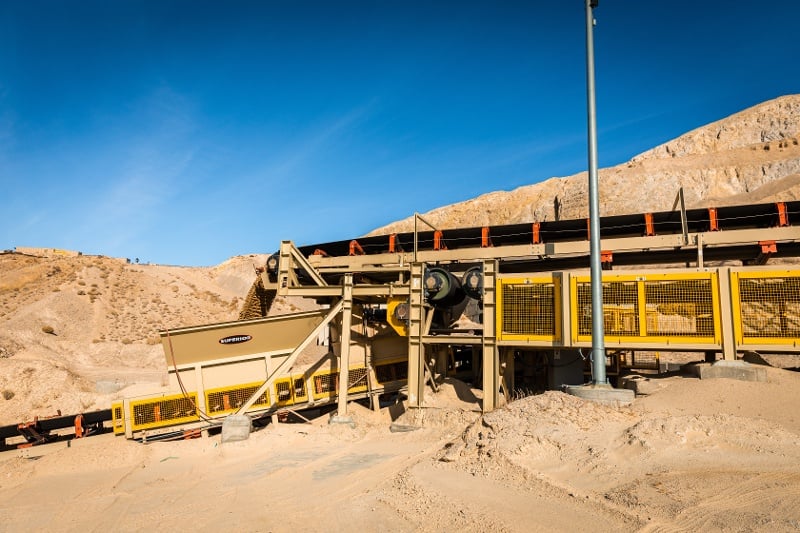
The Results
Over a year since the installation, the new Titanium Seals have proven to be highly effective. Maintenance downtime has been significantly reduced, with the company no longer needing frequent or daily shutdowns for idler replacement.
The advanced seal technology has not only extended the life of the idlers but also improved overall conveyor belt performance, contributing to greater uptime and enhanced cost-efficiency. Capital Sand plans to implement this technology across its other frac sand plants, further boosting operational profitability.
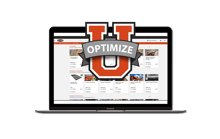
OptimizeU - Strategic Learning
Pursue greater production with comprehensive online courses in crushing, screening, conveying, and washing. Check out the premiere training resource in the construction aggregates industry.
More Projects & Resources
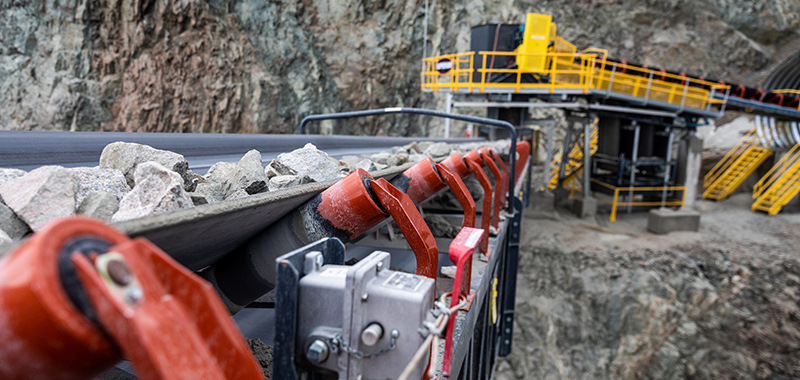
Conveyor Idlers: Don’t Overlook This Most Critical Component
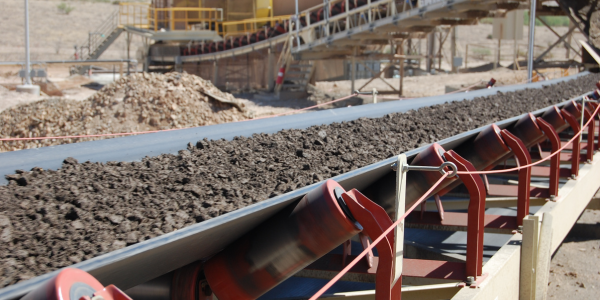
The Critical Role of Idler Bearing Seals in Protecting Belt and Profitability
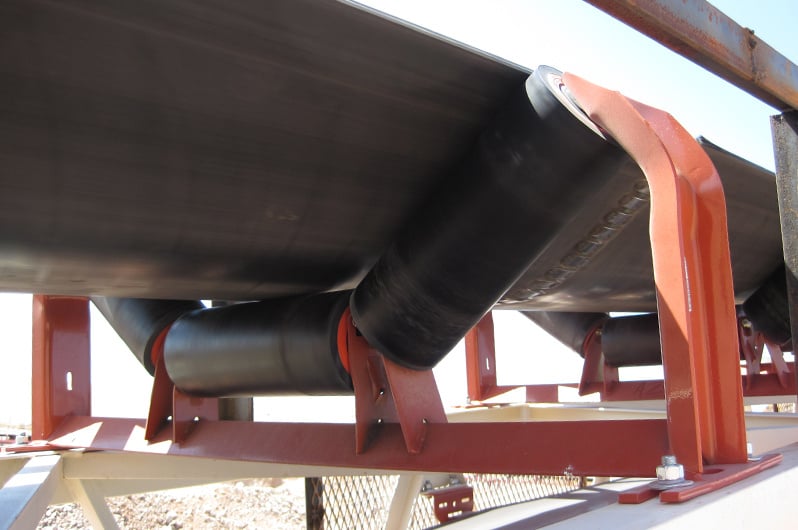