CASE STUDY
Hubbard Construction
- Winter Park, Florida
- LOCATION
- Ocean Terminal: Ship Unloading
- INDUSTRY
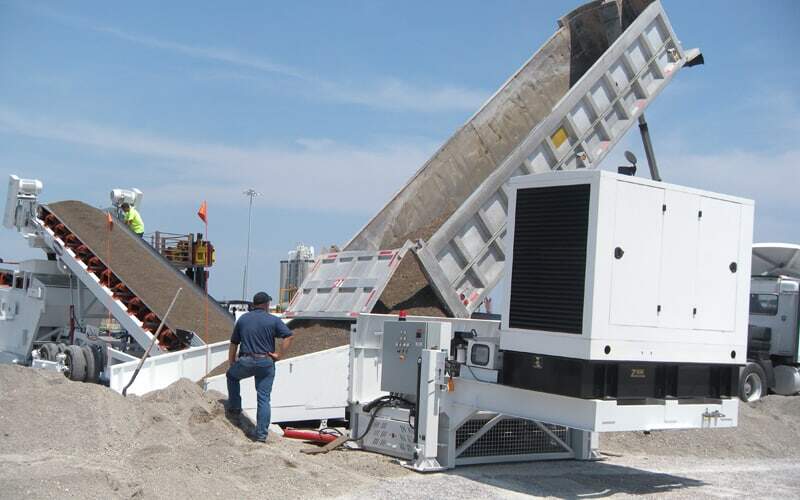
The Challenge
Hubbard Construction, a leading heavy civil construction company in Winter Park, Florida, is curbing trucking and fuel costs by using automated truck unloading and conveying systems. Traditional methods of material handling relying on trucks and loaders were not only expensive but also time-consuming, leading to inefficiencies and increased fuel consumption.
With the need to transport materials from ocean vessels to their stockpiling area, Hubbard sought a solution that would streamline operations, reduce costs, and improve safety by minimizing traffic congestion and the risk of accidents during material handling.
“The truck unloading systems and telescoping radial stacking conveyors have eliminated the two loaders we used previously, which has certainly delivered substantial savings in labor, fuel and maintenance.”
The Solution
To address these challenges, Hubbard Construction implemented a combination of RazerTail® Truck Unloaders and TeleStacker® Conveyors. These systems allowed for efficient and automated unloading of materials from trucks directly onto conveyors, eliminating the need for multiple loaders and reducing material handling steps.
The RazerTail Truck Unloaders transferred up to 25 tons of material in minutes, significantly improving cycle times, while the TeleStacker Conveyors provide increased stacking capacity over standard radial stackers.
Up to 30% more material can be stockpiled under Superior's telescoping stacker. This is particularly important to Hubbard as they wish to maximize stockpile volume on their limited three-acre material storage footprint. Also, the operation can program the telescoping radial stacking conveyor to create stockpiles in many different shapes, sizes, and configurations.

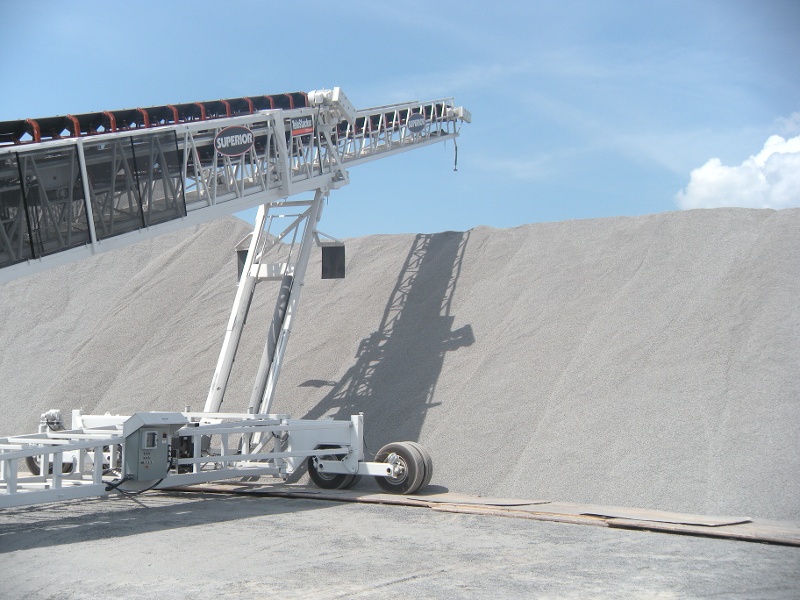
The Results
The implementation of the RazerTail Truck Unloaders and TeleStacker Conveyors resulted in significant cost savings and operational improvements for Hubbard Construction.
Ccycle times were reduced to just 45 seconds per truck, compared to the slower process of using loaders. This led to reduced labor, fuel, and maintenance costs, as the need for two loaders was eliminated.
Additionally, the automated telescoping radial stackers provided better control over product quality by preventing material segregation and allowing for precise stockpiling. The new system also improved safety by reducing traffic congestion and the risk of accidents on-site.
Overall, the investment in advanced material handling systems allowed Hubbard Construction to increase production capacity and lower operating costs while maintaining high standards of product quality and safety.
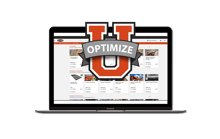
OptimizeU - Strategic Learning
Pursue greater production with comprehensive online courses in crushing, screening, conveying, and washing. Check out the premiere training resource in the construction aggregates industry.
More Projects & Resources
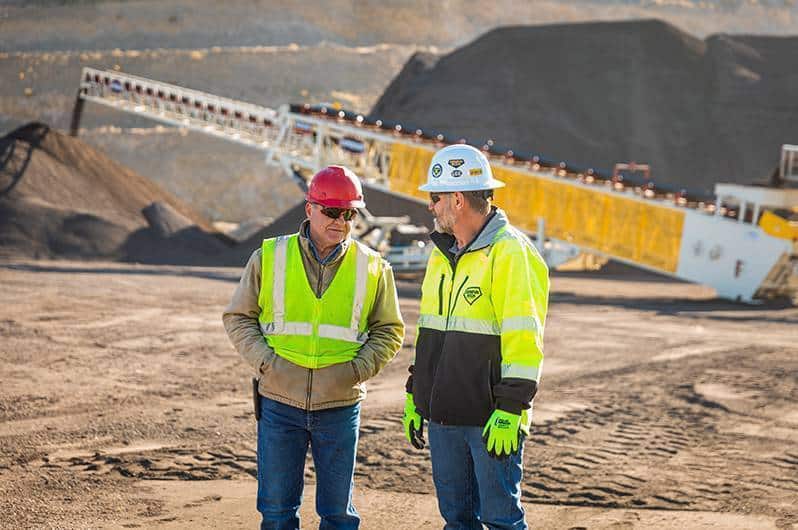
Peak Performance Achieved: Geneva Rock’s Sustainable Material Handling
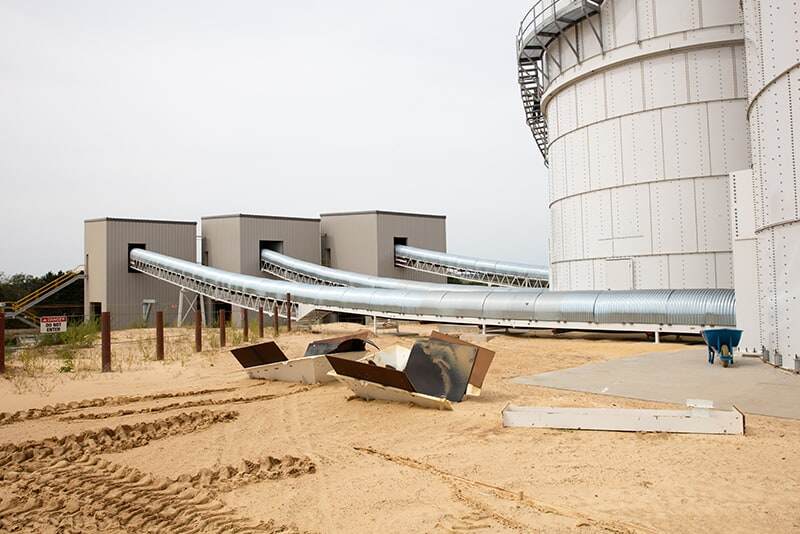
Efficiency in Motion: Hi-Crush Relocates TeleStacker® Conveyor Three Times a Week with Ease
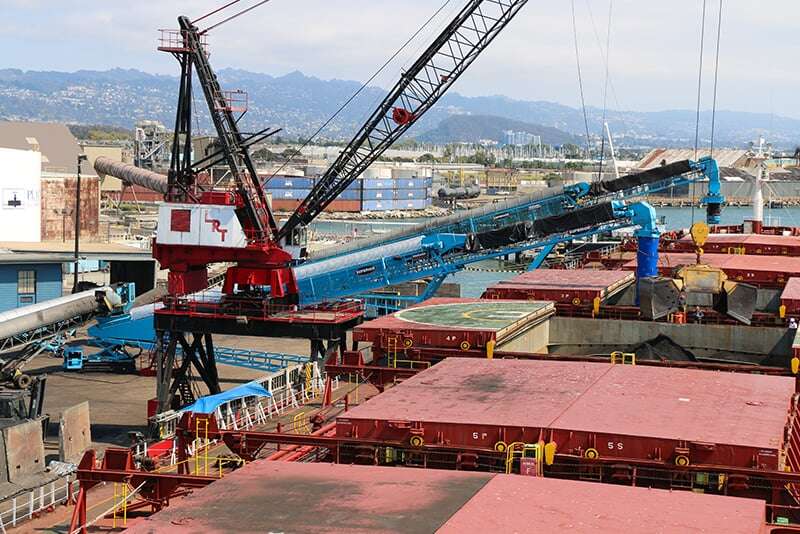