CASE STUDY
Geneva Rock Products
- Salt Lake City, Utah
- LOCATION
- Aggregates: Sand & Gravel
- INDUSTRY
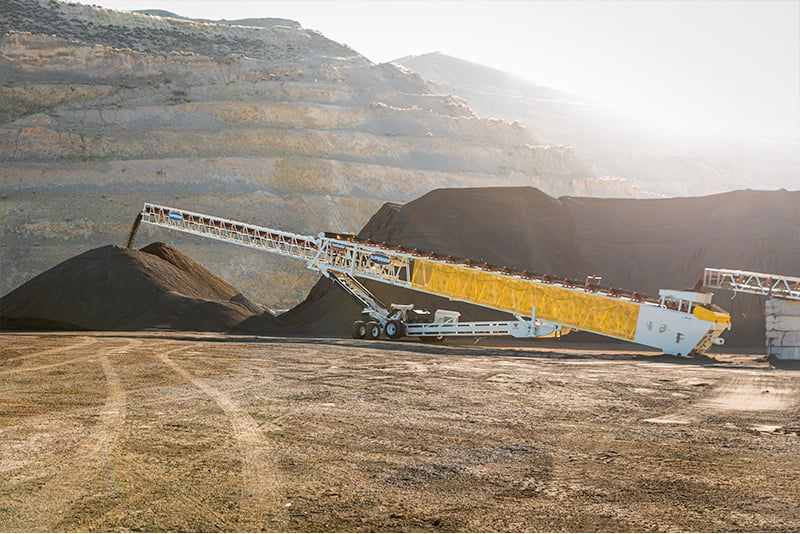
The Challenge
Geneva Rock Products, known for its commitment to sustainability, energy efficiency, and safety at its Point-of-the-Mountain site near Salt Lake City, Utah, faced the challenge of meeting stringent new specifications for recycled asphalt in Utah.
The company needed to avoid segregation in both material and oil content during the recycling process to ensure compliance with the updated regulations. Previous methods using standard radial stackers and dozers for blending were proving inefficient, leading to inconsistencies in the recycled asphalt’s quality and costly rehandling.
"Due to the way the TeleStacker Conveyor is programmed, we get a much better blend of material, and the product is the same on one end of the pile as it is on the other."
The Solution
To address these challenges, Geneva Rock Products collaborated with Superior Industries to upgrade their material handling system, particularly in their asphalt recycling operations. Superior recommended the installation of a 36-inch by 150-foot TeleStacker® Conveyor, a telescoping radial stacking conveyor designed to eliminate material segregation by stockpiling in windrows.
This advanced system ensured a uniform blend of recycled asphalt, meeting the strict new specifications. Additionally, the conveyor was equipped with innovative features like FD Auto Level technology, which maintains a level head pulley during radial travel, and the SonicScout™ Material Sensor, which prevents gaps in the stockpile by stopping conveyor travel if feed material flow is interrupted.
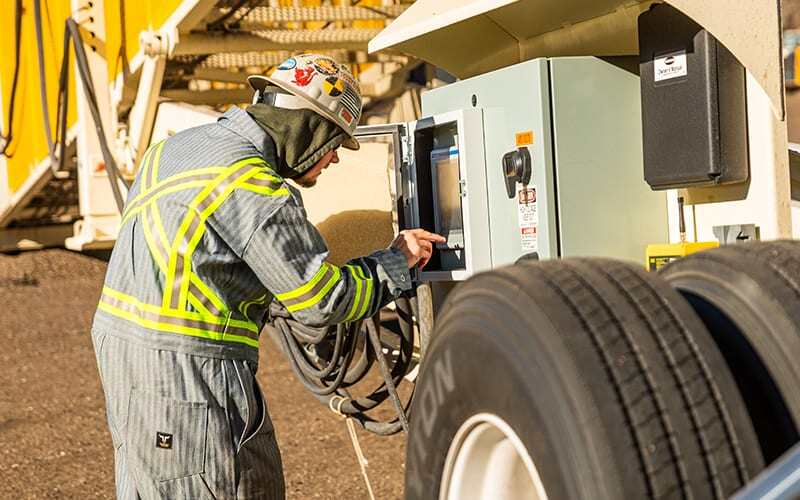
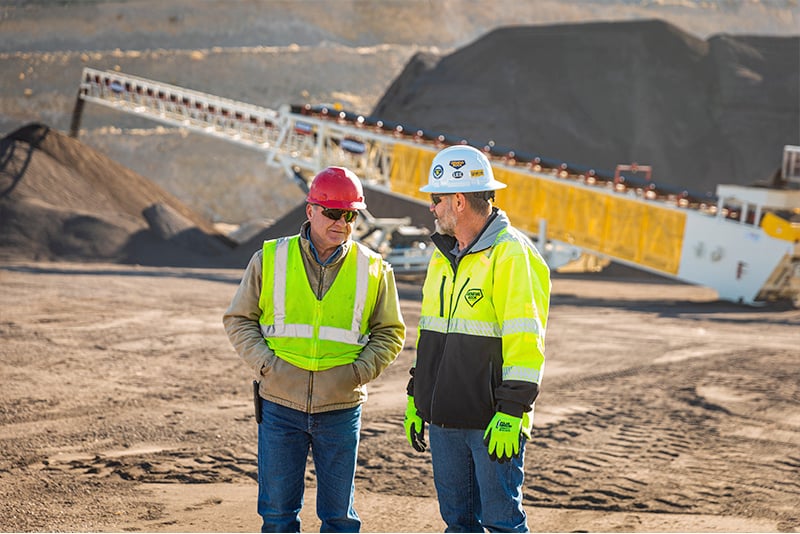
The Results
The new system has eliminated the issues of material segregation and inconsistencies in oil content, resulting in more uniform gradations and compliance with stringent specifications.
The improvements have allowed Geneva Rock to build a 30,000-ton stockpile during the winter, providing a steady supply of recycled asphalt to feed the plant throughout the summer.
Additionally, the high-quality components from the vertically-integrated Superior Industries, including custom idlers and Chevron® Pulleys, have contributed to increased wear life, belt protection, and overall cost-per-ton savings.
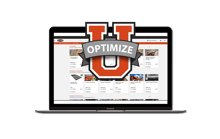
OptimizeU - Strategic Learning
Pursue greater production with comprehensive online courses in crushing, screening, conveying, and washing. Check out the premiere training resource in the construction aggregates industry.
More Projects & Resources
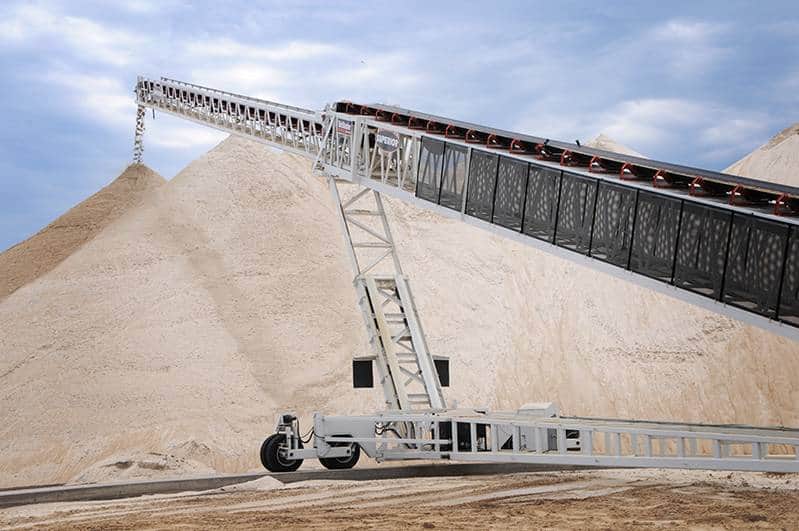
Reducing Costs and Footprint: Littleton Quarry’s Strategic Conveyor Upgrade
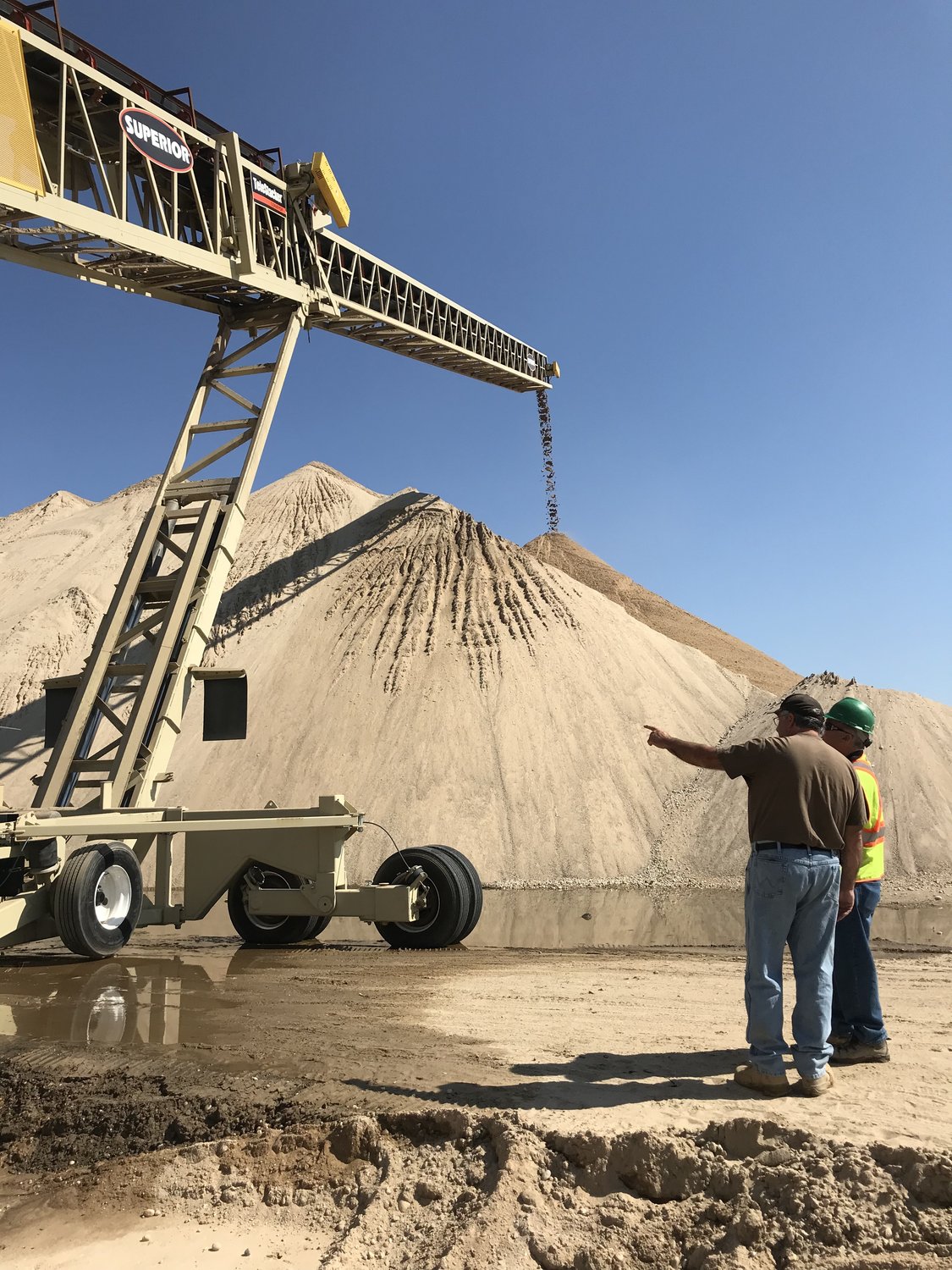
Higher Stockpiles, Fewer Trucks: Coram Materials Streamlines Operations
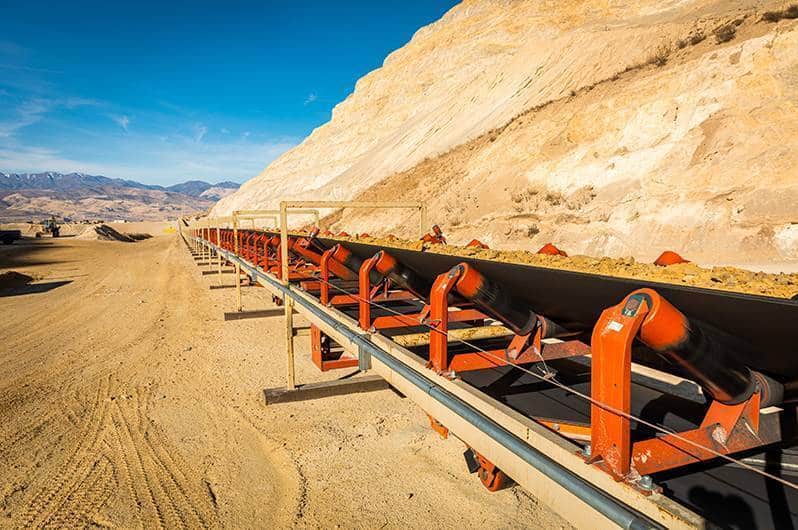