CASE STUDY
Dakota Aggregates
- Rosemount, Minnesota
- LOCATION
- Aggregates: Sand & Gravel
- INDUSTRY
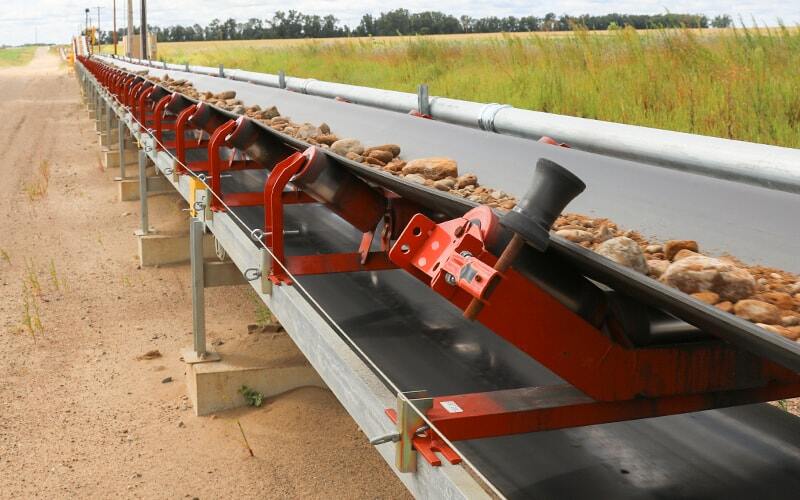
The Challenge
Operating within the University of Minnesota’s UMore Park, Dakota Aggregates needed an efficient and flexible material handling solution for its new processing plant. The expansive site, spanning three miles from north to south and a mile and a half from east to west, required a cost-effective overland conveyor system that could be easily reconfigured to accommodate changing mining needs each season.
Traditional custom-engineered overland systems were expensive and lacked the flexibility needed to adapt to the operation’s dynamic requirements, making it challenging to maintain efficiency and keep costs low.
“It was refreshing to share our input on the system with the engineers at Superior and to work with them on various enhancements to this new product.”
The Solution
Dakota Aggregates partnered with Superior Industries to obrain a Zipline® Conveyor, which is a pre-engineered, modular overland conveyor designed for quick and tool-free installation.
The Zipline Conveyor allowed Dakota Aggregates to efficiently transfer material from the mining face to the processing facility while minimizing the use of loaders and haul trucks, thereby reducing emissions, energy consumption, and operating costs.
The system’s modular design provided the necessary flexibility to add or remove sections as needed, enabling easy reconfiguration to meet the operation’s seasonal demands. The installation process was streamlined, with three crew members able to assemble 1,000 feet of conveyor in just a ten-hour day using only basic equipment like a forklift and skid steer loader.
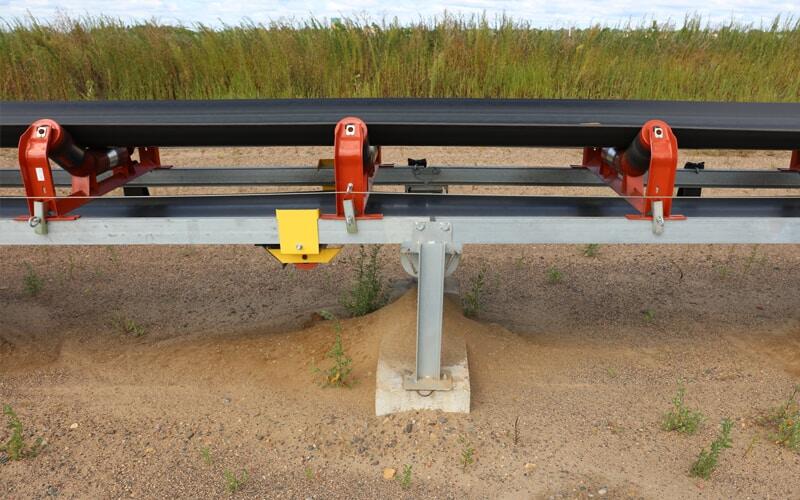
025-1.jpg)
The Results
The adoption of the Zipline Conveyor system resulted in significant operational improvements for Dakota Aggregates.
- The flexible and modular design allowed the company to quickly and cost-effectively reconfigure its overland conveyors to accommodate changing mining requirements.
- The system’s ease of installation and modular portability reduced the need for heavy equipment and labor, cutting down installation time and costs.
- Additionally, by reducing reliance on loaders and haul trucks, Dakota Aggregates minimized fuel consumption, emissions, and maintenance expenses, leading to lower operating costs per ton, which is important to the landowner.
The success of this innovative material handling solution not only supported Dakota Aggregates’ commitment to sustainability but also provided long-term operational benefits as the company continues to serve the Twin Cities metro area with high-quality aggregate products.
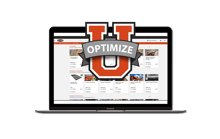
OptimizeU - Strategic Learning
Pursue greater production with comprehensive online courses in crushing, screening, conveying, and washing. Check out the premiere training resource in the construction aggregates industry.
More Projects & Resources
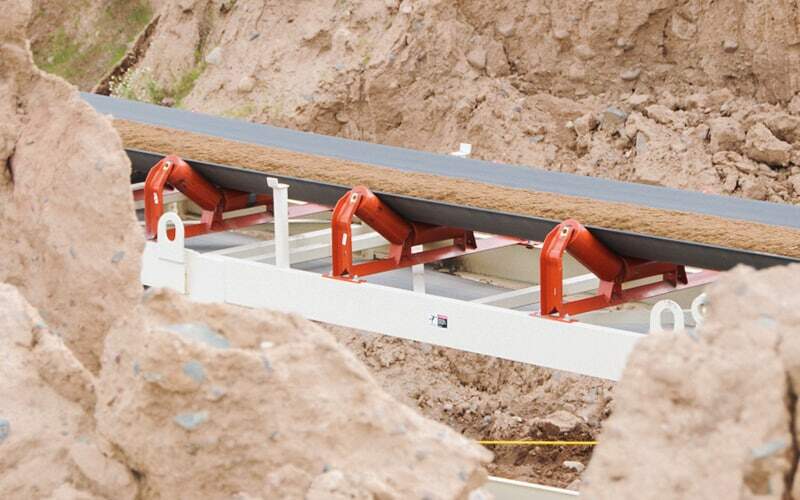
Knife River Meets Tight Deadline at Temporary Site Using Portable Overland Conveyor
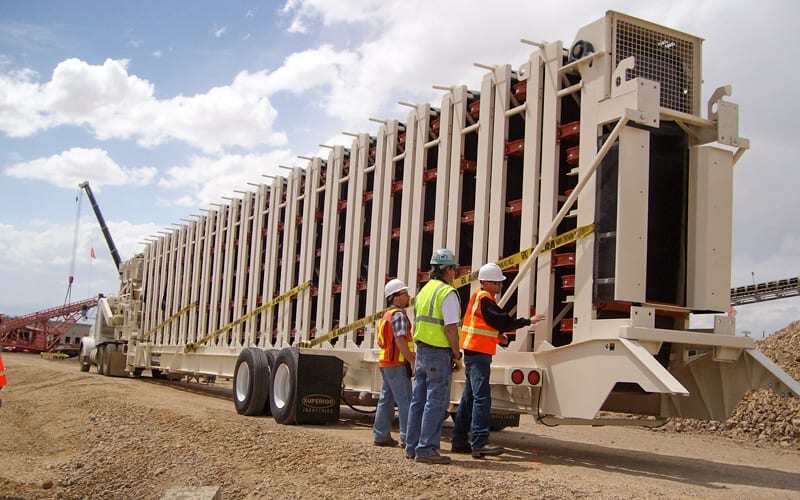
Rapid Deployment: Newmont Utilizes Trailblazer® Conveyor to Meet Tight Deadlines at SAG Mill
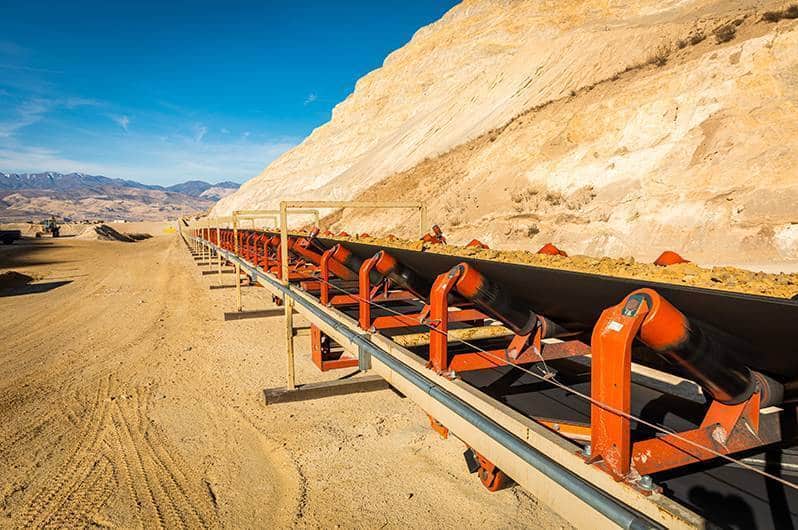