Tech Tip: Conveyor Snub Pulleys
Belt slippage means costly downtime. By the time you’ve shoveled out the resulting material spill at the tail end of the conveyor, you know that the problem needs to be solved. The use of a snub pulley is one solution.
Mounted close to the drive pulley on the return side of the belt, the snub pulley’s primary job is to increase the angle of wrap around the drive pulley, thereby increasing traction. Its secondary purpose is reducing belt tension, which is important in maximizing conveyor component life.
.png)
In the absence of a snub pulley, should slippage occur, you can increase the co-efficient of friction by installing a ceramic-lagged pulley in the place of the rubber-lagged pulley. Note that in some cases, the conveyor framework may not easily allow the addition of snub pulley, so a ceramic lagged pulley is often the answer. Is adding a larger diameter pulley and answer as well? Many think it is; however, there is no theory that says that a larger diameter pulley will deliver greater traction. Bottom line, you must either increase the angle of wrap or increase the coefficient of friction.
The downside to snub pulley operation is possible material buildup, as the snub is running on the dirty side of the belt. You should install a good belt cleaner that provides even contact with the belt. Also, a ¼-inch (6mm)smooth rubber lagging should be applied to the snub pulley drum.
According to the Conveyor Manufacturer’s Association (CEMA), the use of a snub pulley is subject to the following limitations:
• Diameter is limited by belt specifications
• Suitable clearance between pulleys for belt replacement
• Must be below deck plate or underside of carry idlers
These limitations restrict a snubbed drive to an angle of wrap not exceeding 240°. If a greater angle of wrap is necessary, a dual-pulley drive may be required.
Snub pulleys do add maintenance costs and engineering time. Again, this is why it is important to be familiar with the intended application. If you know that you will have wet or dusty material characteristics, and that you will need more than 180 degrees of wrap, a snub pulley is recommended.
Yes, there’s a little more maintenance, but it’s cheaper to design in a snub upfront, rather than adding a ceramic lagged pulley later. The snub pulley is just as effective.
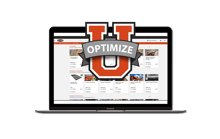
OptimizeU - Strategic Learning
Pursue greater production with comprehensive online courses in crushing, screening, conveying, and washing. Check out the premiere training resource in the construction aggregates industry.
Related Content
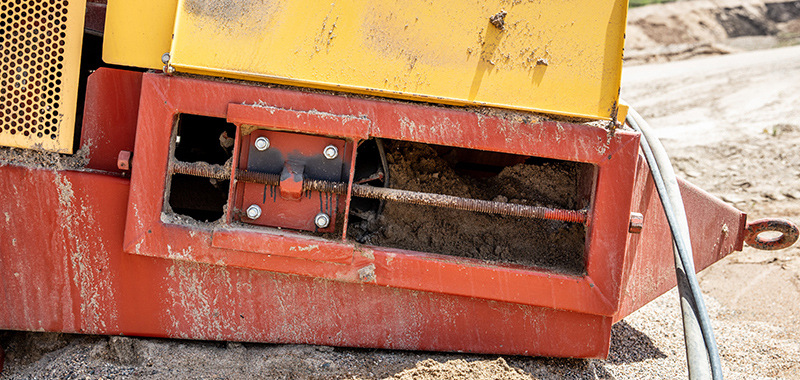
Conveyor Belt Tension: A Simple, Solid Approach
Ensuring proper belt tension is a vital issue in conveyor operation – one that affects belt tracking, overall belt performance, and the life of the belt itself.
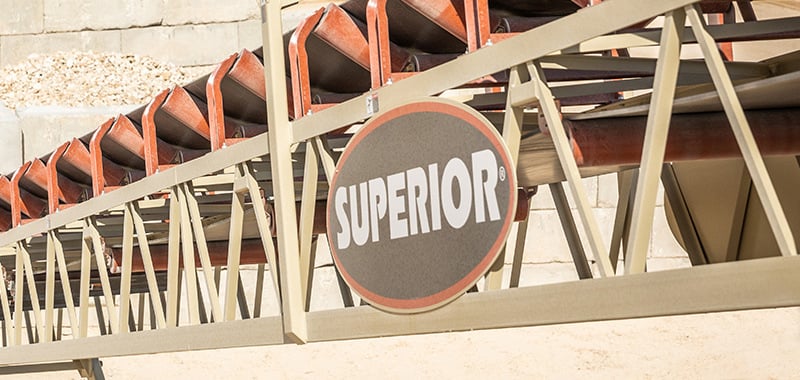
Conveyor Maintenance: Basic Design to Increase Your Uptime
Designing a conveyor to be maintenance friendly means providing adequate provisions for necessary service from the onset.
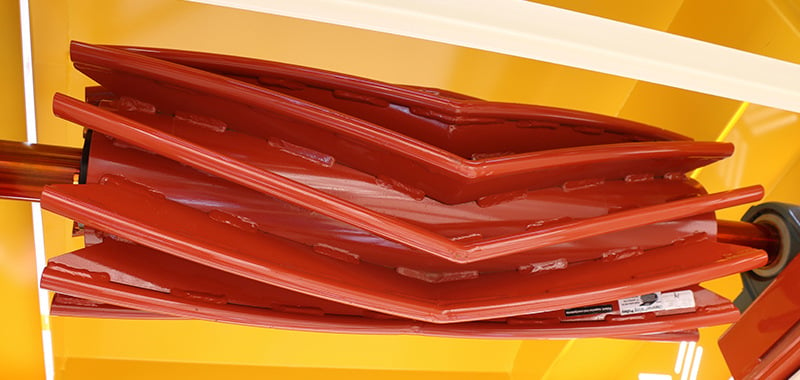
Modern Wing Pulleys: Extend Belt Life With V-Shaped Model
It is common for operations to stick with traditional conveyor components even though they are causing maintenance challenges.
Talk to an Expert
Need more information? We'll get you in contact with a product expert in your area.