Case Study
Aggregate Industries: Littleton Quarry
- Boston, Massachusetts
- LOCATION
- Aggregates: Crushed Stone
- INDUSTRY

The Challenge
The Littleton Quarry, a key site within Aggregate Industries’ Northeast Region, sought to enhance its operational efficiency while reducing costs per ton. Initially developed as a sand and gravel pit and later transitioning to a granite quarry, the site had been in operation since the 1950s. However, by the 2010s, the quarry faced challenges with its outdated material handling systems. The existing setup required double handling of finished products, leading to increased costs in fuel, wear and tear on equipment, and additional labor. Moreover, the operation was constrained by an inefficient footprint, which further drove up operational costs.
“We can program the TeleStacker Conveyor to a certain travel pattern and then just walk away and let it do its thing."
The Solution
To address these challenges, the Littleton Quarry undertook a significant upgrade by relocating its secondary and tertiary plants closer to the quarry face. This upgrade included the integration of two 36” by 150’ TeleStacker® Conveyors and three portable radial stackers, all manufactured by Superior Industries.
These advanced material handling systems allowed the quarry to streamline its operations by eliminating the need for double handling and reducing the overall footprint by 43%. The new setup also eliminated over 2,200 feet of overland conveyors, further boosting efficiency. The TeleStacker® Conveyors, equipped with the PilePro™ Automation package, provided the ability to create customized, desegregated stockpiles, and enhanced product quality and consistency.

03-1.jpg?width=800&height=533&name=PRSC%20-%20Lyman%20Richey%20-%20Omaha%2c%20NE%20(2019-08)03-1.jpg)
The Results
The introduction of the new conveyor systems at Littleton Quarry resulted in a 28-cent-per-ton savings by eliminating the need for double handling and reducing reliance on costly loaders and haul trucks.
The ability to stockpile up to 70,000 tons under each conveyor, combined with the flexibility and precision of the TeleStacker® Conveyors, significantly improved operations and product quality.
Additionally, the quarry’s environmental impact was reduced as the new conveyor systems lowered emissions and minimized pollution compared to traditional material handling methods of haul trucks and loaders. “Our upgrades, and particularly our new material handling systems, have significantly affected our quality and our commitment to ongoing improvements in the way we do business,” Abramson says.
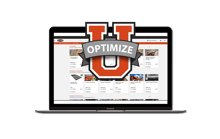
OptimizeU - Strategic Learning
Pursue greater production with comprehensive online courses in crushing, screening, conveying, and washing. Check out the premiere training resource in the construction aggregates industry.
Related Content

Higher Stockpiles, Fewer Trucks: Coram Materials Streamlines Operations
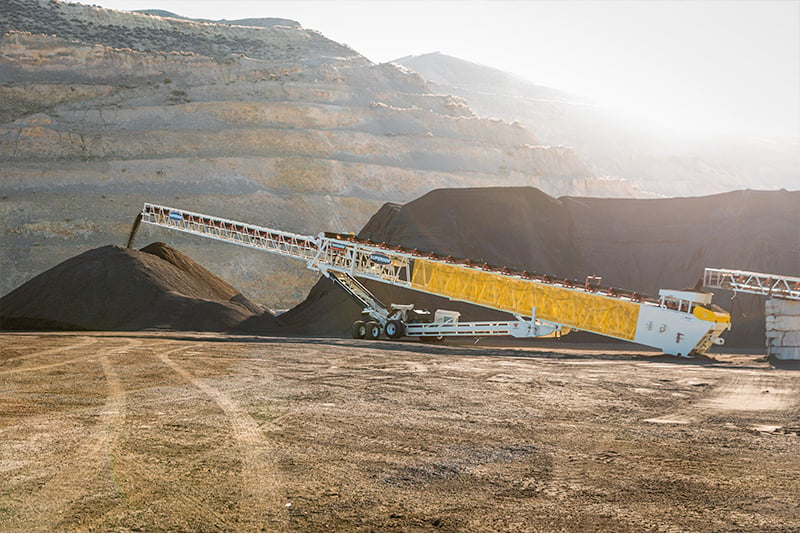
Peak Performance Achieved: Geneva Rock’s Sustainable Material Handling
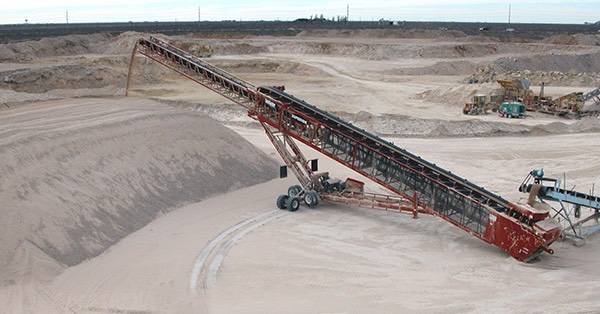