Next Level Cone Automation That Puts Dealers in Control
Superior's new automation manager, Shamus Coughlin, offers a rundown of the new Vantage® Crusher Automation, detailing how dealers are in for an improved experience.
PUBLISHED: FEBRUARY 2025
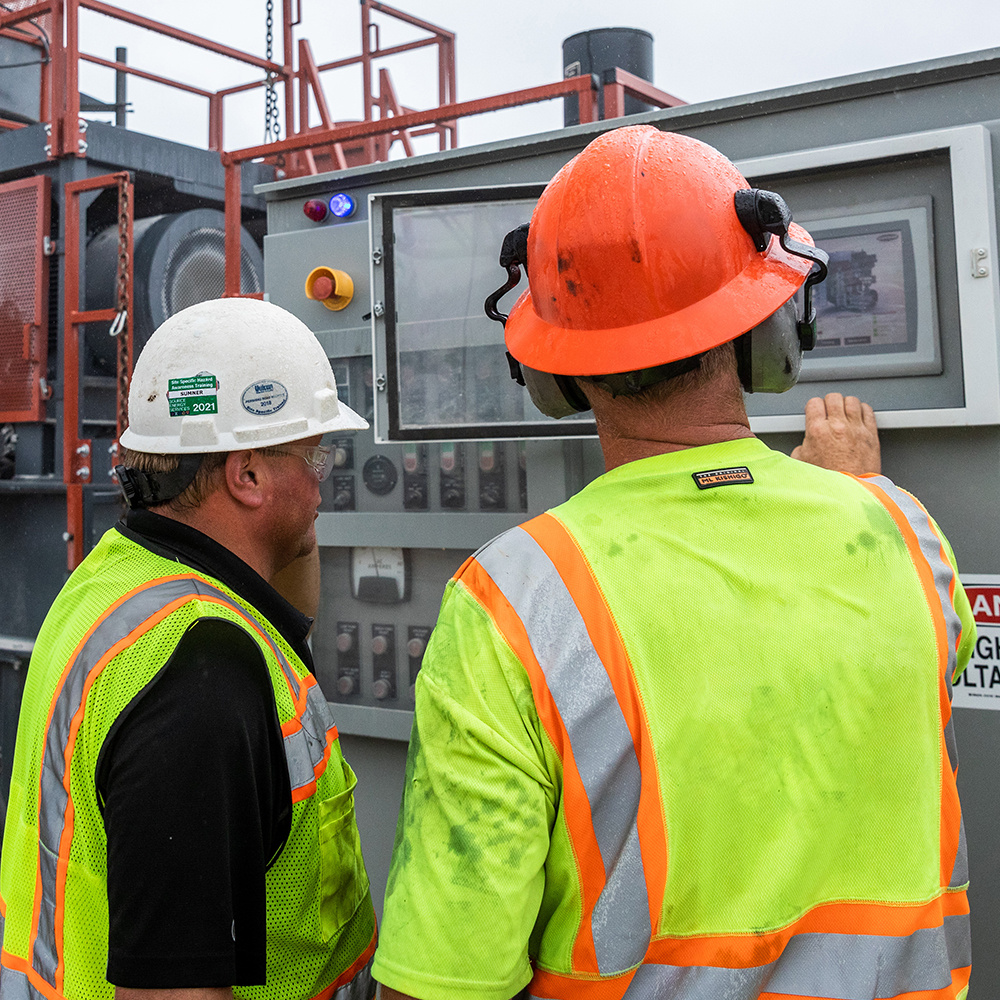
Call them suggestions, complaints, or perhaps even grievances. Regardless, dealers and end users periodically delivered them about Superior's Vantage Automation for cone crushers.
When issues arose in the field involving the control platform, engineers at Superior not only worked the problem, but took lasting notes. Over the course of several years, team members built a list of items – ones based on real-world experiences – that drove the next generation of Vantage Automation.
Listening, Learning, and Improving
As Superior’s Shamus Coughlin describes, that list grew to more than 100 items. He says Superior addressed 90% of them with version 7.2, which was released last month.
“We took it to heart when people would call in and need support,” says Coughlin, automation manager at Superior. He joined the company last June after 17 years with Astec (and a short stint in between with McCourt Equipment).
Sensors were sometimes at the center of automation issues, according to Coughlin. While end users sought data about their crushers, some of the sensors providing it were more problematic than they were worth.
In the end, feedback from end users afforded Superior the opportunity to strike a better balance between the data that’s critical to operations and the kind end users can do without.
“If you want data to protect and run the machine, you need to have enough sensors and electronic modules,” Coughlin says. “It’s finding a balance of what is enough to get the data you need, but not so many delicate parts that they become more of a nuisance."
“We don’t want to be a cause of downtime, so our job in the automation department is finding the right balance,” Coughlin says.
The new Vantage Automation v7.2 interface streamlines calibration with intuitive visuals and simplified navigation, making setup and troubleshooting easier for operators and dealers.
A Smarter, Simpler User Experience
One goal Superior had with its update was to simplify the user experience with Vantage Automation. The new touchscreen is a means of doing so.
“The big changes all come in the touchscreen interface,” Coughlin says. “It’s what the operator uses to perform all the functions on the crushers and it's the biggest of our improvements.”
With the new interface, operators can now troubleshoot issues on the spot—without needing an engineer or programmer on-site. The goal is to make problem-solving faster and more intuitive, reducing the need for remote support from a Superior technician.
When cone crusher problems arise now, the new Vantage Automation allows for solving those more efficiently.
“Setting up the machine quickly to get it functional and crushing is important,” Coughlin says. “So, when you do have an issue, quickly pinpointing the source is important.”
And with end users now more easily able to uncover such issues, the dealer experience should be simplified too.
“In many cases, our dealers shouldn't have to call Superior for help,” Coughlin says. “They can use the alarms and the data right on the screen to troubleshoot the problem.”
The overall experience is a more pleasant one, he adds.
“Navigating through all the screens is so much easier,” Coughlin says. “We updated the images to be easier to read in the bright sunlight and grouped data together where it makes more sense – especially for people who aren’t as familiar with the machine at first.”
Managing warranty claims should be simpler following the update, as well.
“When you have data on what actually happened over time, then you can lay out the event a little more clearly and get a better picture of what happened," Coughlin says. "That’s becoming more critical and important.”
In case you missed it... New Automation for TeleStacker® Conveyors
Stronger Support, Faster Solutions
Since Superior designs and builds its automation programs in-house, problem-solving is quicker, too.
“At Superior, we believe our engineers and automation team should know our crushers better than anyone,” Coughlin says. “Because we design and build the control systems ourselves, we have an intimate understanding of how they work with the machines—allowing us to provide the best possible support.”
The Vantage 7.2 update reflects that approach’s value.
“When a dealer or customer calls in for support and the automation team answers, it’s refreshing for them to know they’re talking to the people that actually programmed that system,” Coughlin says. "That’s uncommon for other companies.”
With 7.2, Superior also combined separate programs for Patriot® Cones and Dakota® Cones into one interface.
“The two cones work very similarly,” Coughlin says. “By unifying the control logic, we’ve made it easier for dealers to manage both crushers without having to learn separate systems. This streamlines training, simplifies troubleshooting, and ensures a more consistent user experience.”
Other Content This Month
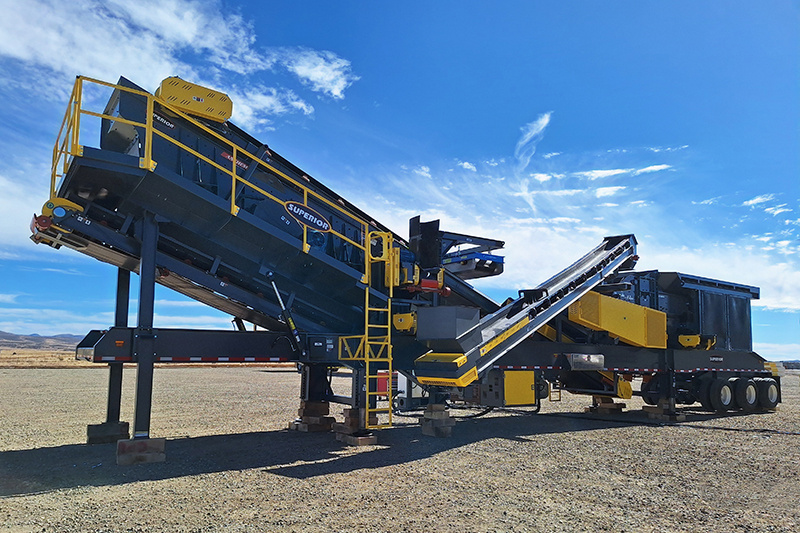
Why More Operators Are Choosing Sentry HSIs
Superior’s product management team shares how Sentry® Horizontal Shaft Impactors are gaining traction with end users, thanks to unmatched simplicity and flexibility.
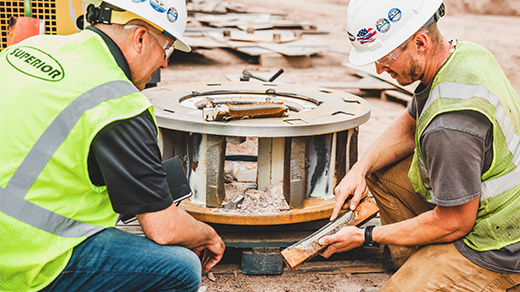
The High Stakes World of VSI Maintenance
With the presence of Superior’s VSI crushers growing, now is the time to brush up on critical inspection practices to keep these high-speed machines performing their best.
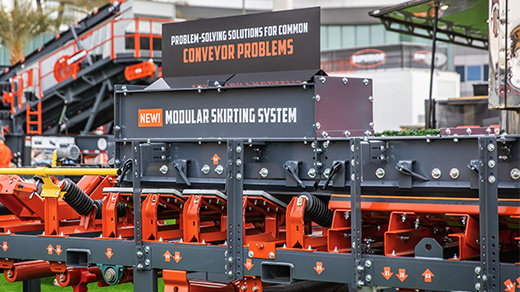
AGG1 2025: What Dealers Need to Know
After back-to-back years in Nashville, AGG1 is making its first-ever stop in St. Louis—where show planners still expect near-record attendance (with a little less honky tonk).