CASE STUDY
Geneva Rock Products
- Draper, Utah
- LOCATION
- Aggregates: Sand & Gravel
- INDUSTRY
- 3,500 TPH
- TONNAGE
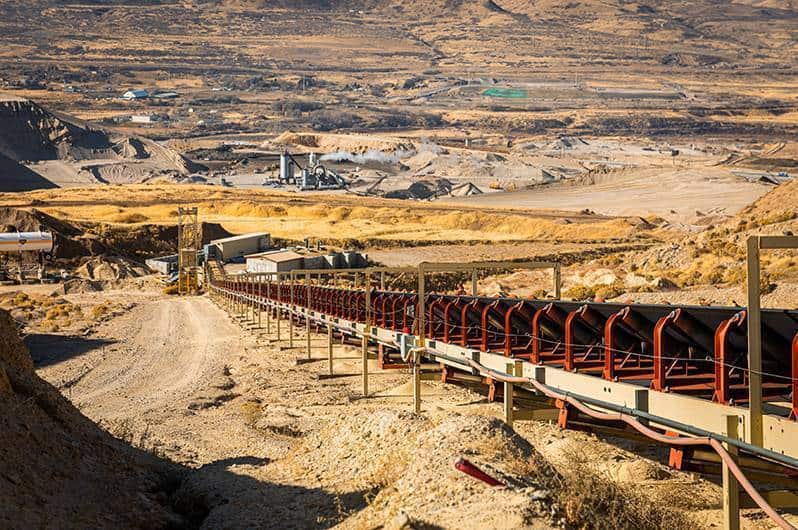
The Challenge
Geneva Rock Products faced the significant challenge of efficiently transporting large quantities of upper-ledge rock material from the top of a mountain to ground-level crushing and processing operations at their Point-of-the-Mountain site.
The traditional method of using dozers and haul trucks not only posed safety risks but also incurred high operational costs and environmental concerns, including increased emissions and dust pollution. As the material source continued to move higher up the mountain, Geneva Rock needed a sustainable, cost-effective, and safe solution to maintain their high production capacity.
"The conveyor system takes the excess power generated from the belt and feeds it to a central distribution center to be used for plant operations. That is sustainability at its best!"
The Solution
To address these challenges, Geneva Rock installed a state-of-the-art downhill overland conveyor system engineered and manufactured by Superior. This innovative system, designed to transport material efficiently while generating electricity, allowed Geneva Rock to move material from the mountain to the processing plant with minimal handling.
The conveyor system features three downhill conveyors, ranging from 700 to 1,050 feet in length, transporting material at a rate of 3,500 tons per hour. The system also includes a 150-foot radial stacker for creating surge piles, ensuring continuous operation even during maintenance or unexpected shutdowns.
Additionally, the system’s variable frequency drive acts as a braking system, safely controlling the descent of material and converting excess energy into electricity to power the site.
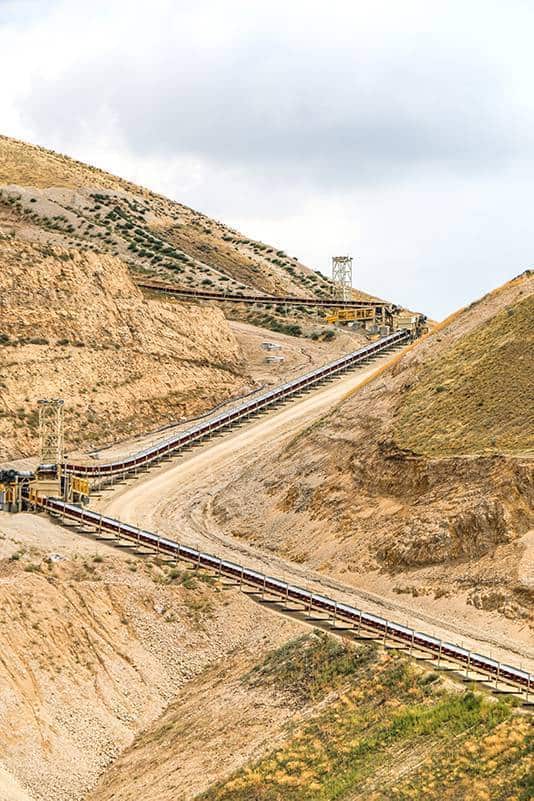
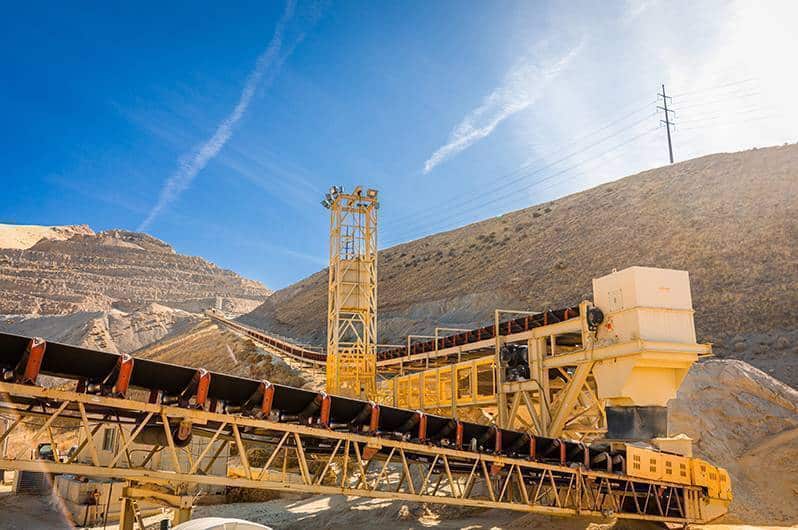
The Results
The installation of the downhill overland conveyor system resulted in significant benefits for Geneva Rock. The system not only enhanced safety by reducing the need for mobile haulage equipment and minimizing material handling at the top of the mountain but also lowered costs by reducing labor, fuel consumption, and equipment wear-and-tear.
The ability to generate electricity from the conveyor system further contributed to sustainability, providing enough power to support much of the 50-acre site. The reduction in particulate matter and noise pollution also aligned with Geneva Rock’s commitment to sound environmental practices. Overall, the conveyor system allowed Geneva Rock to achieve its goals of increased efficiency and safety, while maintaining high production levels.
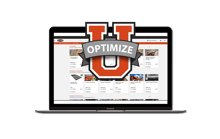
OptimizeU - Strategic Learning
Pursue greater production with comprehensive online courses in crushing, screening, conveying, and washing. Check out the premiere training resource in the construction aggregates industry.
More Projects & Resources
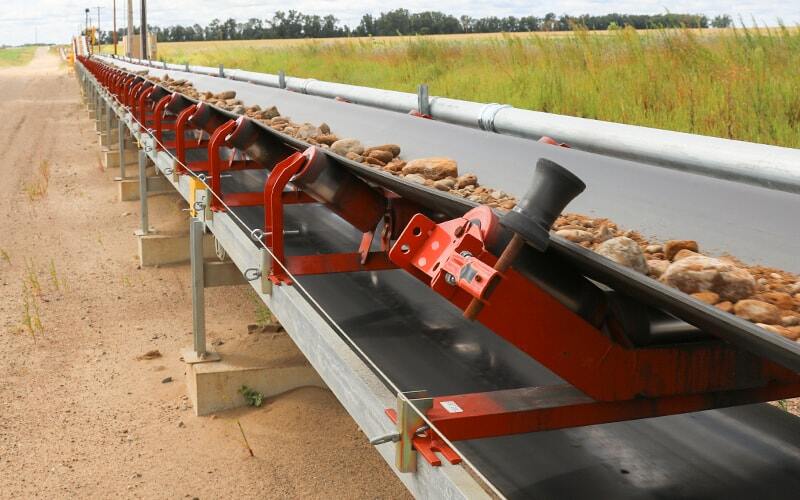
Dakota Aggregates Embraces Modular Conveying for Easy Material Handling Adjustments

Knife River Meets Tight Deadline at Temporary Site Using Portable Overland Conveyor
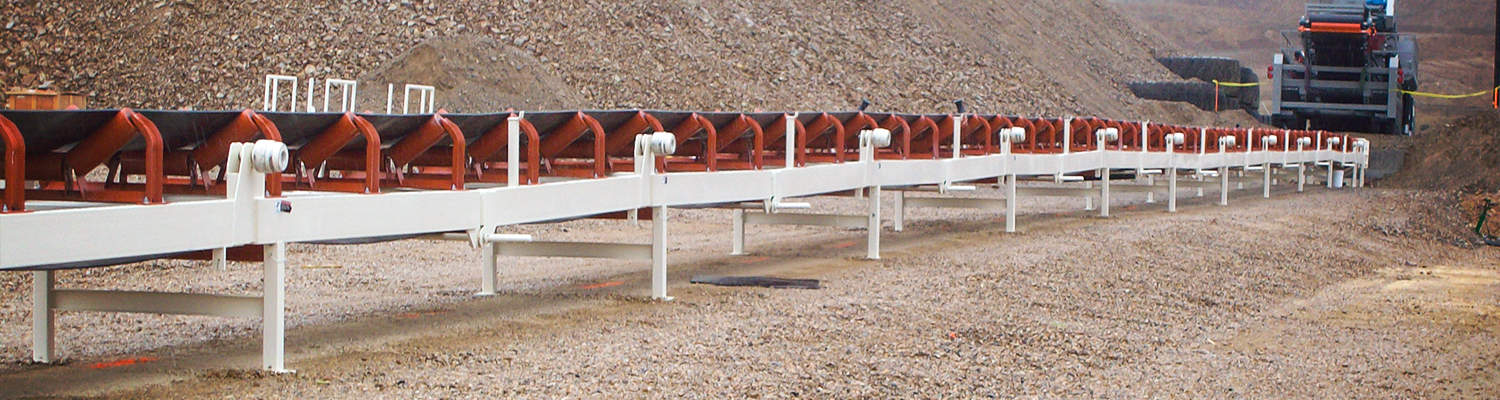