Double Down: Washing Strategies for Tough Deposits
As the era of clean, easily processed deposits fades, the need for double or even triple washing emerges, prompting effective strategies to tackle tough aggregate deposits.
PUBLISHED: APRIL 2025
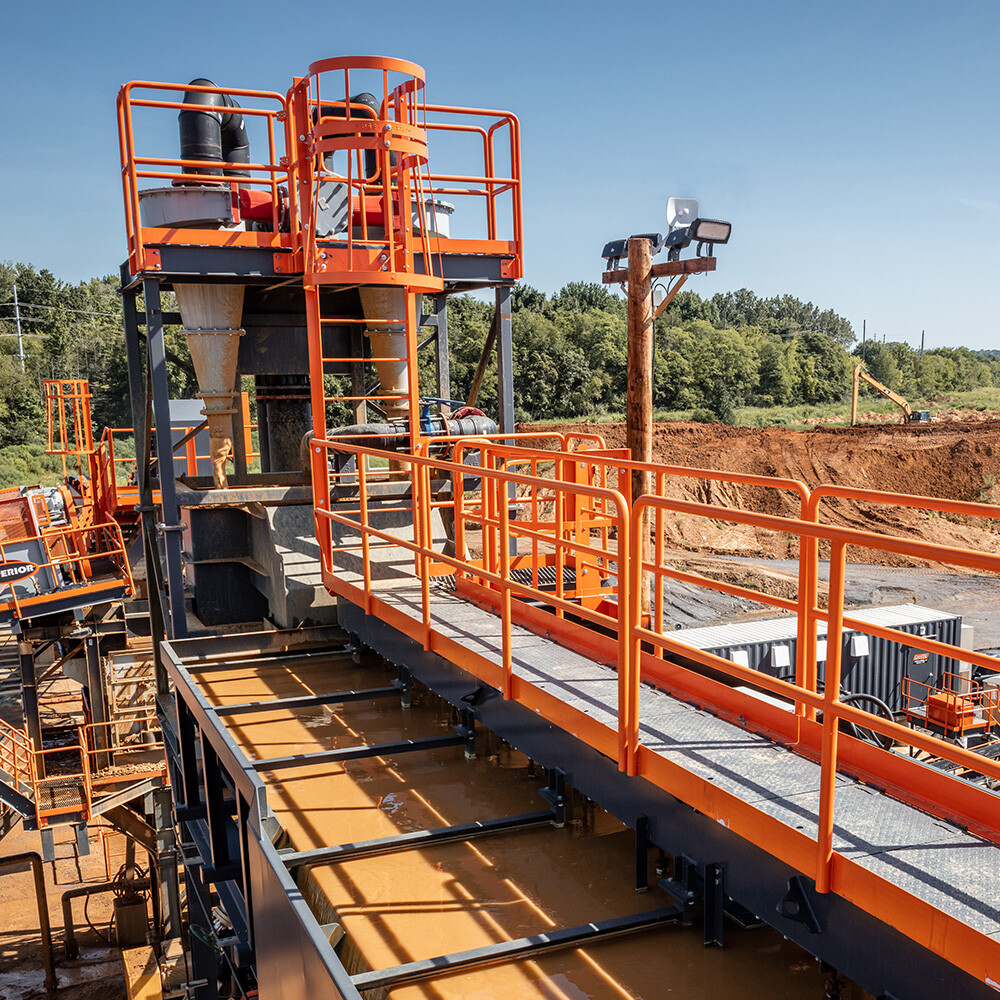
“That’s a frustrating issue for many producers as they tackle today’s tough deposits," says Lauren DeBow, a washing applications engineer at Superior. "There’s still value in that deposit, but it just takes more processing time and equipment to get the good stuff out.”
When digging into the dirtiest deposits, DeBow opts for focus over frustration. The focus is finding the lowest costs per ton while meeting required specifications.
“Washing is a unique process for each and every operation," she says. "Developing cost-efficiency depends upon the particular deposit, specification requirements, and overall plant operations, so we focus on each unique parameter.”
Twice the Challenge
First, there are limits to any single piece of washing equipment — whether it’s a sand screw, a classifying tank, or even a cyclone. In washing, there are no “one-size-fits-all” equipment solutions.
“Sure, some pieces of equipment are more efficient than others, but everything has its place,” she says.
Secondly, when operations have more than 12% minus #200-mesh (fines) in their feed material, that's too many fines to be washed out in one pass.
Given the high demand for DOT #C33 sand products, producers are increasingly aware of the rigorous washing requirements involved. For instance, achieving standard C33 specifications with feed material containing more than 12% minus #200-mesh is not feasible using just a single screw or Helix® Cyclone.
The C33 spec restricts the amount of fines to a mere 0-3% — a strict requirement. Therefore, when feed material consistently contains more than 12%, achieving these specifications demands additional equipment, water, and washing.
Complete Toolbox & Customization
Frustrations with dirty deposits are understandable, but guiding your customers to focus on solutions can change their perspective. DeBow says she finds it fascinating, and even fun, to assist operations with double washing.
“With Superior’s complete equipment toolbox, we can provide producers with custom solutions that fit the site, the deposit, the feed, the final product, and the budget,” she says. "Customization also allows us so many ways to tackle it!"
Solutions vary widely, from simple to more sophisticated.
“When dealing with a low to moderate fines percentage, it may be just a matter of adding another sand screw," she says. "Or it’s as easy as adding a dewatering screen with spray bars just to get the bottom end tightened up a bit."
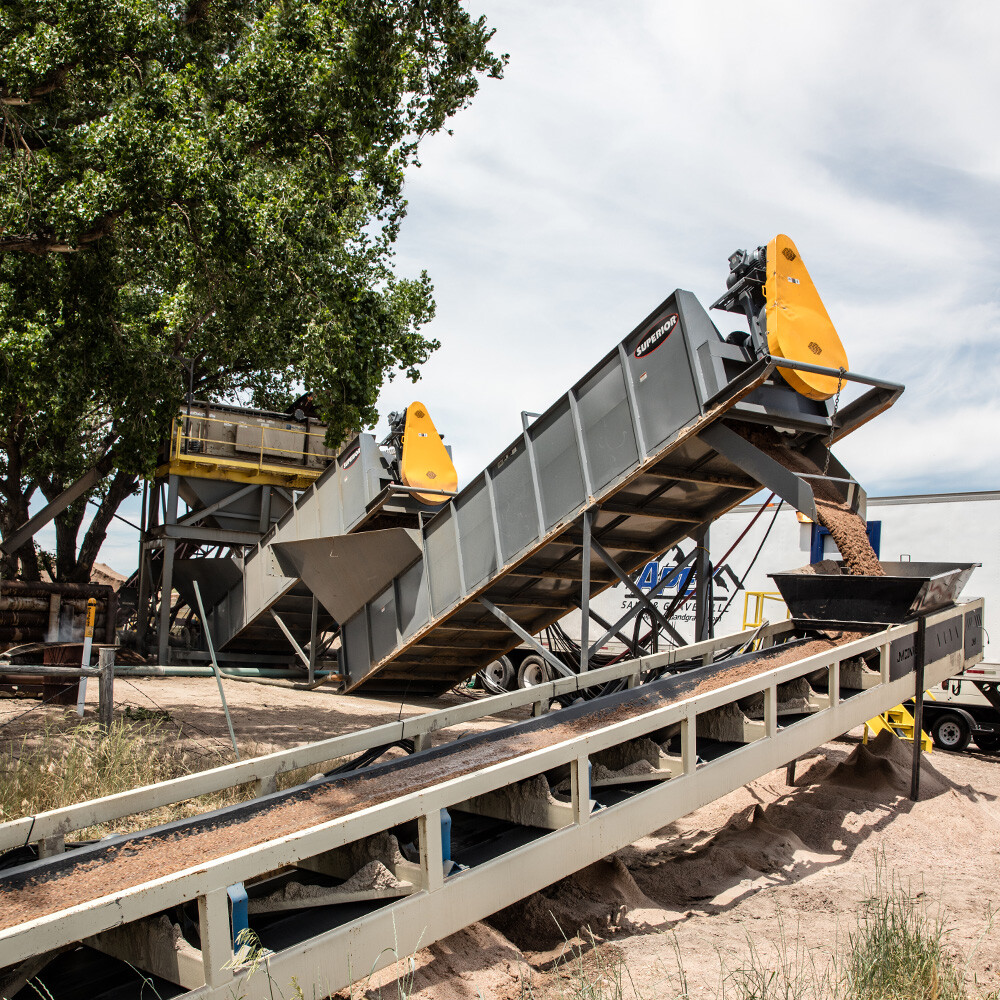
Apex Sand & Gravel uses two fine material washers (screws) to ensure spec-compliant product by removing -200# without sending -50# x #150 fines to waste.
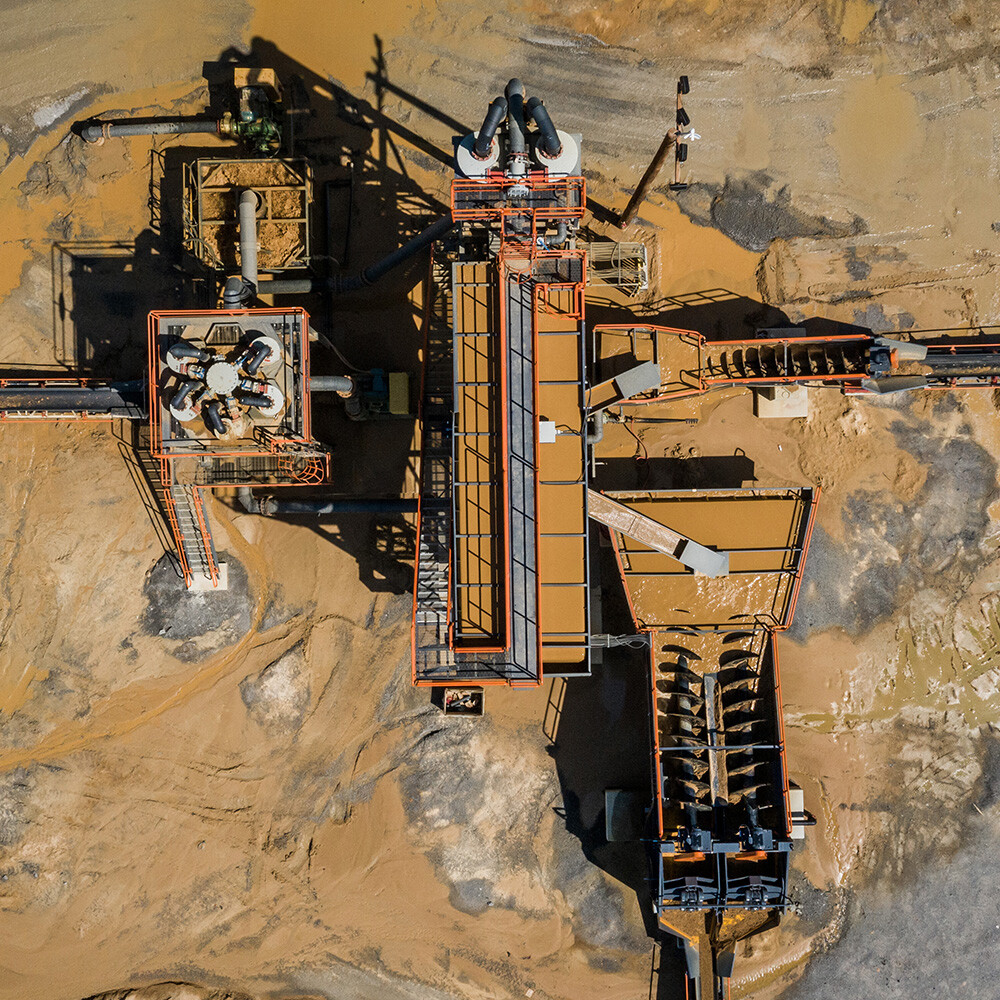
An example of a triple washing application in a wet processing plant. The operation is producing C33 and mortar sand from overburden material generated by a nearby limestone quarry.
When the feed material approaches 20% of material passing #200 mesh, some operations combine cyclones with sand screws for greater control. Also, many solutions involve the use of a classifying tank followed by a sand screw. The classifier filters off a substantial portion of the minus #200 in the first pass, while the remainder is processed again as it hits the screw.
In some cases, it’s best to place a cyclone ahead of a classifying tank. As the cyclone pulls off a portion of the #200s, this takes some of the pressure off the classifying tank, allowing the producer to use a smaller classifier for cost savings or space restrictions.
Again, each wet processing operation is different, and each custom solution depends upon specific parameters and proper analysis. However, no matter how tough the application is, cost-efficient washing remains within reach.
Other Content This Month
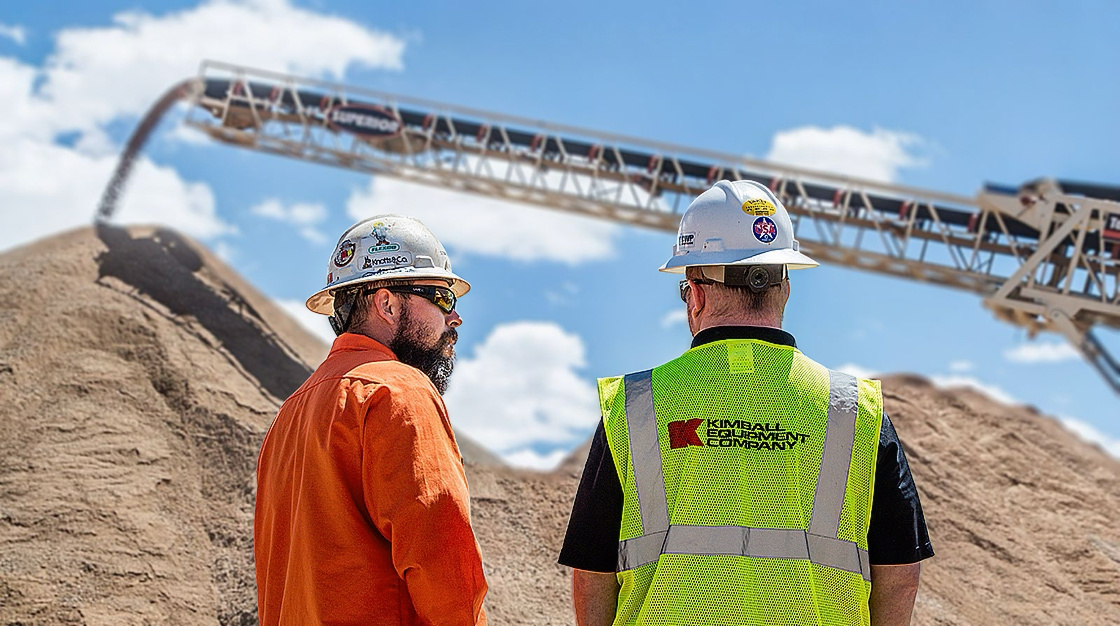
110 Features to Know: Patents Deliver Success
With an extensive portfolio of patents and pending patents, Superior dealers can leverage these unique features in their sales strategies to differentiate themselves from the competition.
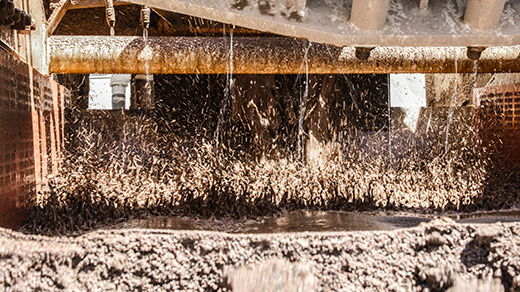
Double Down: Washing Strategy for Tough Deposits
As the era of clean deposits fades, the need for double or even triple washing emerges, prompting effective strategies to tackle tough aggregate deposits.
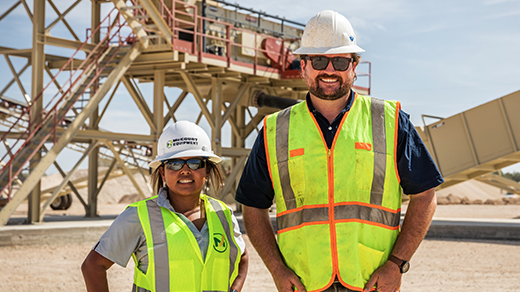
McCourt's Winning Strategy with Platforms
McCourt Equipment and Superior Industries detail a collaborative strategy for modular platform sales and the key factors that drive end users to invest.