CASE STUDY
Rogers Group: Gallatin Quarry
- Gallatin, Tennessee
- LOCATION
- Aggregates: Sand & Gravel
- INDUSTRY
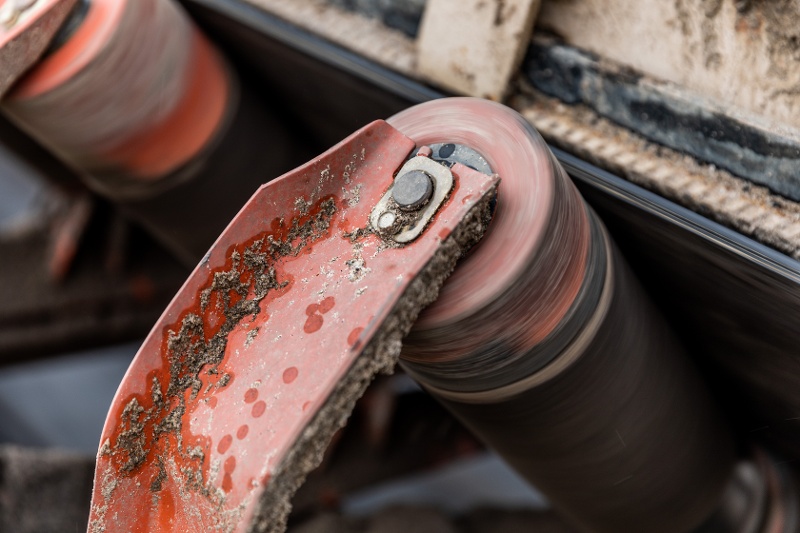
The Challenge
Aggregate operations, such as Rogers Group at its Gallatin Quarry, face significant challenges with belt protection under harsh conditions. Premature bearing contamination, caused by dust and moisture, often leads to idler lockup, belt damage, and excessive maintenance costs, impacting both productivity and profitability.
“Once we switched over to the Superior rollers, and saw how robust they are, we decided to stick with them. They really work well, and we’re getting great results.”
The Solution
Superior Industries redesigned the idler bearing seal, improving contamination resistance through extensive testing. The newly developed SpinGuard® Titanium™ Seals feature advanced sealing technologies for wet and dusty environments, prolonging idler and belt life. This innovative new seal design tackles moisture, dust, and heavy wear applications.
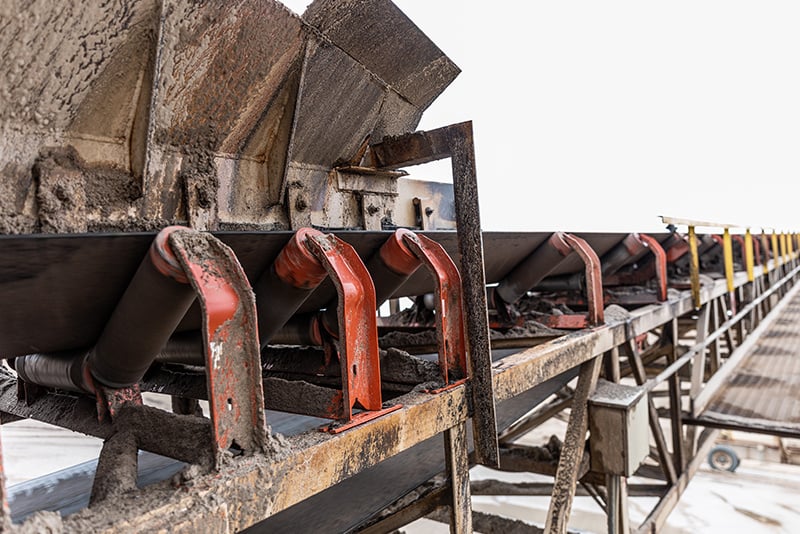
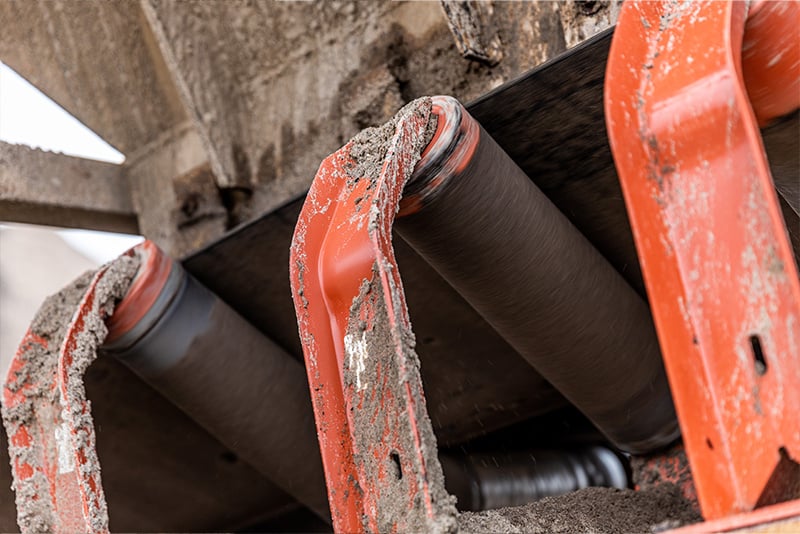
The Results
By implementing Titanium Seals, operators at the Gallatin Quarry have significantly reduced idler failure rates, extended equipment life, and improved uptime. The new seals helped them reduce costly maintenance while protecting the belt.
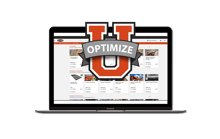
OptimizeU - Strategic Learning
Pursue greater production with comprehensive online courses in crushing, screening, conveying, and washing. Check out the premiere training resource in the construction aggregates industry.
More Projects & Resources
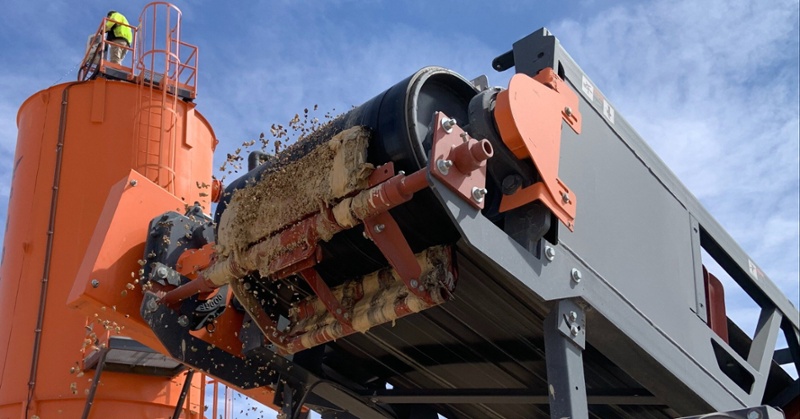
Consistency in Components: Standardization is Key for Conveyor Parts
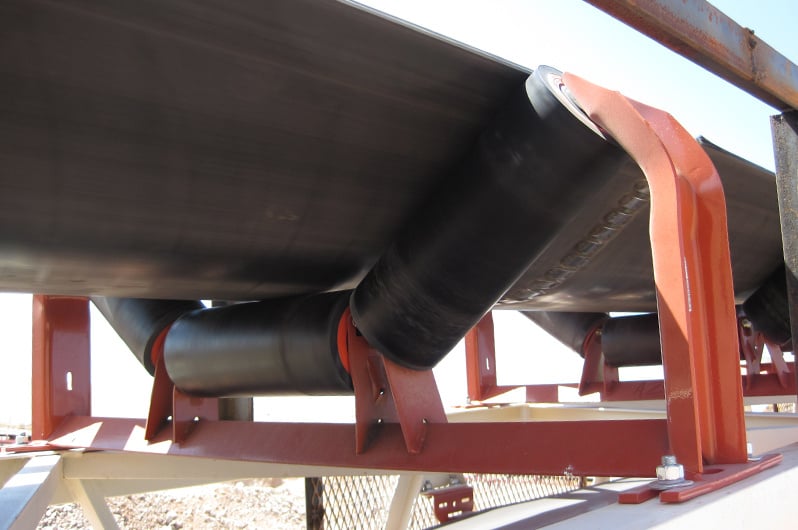
Harsh Application is Achieving 4x the Wear Life with Moxie® Rolls
