Tech Tip: Conveyor Belt Splicing
Which Method is Best?
For every conveyor application, the ends of each belt must be joined together to create a continuous belt. Even the most highly engineered belt specification is only as good as its splice. When determining which splicing method is best the operator must consider the benefits of the two common splicing methods: vulcanized or mechanical.
Is there a clear choice between these two methods? Consider this simple rule: For the permanent splicing of a conveyor belt, vulcanized splicing is most often the best choice; however, when a belt must be rejoined frequently, mechanical fasteners may be preferred.
Vulcanized Splicing
There are two methods of vulcanized splicing: hot and cold. Hot vulcanized splicing requires time, temperature, and pressure to complete the process of joining the ends of a belt together. Cold splicing relies on chemical adhesives to properly vulcanize the ends of the belt together.
Special equipment and expertise are required when utilizing the hot vulcanized splicing method. The ends of the belt to be joined together are stripped in a “stair-step” manner, overlapped and bonded together using splicing rubber and then cured using a heated press and pressure.
The cold method requires the ends of the belt to be stripped in the same stair step manner as hot vulcanized splicing or the ends are skived (thin, bevel, or cut away layers of a material) to provide the required overlap and then the belt’s layers are bonded back together with adhesive which cures at room temperature.
Advantages | Disadvantages |
Strong, seamless belt joint Ideal for heavy-duty loads Longer splice service life Resistant to moisture, debris No metal parts to fail |
Requires specialized equipment Time-consuming field process Needs skilled labor to perform Longer downtime for installation Not easy to inspect visually |
Mechanical Splicing
The mechanical fastener alternative involves connecting rows of metal fasteners that are attached to each belt end. They are the preferred method for making in-the-field repairs, such as adding belt length and patching holes or tears. There are many types and sizes of mechanical fasteners. As belt manufacturers will tell you, "One size does not fit all." In other words, don't rely on one type or size of fastener for all belts just to cut down on inventory requirements. Always use the correct fastener that has been designed specifically for the belt and application.
Proper mechanical fastener selection involves belt thickness, operating tension, and pulley diameter. All three criteria must be considered when selecting the proper fastener for any application.
Advantages | Disadvantages |
Quick and easy installation Minimal downtime required Simple tools, no heat needed Easier to inspect and repair Suitable for emergency fixes |
Weaker than vulcanized splice Prone to snagging and wear Metal fasteners can damage parts Not ideal for high tension Shorter service life overall |
Never Skimp on Splicing
Don't skimp on splicing. Splice failures can result in employee injury, equipment damage and unnecessary or unplanned downtime. Invest in the time and training required to achieve optimum splice wear life. If a vulcanized splice is chosen, make certain the selected service company is certified by the belt manufacturer and follows the belt manufacturer’s specifications concerning safety, splicing techniques, procedures, and splicing materials.
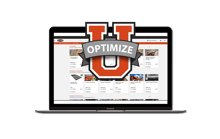
OptimizeU - Strategic Learning
Pursue greater production with comprehensive online courses in crushing, screening, conveying, and washing. Check out the premiere training resource in the construction aggregates industry.
Related Content
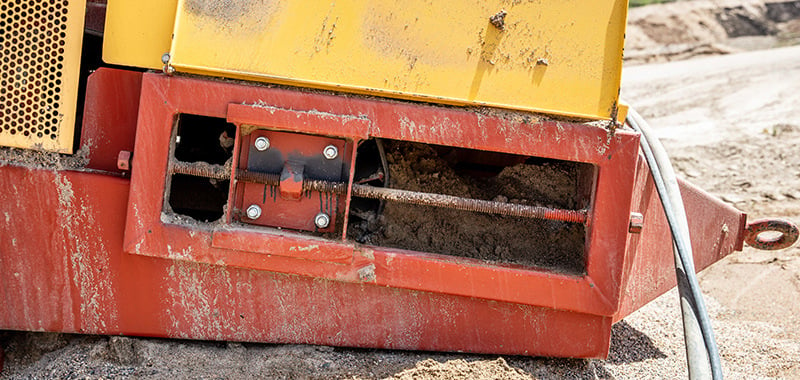
Conveyor Belt Tension: A Simple, Solid Approach
Ensuring proper belt tension is a vital issue in conveyor operation that affects belt tracking, performance and service life.
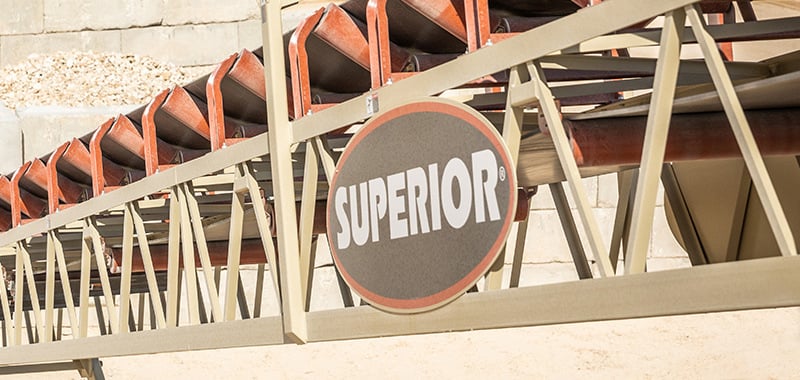
Conveyor Maintenance: Basic Design to Increase Your Uptime
Designing a conveyor to be maintenance friendly means providing adequate provisions for necessary service from the onset.
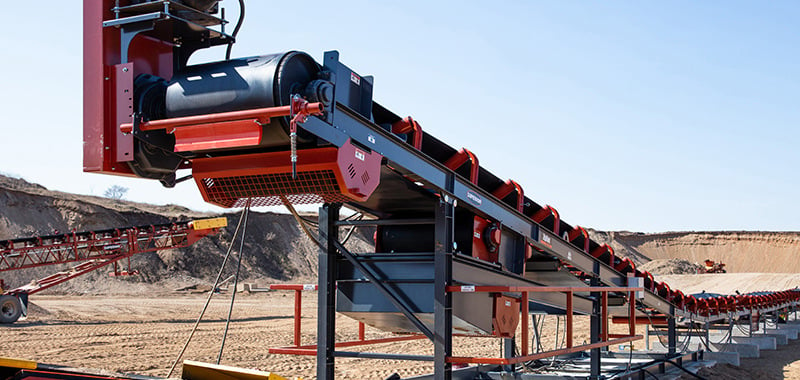
Conveyor Snub Pulleys: A Simple Solution to Belt Slippage
Mounted close to the drive pulley, the snubs primary job is to increase wrap angle around the drive pulley, thereby increasing traction.
Talk to an Expert
Need more information? We'll get you in contact with a product expert in your area.