The High Stakes World of VSI Maintenance
With the presence of Superior’s VSI crushers growing, now is the time to brush up on critical inspection practices to keep these high-speed machines performing their best.
PUBLISHED: FEBRUARY 2025
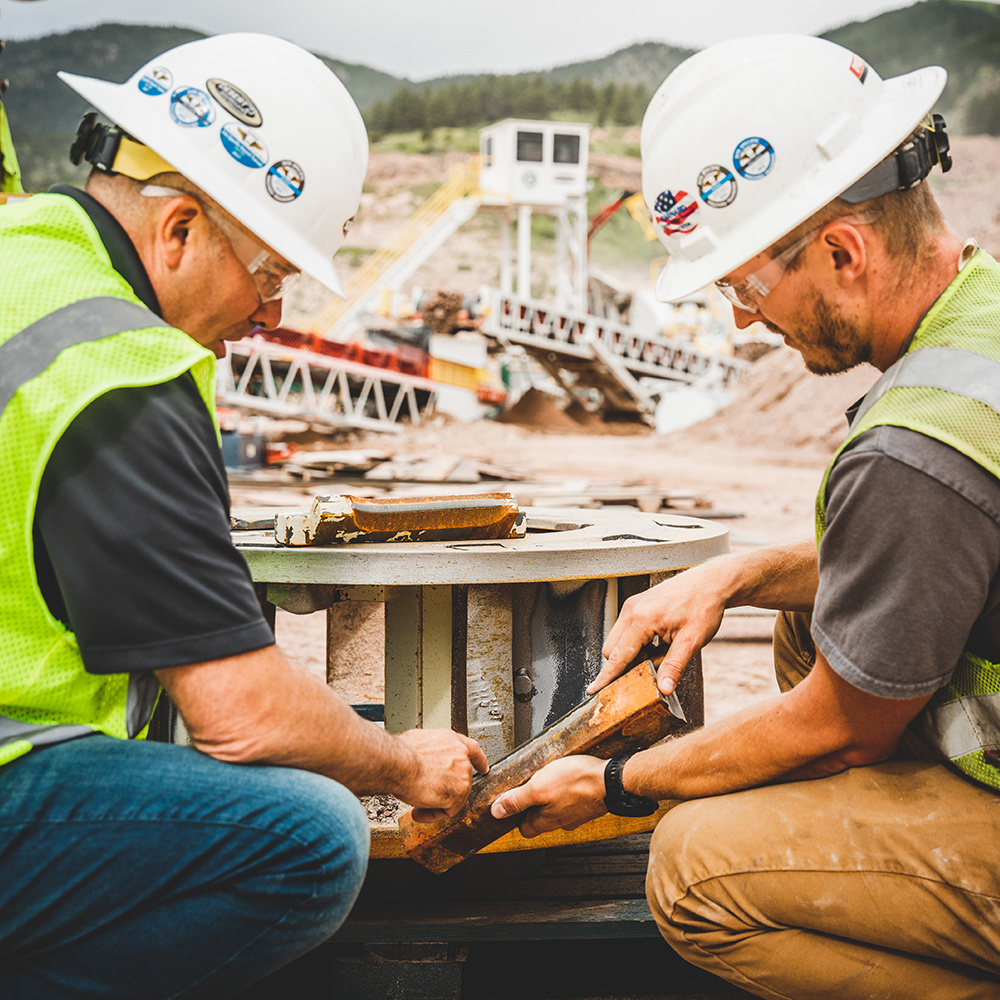
Superior’s presence in the VSI crushing market has grown significantly since acquiring the former CEMCO in late 2023. With market share tripling last year, it's a good time to reinforce the importance of regular inspections and proactive maintenance.
Why Frequent Inspections Matter
Unlike compression-style crushers, a VSI relies on continuous, high-speed impact to fracture material. That means wear occurs faster, and even a single neglected component can throw the machine out of balance. Regular maintenance isn’t just beneficial for a VSI—it’s essential to keeping it running safely and efficiently.
To understand just how critical maintenance is, we spoke with Kyle Ruschmeyer, one of Superior’s boots-on-the-ground crusher service technicians. He’s seen firsthand what happens when VSI maintenance is overlooked.
“Without frequent inspections, worn components can throw the machine out of balance, causing excessive vibration and structural damage,” says Ruschmeyer. “I’ve seen material wear right through the anvils and start cutting into the crusher body itself—turning a simple fix into a major repair.”
According to Ruschmeyer, well-organized operators inspect their VSI crushers at the beginning or end of each shift to catch wear and misalignment before they cause larger issues. In high-abrasion applications like manufactured sand production or crushing quartzite, inspections may be necessary as often as every four hours.
Cemco T80 VSI Components Identification
Critical Checkpoints: Key Areas to Watch
A well-maintained VSI crusher delivers consistent product quality, reduced downtime, and longer component life. Here’s a breakdown of the critical areas to inspect and what to look for to prevent performance issues and costly repairs.
Rotors & Wear Parts
The rotor is the heart of a VSI crusher, spinning at high speeds to propel rock into wear surfaces. An unbalanced or worn rotor can cause excessive vibration, reduced efficiency, and structural damage.
- Rotor Tips: These take the brunt of the impact, shattering material upon contact. Look for rounding, chipping, or excessive wear, as this reduces efficiency.
- Table Liners: They shield the rotor’s base from wear. Inspect for uneven patterns, cracks, or thinning, and replace before exposing the frame to impact.
- Rotor Balance: Replacing worn parts without balancing causes vibration. Always replace opposite components together for even weight distribution.
Bearings & Lubrication System
The high speed operation of VSIs places a significant load on the bearings. Proper lubrication is critical to preventing premature wear, overheating, and catastrophic bearing failure.
- Oil Levels & Flow Meters: Ensure lube oil is at the correct level and circulating. Low oil levels lead to overheating and increased friction.
- Oil Contamination & Temperature: Watch for water contamination, metal shavings, or sludge. Rising oil temperature indicates friction or cooling failure.
- Bearings & Seals: Check for leaks, overheating, or excessive movement. Any sign of leakage or unusual vibration requires immediate attention.
- Vibration Monitoring: VSIs have shutdown switches for excessive vibration. Frequent trips may indicate rotor imbalance, wear, or bearing issues.
Anvil Ring & Crushing Chamber
The crushing chamber is where rock fractures upon impact. VSI crushers use either anvil rings (rock-on-steel) or rock shelves (rock-on-rock) for material reduction.
- Anvil Condition: Anvils absorb high-impact, so inspect for wear, cracks, or misalignment. Never wear down to the base or risk frame damage.
- Chamber Lining: In rock-on-rock crushers, check for material buildup that disrupts impact patterns and reduces efficiency.
- Material Build-Up: Excessive accumulation of fines or uncrushed material can block flow, reduce shape quality, and cause uneven wear on surfaces.
Lid, Feed Hopper & Feed Tube
The feed system controls material entry into the rotor. Blockages, misalignment, or excessive wear can disrupt crushing performance.
- Lid Seal: Ensure it's securely closed and sealed to prevent dust ingress. Loose seals allow fine particles to escape, accelerating wear on other components.
- Hopper Wear Plates: These protect hopper walls from material abrasion. Inspect for excessive wear, cracks, or instability.
- Feed Tube Alignment: A misaligned or excessively worn feed tube causes uneven material flow, leading to imbalanced rotor wear.
A destroyed rotor caused by an over-torqued bolt that snapped, allowing a feed disc to bounce freely during operation.
The Payoff of Proactive Maintenance
Regular VSI inspections takes time, but the cost of skipping is far greater.
“It doesn’t take much – one worn part left unchecked – and suddenly your customer has a much bigger problem on your hands,” says Ruschmeyer. “A few minutes of inspection can prevent days of downtime and thousands in repairs.”
Staying ahead of wear doesn’t just extend VSI life, it keeps production on track and prevents shutdowns that cut into profitability.
Other Content This Month
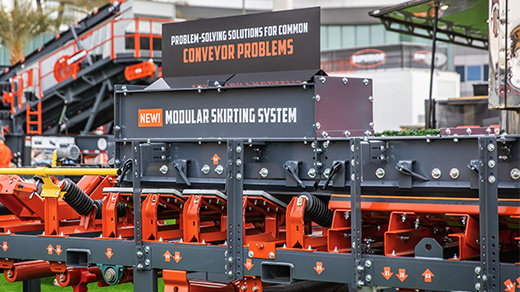
AGG1 2025: What Dealers Need to Know
After back-to-back years in Nashville, AGG1 is making its first-ever stop in St. Louis—where show planners still expect near-record attendance (with a little less honky tonk).
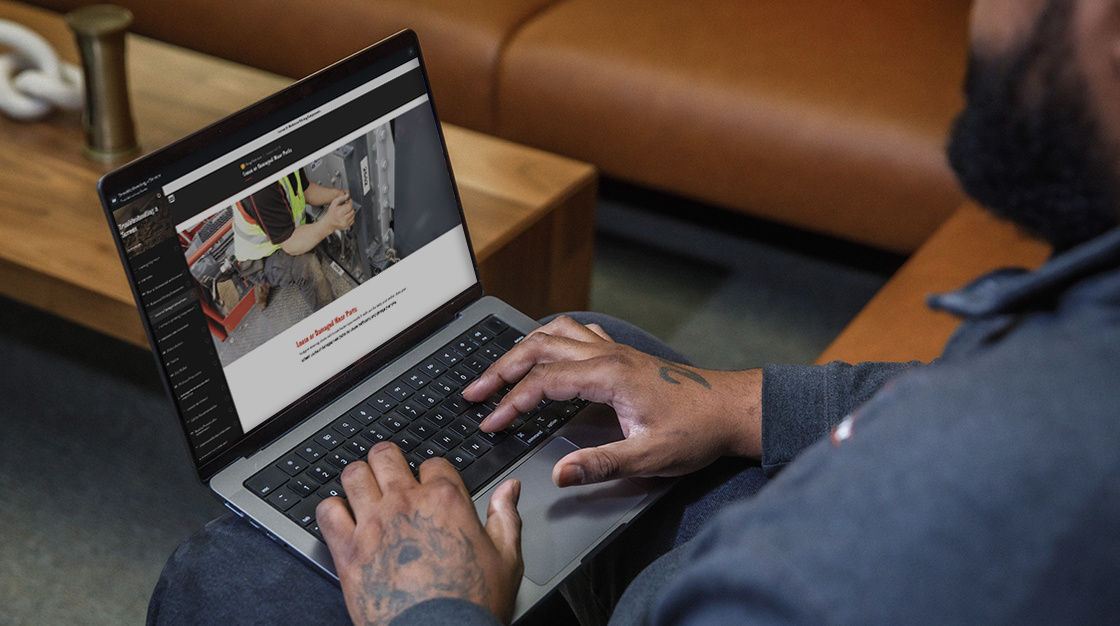
OptimizeU: On-Demand Training for Dealers
Dealers can now access OptimizeU, designed to sharpen product knowledge, improve troubleshooting skills, and enhance sales expertise.
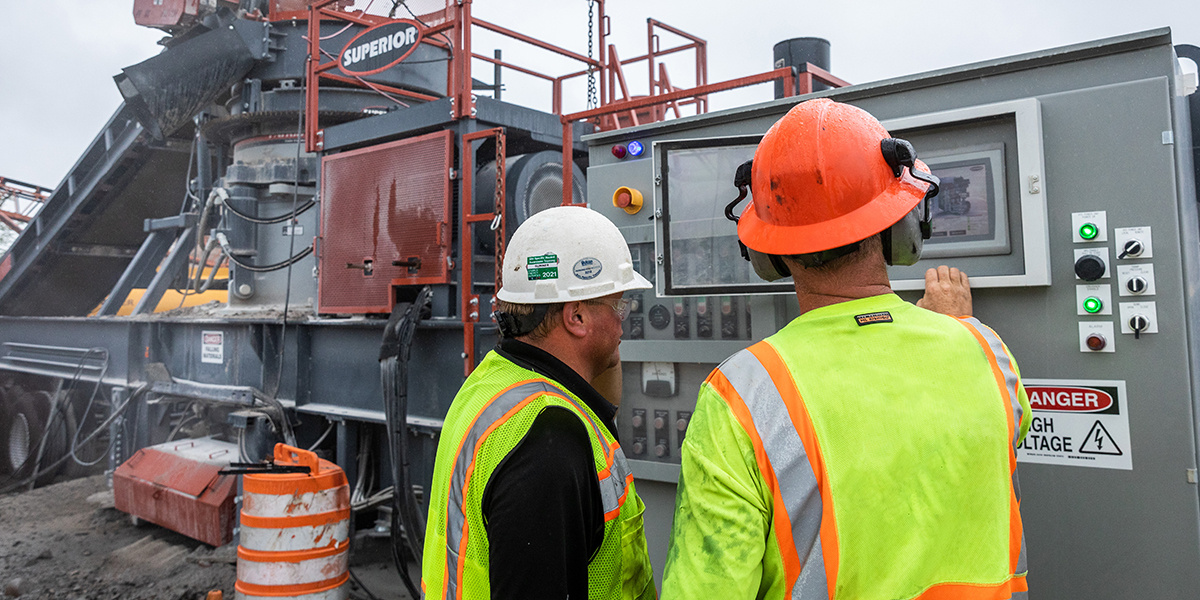
Next Level Cone Automation That Puts Dealers in Control
Superior's automation manager offers a rundown of the new Vantage® Crusher Automation, detailing how dealers are in for an improved experience.