Case Study
Knife River Corporation
- St. Helens, Oregon
- LOCATION
- River Terminal: Barge Loading
- INDUSTRY
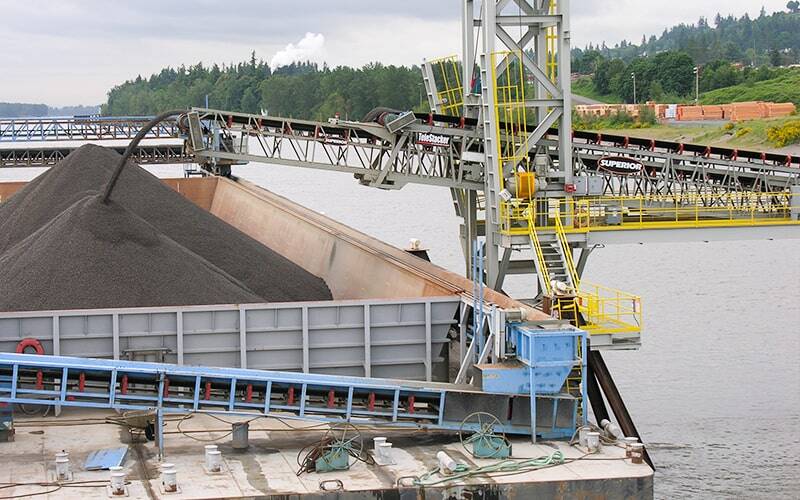
The Challenge
Knife River Corporation faced a challenge of effectively transporting large quantities of aggregate materials from their new processing site to the Portland metro area, located 30 miles upriver. The traditional methods of truck and rail transport were cost-prohibitive, given the significant volumes involved.
The company needed a solution to minimize transportation costs, reduce fuel consumption, and ease road congestion, while also handling the complex task of transferring material across a highway to a barge-loading facility.
“The operators on the barge have the ability to raise and lower the telescoping conveyor while keeping the load centered on the barge. If the barge starts to list left or right, they can make adjustments.”
The Solution
To address these challenges, Knife River Corporation, in consultation with Superior Industries, implemented a state-of-the-art conveyor system designed for barge loading. The key component of this system was a custom-built 48-inch by 150-foot TeleStacker Conveyor, engineered to operate on a dock structure extending 360 feet into the Columbia River.
This conveyor was designed to handle the variable height of the river and the barge, which could drop up to 13 feet as it loaded. The system also featured programmable logic controllers (PLCs) and wireless remote control, allowing operators to adjust the conveyor’s positioning to ensure even loading across the barge.
To support this system, four field conveyors, totaling nearly a mile in length, were installed to transport material from the mining site to the processing facility, through a tunnel beneath the highway, and finally to the barge-loading area.
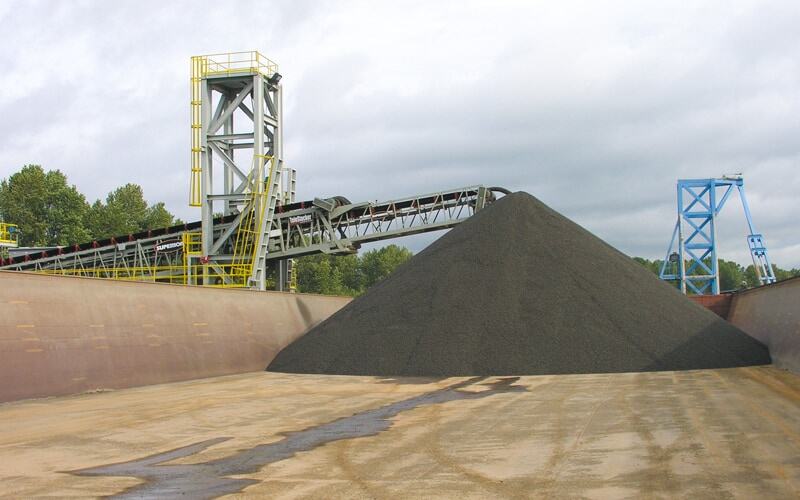
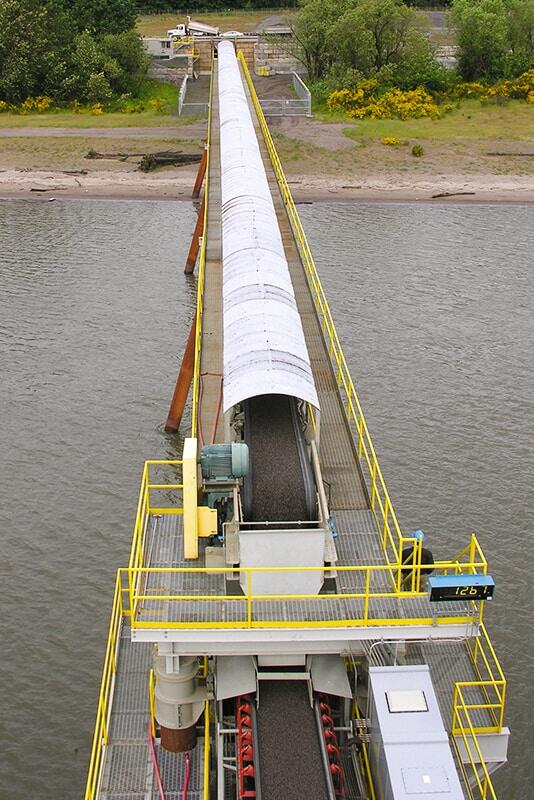
The Results
The implementation of the TeleStacker Conveyor and supporting field conveyors resulted in significant operational efficiencies for Knife River Corporation.
- The company achieved a cost savings of over $3 per ton by shifting from truck transport to barge transport, saving more than $1 million in transportation costs in the first seven months alone.
- The ability to load up to 8,000 tons of material onto a barge in just four hours allowed Knife River to meet high demand during peak seasons, with the capacity to load as many as three barges per day.
- This shift to river transport also eliminated over 11,000 truckloads annually from traversing local roads, contributing to safer highways and lower emissions.
The innovative conveyor system ensured that Knife River could efficiently and cost-effectively move materials to market, reinforcing their position as one of Oregon’s leading suppliers of aggregates
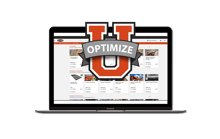
OptimizeU - Strategic Learning
Pursue greater production with comprehensive online courses in crushing, screening, conveying, and washing. Check out the premiere training resource in the construction aggregates industry.
Related Content
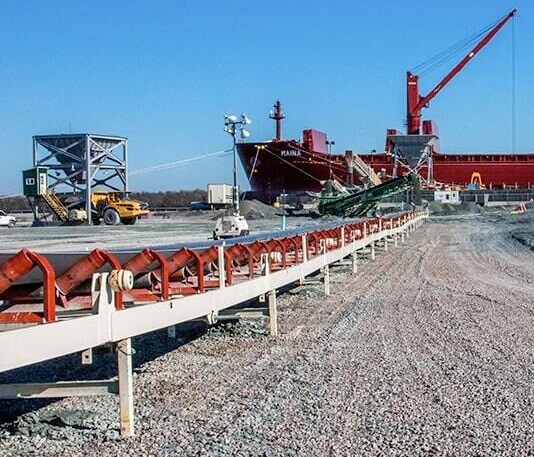
Carver Companies Saves $1 Per Ton on 2 Million Tons Annually with Superior’s Conveyor System
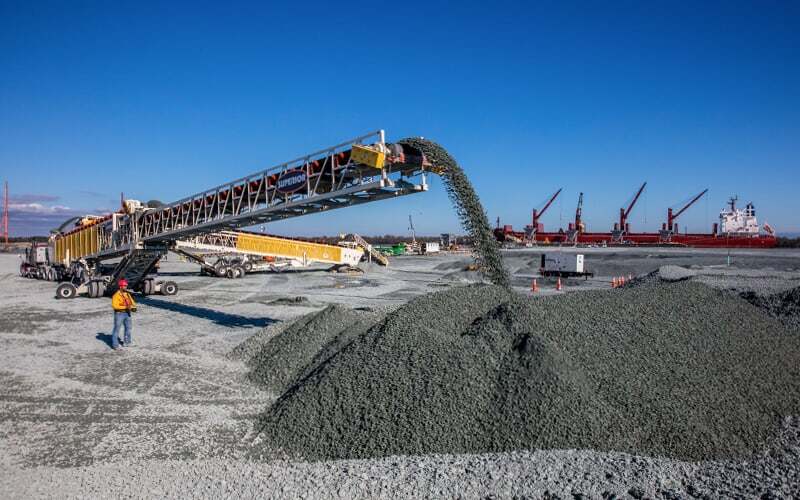
Carver Companies Tackles Massive Container Port Buildout with Mobile Conveyors
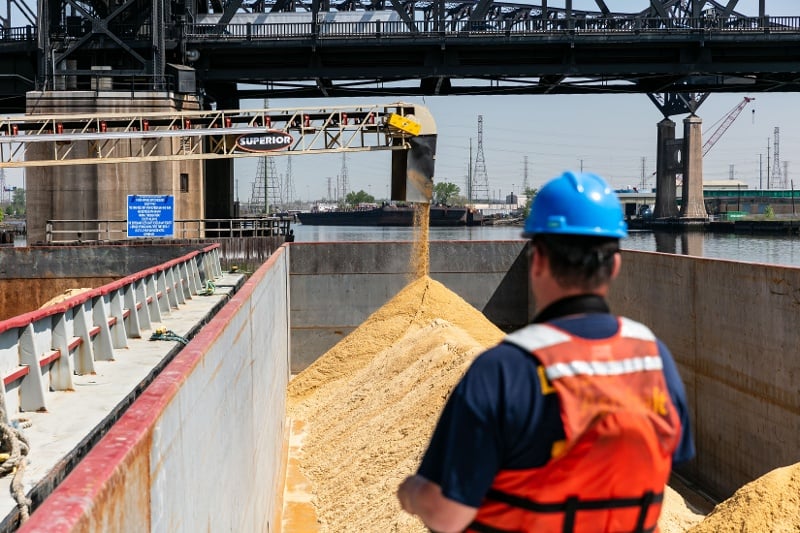