CASE STUDY
Gotham Aggregates
- Newark, New Jersey
- LOCATION
- River Terminal: Barge Loading
- INDUSTRY
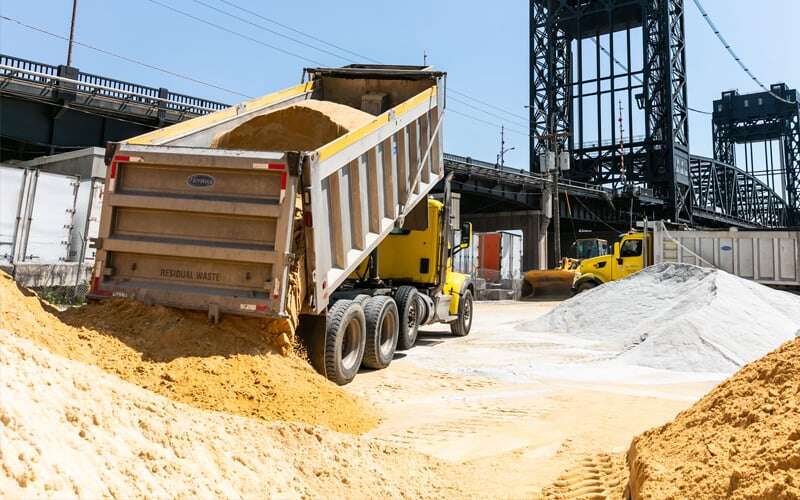
The Challenge
Gotham Aggregates faced the logistical challenge of delivering construction aggregate into the dense and congested New York City metro area cost-effectively.
Traditional truck transport methods were becoming increasingly inefficient due to limited truck availability, rising labor costs, high bridge tolls, and severe traffic congestion, which reduced the number of daily trips and increased overall shipping expenses.
The company needed to find a more efficient and economical way to move large volumes of aggregate to meet the demands of the tri-state market while operating within a small riverfront footprint.
“Trucking to our barge loading operation versus trucking directly to New York City markets from New Jersey quarries reduces travel time by more than 50% and requires less trucks to move the same volumes.”
The Solution
To overcome these challenges, Gotham Aggregates established a barge loading facility along the Passaic River, strategically located near Newark Bay. At the heart of this operation is a 36-inch by 150-foot TeleStacker® Conveyor, a telescoping radial stacking conveyor designed to maximize load volumes.
The facility’s truck unloader feeds the TeleStacker Conveyor, which operates on a spud barge capable of loading two barges without needing to reposition them or the conveyor. The conveyor system is also adjustable to accommodate fluctuations in river height and barge displacement.
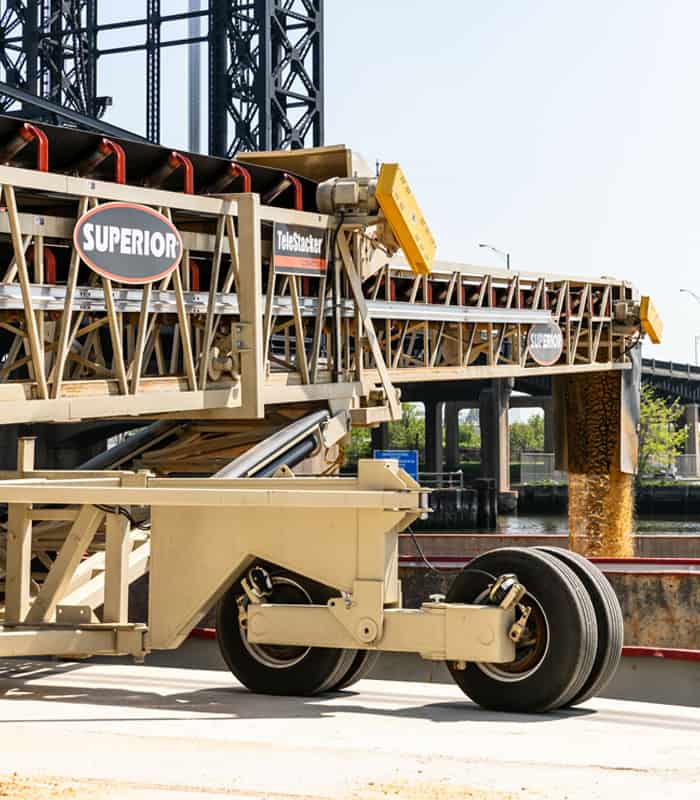
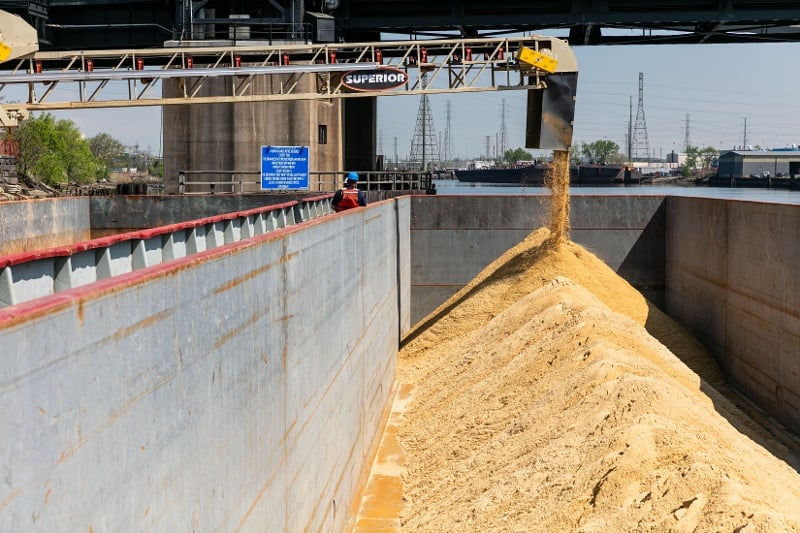
The Results
The implementation of the TeleStacker Conveyor system transformed Gotham Aggregates' barge loading operations, enabling them to ship aggregates to New York City markets more efficiently and cost-effectively. By utilizing barge transport, Gotham Aggregates achieved up to a 35% reduction in shipping costs compared to traditional truck transport.
The facility can load up to four barges a day, each reducing the number of trucks on the road by 80 per shipment. The barge loading process is completed in less than 36 hours, including the round trip, significantly improving turnaround times.
Future plans for the facility include expanding its physical footprint and further automating material handling systems to enhance efficiency and reduce material re-handling.
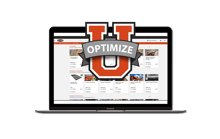
OptimizeU - Strategic Learning
Pursue greater production with comprehensive online courses in crushing, screening, conveying, and washing. Check out the premiere training resource in the construction aggregates industry.
Related Content
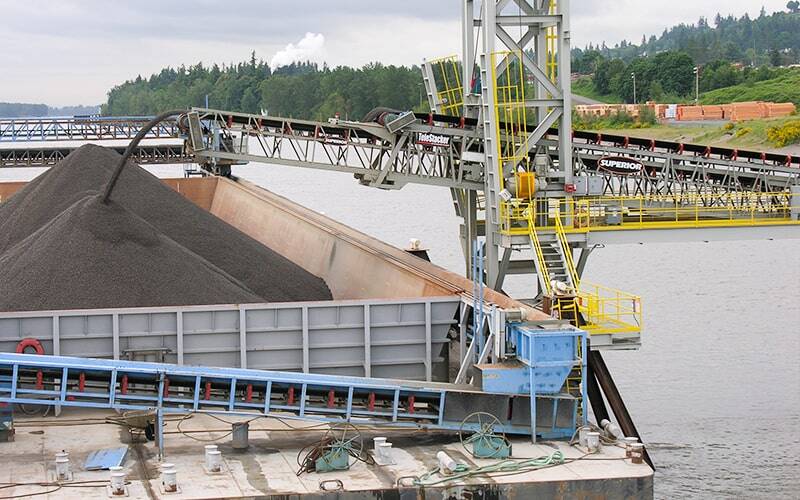
Knife River Shifts to Barge Transport, Saving an Estimated $1 Million in Seven Months
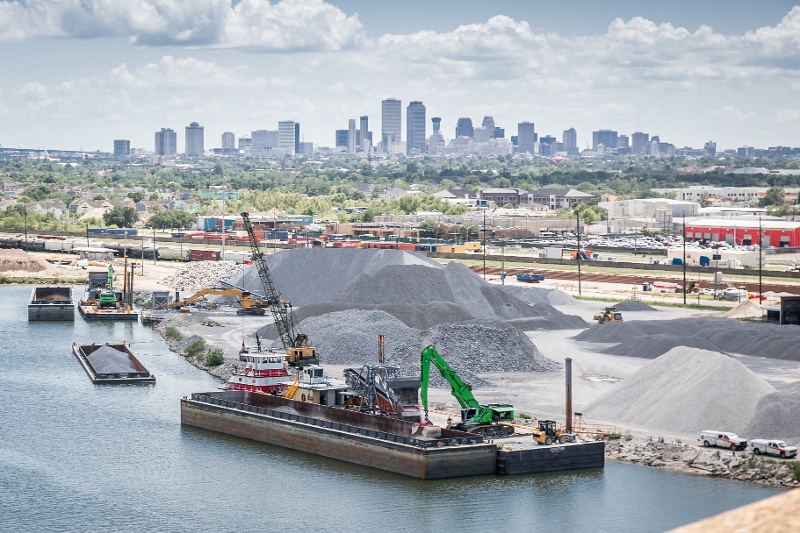
Flexibility on the Mississippi: Pontchartrain Materials' Super Custom, Barge-Mounted Conveyor
_097.jpg?width=2000&name=Weeks%20Marine%20-%20Jersey%20City%2cNJ%20(July%202014)_097.jpg)