Tech Tip: Conveyor Idlers
Don’t Overlook This Most Critical Component
While the reliability of each conveyor component is key, it’s the often overlooked idler that should always receive its proper consideration. After all, idlers are spaced along the entire length of the belt, and it only takes one roll malfunction to delay material throughput or cause potential damage to costly belting.
Bottom line, if you maximize idler performance, you’ll add more to the profit stockpile. Here are some simple tips on getting the most from your idlers:
Access Replacement Tools
The market is shifting toward the use of replacement/retrofit rolls over the practice of chucking the entire idler. Typically, idler malfunction involves only one of three rolls, so why waste 75% of your investment?
Yes, producers have commonly chosen to replace the entire idler due to time and labor factors. Everyone wants to minimize conveyor downtime and few want to move the belt out of the way to replace one roll. Consequently, many operations are choosing to replace rolls in the shop during maintenance hours. The task is far simpler than it used to be, made easier by new idler design innovations that streamline installation. Plus, growing replacement roll demand has resulted in the affordability of built-to-order retrofit rolls that fit any frame brand or type.
Without a doubt, the use of readily available, adaptable, and easily changeable replacement rolls will save you big bucks.
Pay Attention to Bearing Seal Design
The heartbeat of an idler lies in the integrity of its seal and the protection of the bearings. Since an idler’s seal is typically its first fail point, it’s always best to closely scrutinize seal design. For example, current seal innovations may involve unique application-specific models; improved contact seals that result in less seal drag; triple labyrinth seals that increase the distance that contaminants must travel; and grease fills that easily trap contaminants.
Superior offers four application-specific conveyor idler seals. The SpinGuard® Wet Seal is targeted toward applications that experience excessive idler wear due to high moisture, frequent washdowns, and dredging; while the SpinGuard Dry Seal is ideal for operations that produce dust near crushing or screening equipment. The SpinGuard Low Drag Seal is an eco-friendly solution that addresses horsepower concerns in overland and longdistance conveying.
Eliminate Idler Pinch Points
Avoid premature roll failure by utilizing idlers that have no pinch points between the end stand and the outside roll. Pinch points will allow foreign material to lodge within them, causing the roll to seize up.
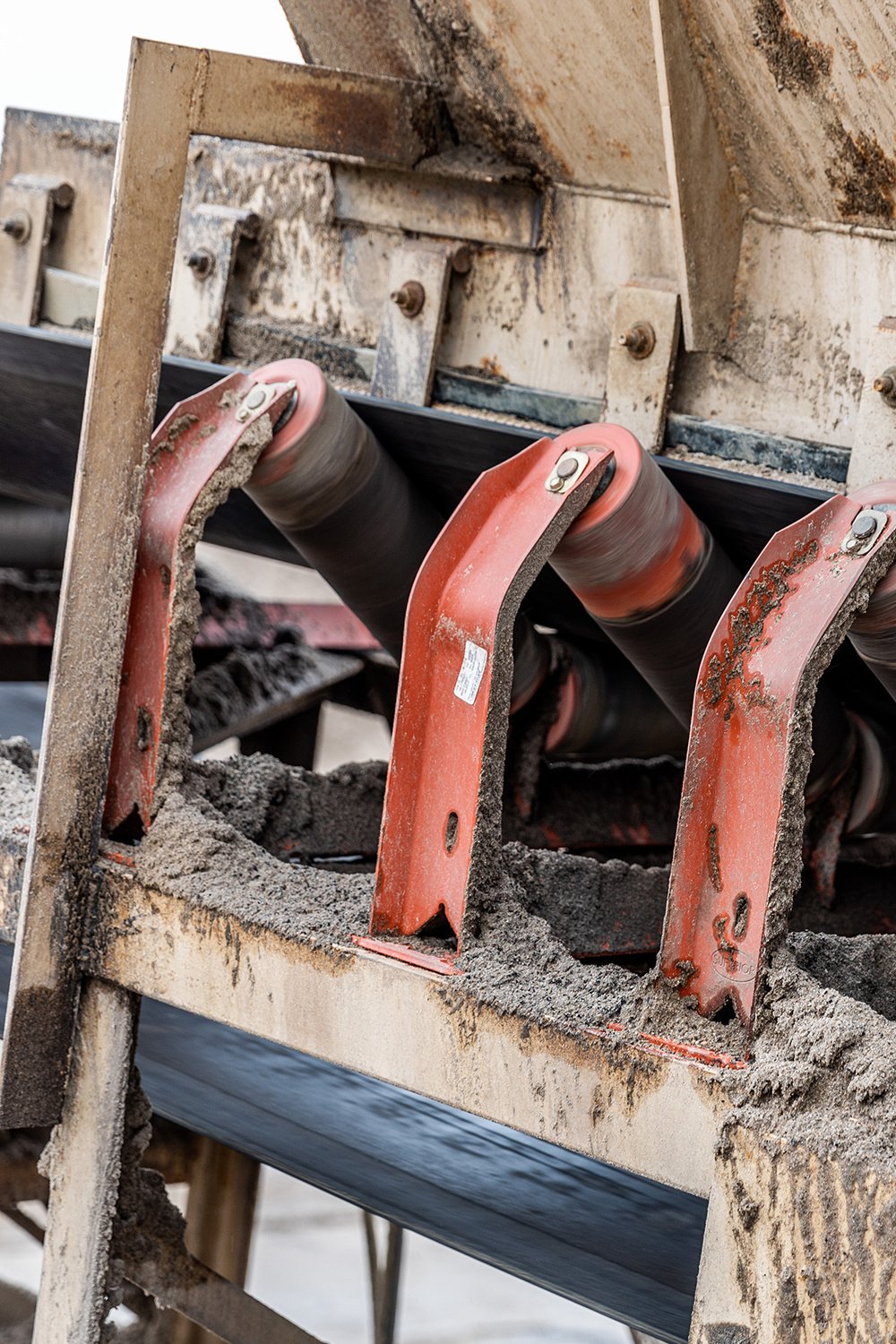
Ensure Adequate Frame Support
It’s critical to have extra idler frame strength and support where you most need it -- at loading and transfer points where forces and impact may cause frames to bend or twist. Consider the use of idlers with “flared” end stands, which deliver added strength especially in applications with large material lumps or where material feed is sideways versus straight on.
Today’s tight profit margins allow little room for error. Maximizing idler performance is just one more way that producers can lower costs per ton. With the availability of new, improved idler designs and cost-efficient replacement rolls, perhaps it’s high time to reap the benefits.
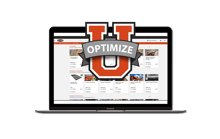
OptimizeU - Strategic Learning
Pursue greater production with comprehensive online courses in crushing, screening, conveying, and washing. Check out the premiere training resource in the construction aggregates industry.
Related Content
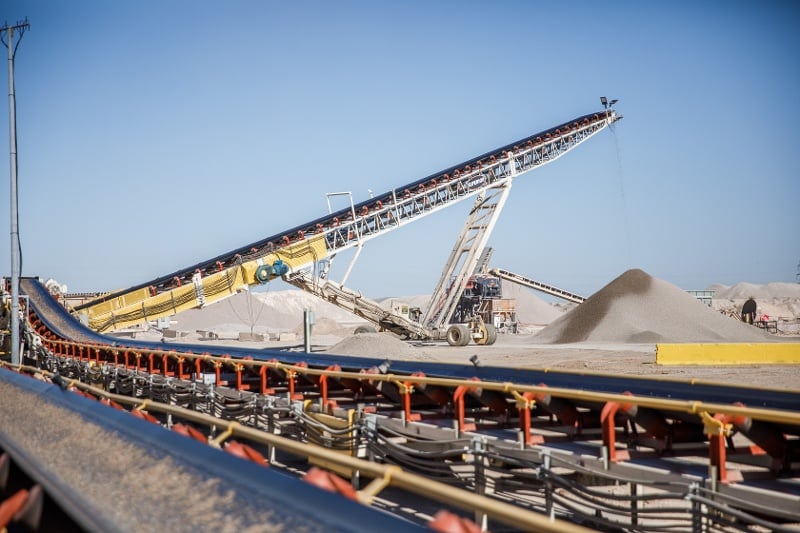
Consistency in Components: Standardization is Key for Conveyor Parts
Standardization is the key to savings and ease of maintenance. As each brand is not the same, choosing the lowest priced component could cost you more in the long run.
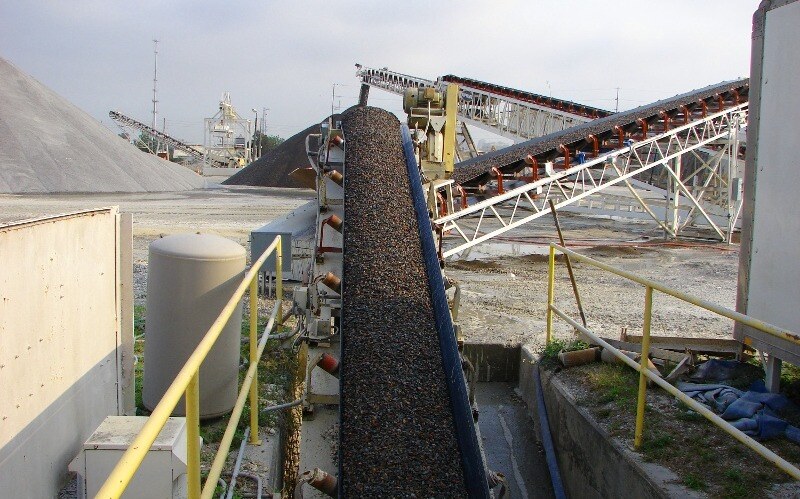
Conveyor Belt Mistracking: Causes & Cures
There's no need for a costly and complete system overhaul if a simple tweak will truly solve the problem.
-1.jpg?width=800&height=533&name=Pallets%20of%20Idlers%20Hero%20-%20Full%20Color%20(1)-1.jpg)
Vantage® Intelligent Idlers: The Superpowers of Smart Conveyor Idler Rolls
There’s no need for a costly and complete system overhaul if a simple tweak will truly solve the problem.
Talk to an Expert
Need more information? We'll get you in contact with a product expert in your area.