CASE STUDY
Scruggs Company
- Cook County, Georgia
- LOCATION
- Rail Terminal: Railcar Unloading
- INDUSTRY
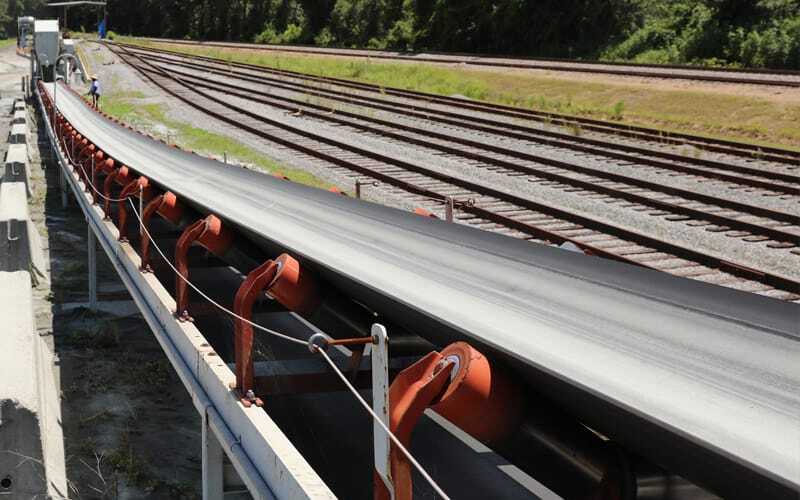
The Challenge
The Scruggs Company faced the significant challenge of managing the logistics for two I-75 lane widening projects in Georgia, requiring over 2 million tons of aggregate. With trucking costs, safety concerns, and material delivery timelines all on the line, the company needed a more efficient and cost-effective solution for transporting and stockpiling the massive amount of material required for these projects.
The solution had to minimize loader use, prevent material segregation, and integrate seamlessly with their new distribution center, which would support an onsite asphalt plant and two portable concrete plants.
“Without a TeleStacker Conveyor, we handle the material twice as much, wear out our loaders twice as fast, and increase costs of maintaining more operators.”
The Solution
To meet these demanding requirements, Scruggs Company turned to rail transportation combined with a customized material handling system designed by Superior Industries.
A dedicated 50- to 60-car unit train was utilized, with each railcar featuring a bottom-discharge unit to unload material into a surge pit. The material was then fed to a 240-ft overland conveyor, which in turn supplied an automated 190-ft TeleStacker Conveyor.
This setup allowed for the rapid, high-volume stockpiling of material, while significantly reducing the need for manual labor and eliminating the risk of material segregation. The integrated system was designed to maximize efficiency and ensure that the projects stayed on schedule.
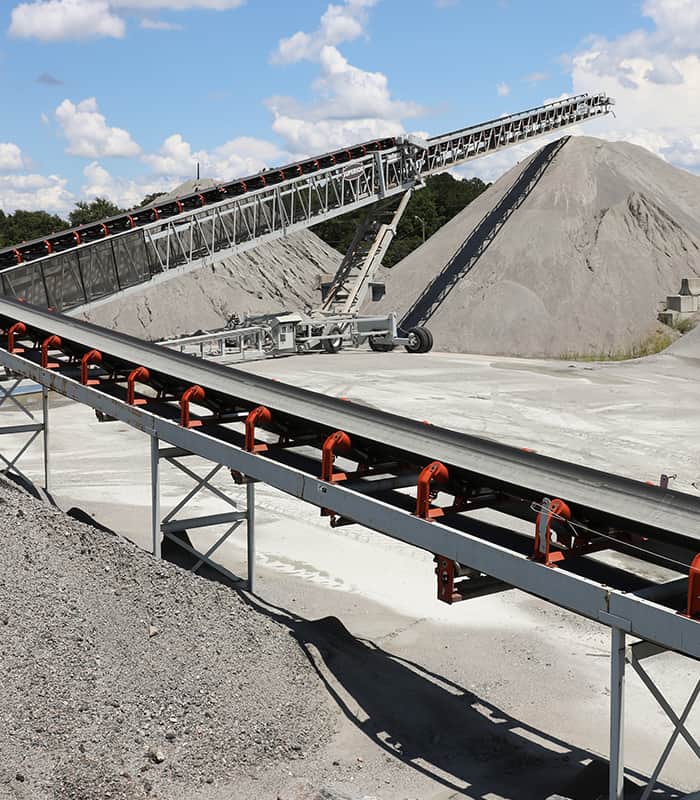
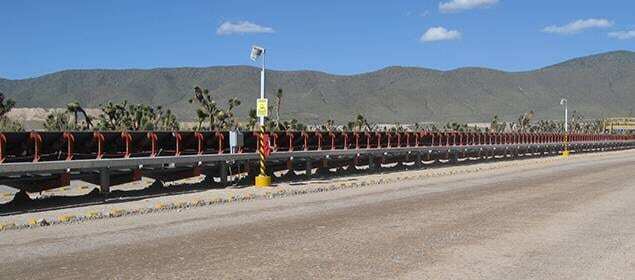
The Results
The combination of rail transportation and advanced material handling technology enabled the Scruggs Company to meet its high-volume delivery and stockpiling goals efficiently.
The unit train was able to unload up to 6,000 tons of aggregate in just six hours, significantly reducing the time and costs associated with trucking the material.
Moreover, the use of the TeleStacker Conveyor not only increased stockpile capacity by 30% but also reduced equipment wear and tear and minimized labor requirements. The success of this approach has positioned the Scruggs Company to continue benefiting from this setup for future projects, ensuring sustained growth and market leadership in the region.
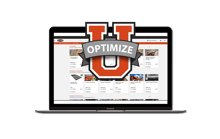
OptimizeU - Strategic Learning
Pursue greater production with comprehensive online courses in crushing, screening, conveying, and washing. Check out the premiere training resource in the construction aggregates industry.
Related Content
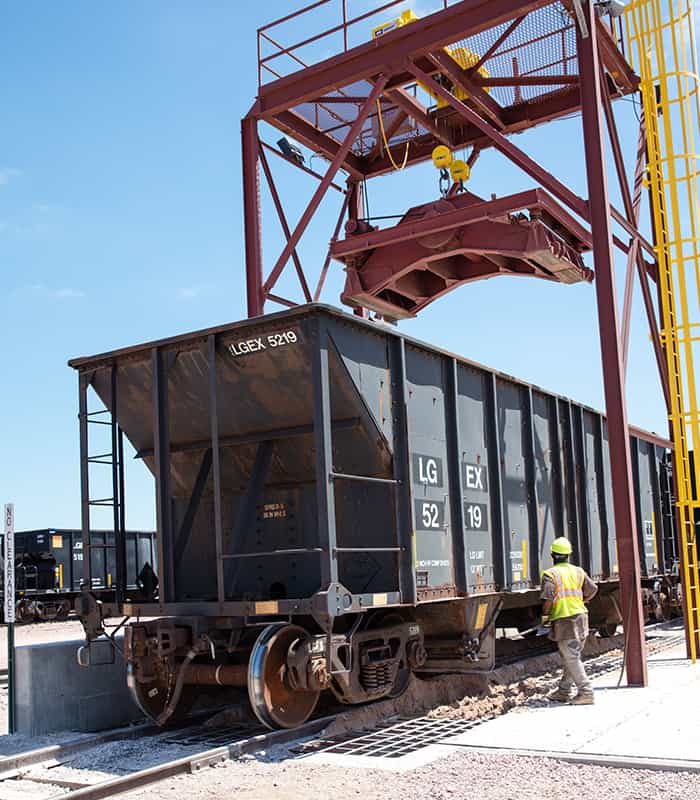
L.G. Everist Cuts Unloading Time in Half, Managing 100 Railcars in Just 10 Hours
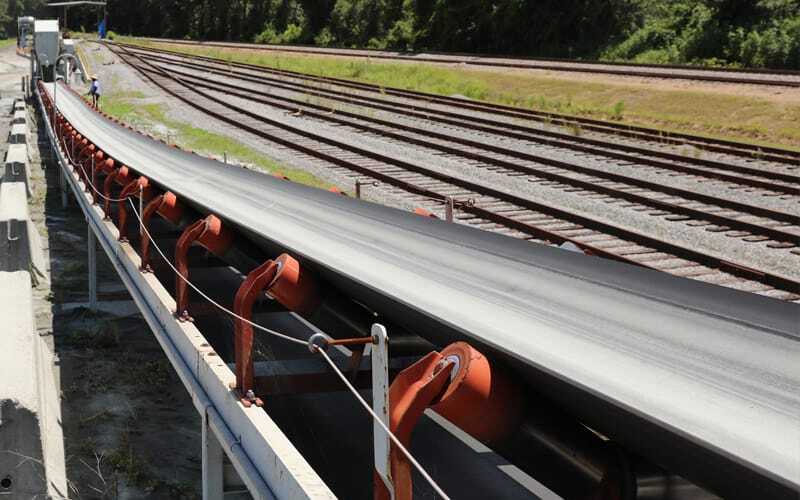
Scruggs Company Boosts Stockpile Capacity by 30% with Superior’s TeleStacker Conveyor
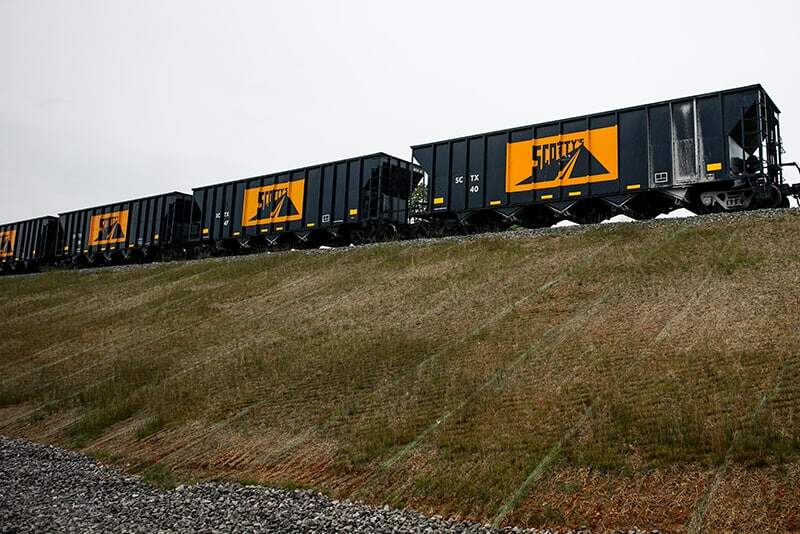
Scotty’s Contracting Chooses Superior for Railcar Unloading Allowing it to Increase Sales