Tech Tip: Customized Wet Processing
Why One-Size-Fits-All Often Fails
Achieving optimal washed sand production and fines recovery requires solutions tailored to the specific parameters of each operation. A one-size-fits-all approach can easily fail because wet processing conditions are highly variable across different sites.
To optimize wet processing, it’s essential to choose equipment that matches the specific requirements of the application. Whether you are integrating a new wash plant or improving an existing circuit, finding the correct equipment configuration is key.
Brett Casanova, washing product manager at Superior Industries, emphasizes that a thorough analysis of plant operations, material properties, and capacity needs is necessary to achieve optimal performance. With the right data and access to a broad range of washing components, Superior’s engineers develop customized solutions designed for maximum efficiency and cost-effectiveness.
Key Considerations
- How can efficiency be maximized in wet processing?
- What technologies can reduce or eliminate maintenance?
- Which equipment configurations will best produce clean sand while recovering fines?
The answers to these questions lie in implementing targeted, customized solutions that address specific operational needs. Casanova outlines the benefits of approaching wet processing in this way.
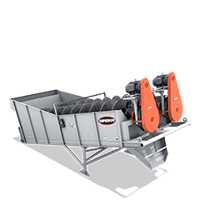
Scrubbing
Attrition Mill
Blade Mill
Coarse Washer
Log Washer
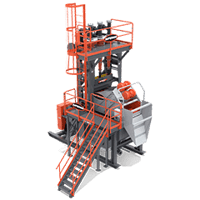
Classifying
Classifying Tank
Density Sizer
Helix® Cyclone
Spirit® Sand Plant
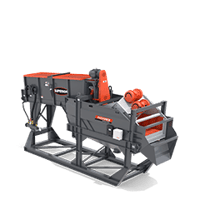
Washing
Aggredry® Washer
Alliance® Washer
Fine Washer
Spirit® Sand Plant
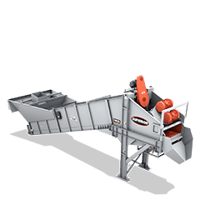
Dewatering
Dewatering Screen
Aggredry® Washer
Alliance® Washer
Fine Washer
Comprehensive Equipment Toolbox
The right solutions require a complete toolbox – not just one or two commonly-used equipment options – or whatever is currently in stock.
Application parameters are numerous including material type, moisture content, specification requirements, footprint, permitting restrictions, finances, water rates and availability, and more. Plus, equipment solutions are required for multiple stages of wet processing from scrubbing, to classifying, washing, and dewatering.
Whether manufacturing sand or washing the dirt out of an already in-spec product, accessing a complete toolbox ensures not only the right package, but also the most cost-efficient one. Consider that certain more affordable solutions can be substituted for a higher capital equipment investment in various applications.
Casanova stresses that since Superior provides the “complete toolbox,” the company is able to “package” plant solutions far more effectively than those manufacturers who must rely upon outsourcing key plant components.
Sand Processing Solutions
Effective washing removes unwanted particles such as lignite, mica, and silts while ensuring products meet specifications. Below is an overview of critical sand washing technologies used in various applications.
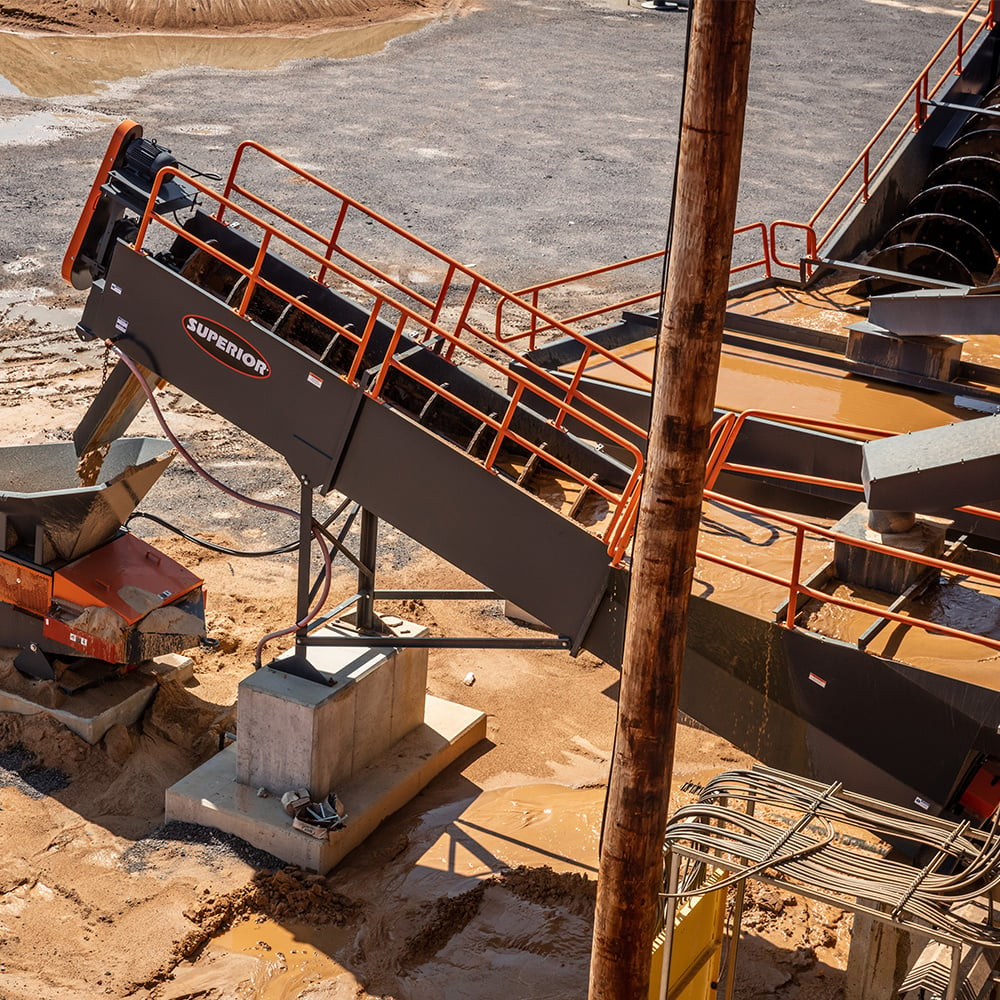
Fine Material Washers
Reliable, easy to maintain, and commonly used, fine material washers remove undesirable silts (with a cut point that ranges from #200 to #100 mesh) from the feed while heavier material augers up an incline for dewatering. Additionally, fine material washers are often placed after classifying tanks as a dewatering tool that brings material to a conveyable level.
While fine material washers have remained a “go-to” component over the years, today’s dirtier pits often demand more technical solutions.
- Captal Invement: Low
- Power Consumption: Low
- Water Usage: Moderate
- Footprint: High
- Maximum Production: 1,200 TPH
- Moisture at Discharge: Moderate
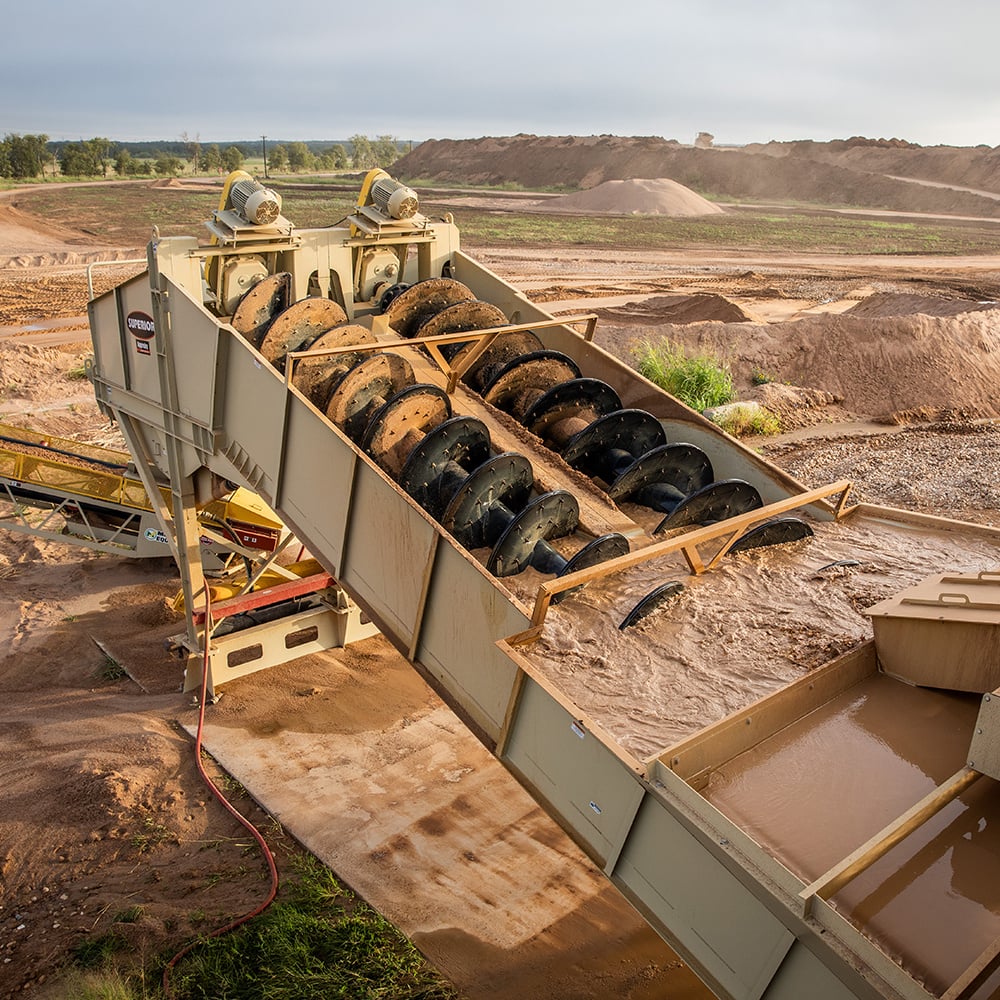
Aggredry® Dewatering Washer
Superior’s Aggredry Dewatering Washer – a combination fine screw and dewatering screen – is designed to overcome many disadvantages of wet processing including water and material waste, stockpiling space , and costly pond maintenance.
As an energy-efficient alternative to the higher horsepower requirements of cyclone plants, the Aggredry Washer achieves precise sand specifications with a final moisture content as low as 8%.
Using as little as one-third to one-half the horsepower per metric ton as that of the typical cyclone plant – the Aggredry delivers considerable energy cost savings, while producing a high-quality finished product that requires no drying time and is immediately saleable.
For further sustainability, the Aggredry Washer minimizes water usage while capturing, recirculating, and recycling valuable water resources within the system – allowing operations to cut water usage when compared to conventional methods.
- Captal Invement: Moderate
- Power Consumption: Moderate
- Water Usage: Moderate
- Footprint: High
- Maximum Production: 600 TPH
- Moisture at Discharge: Low
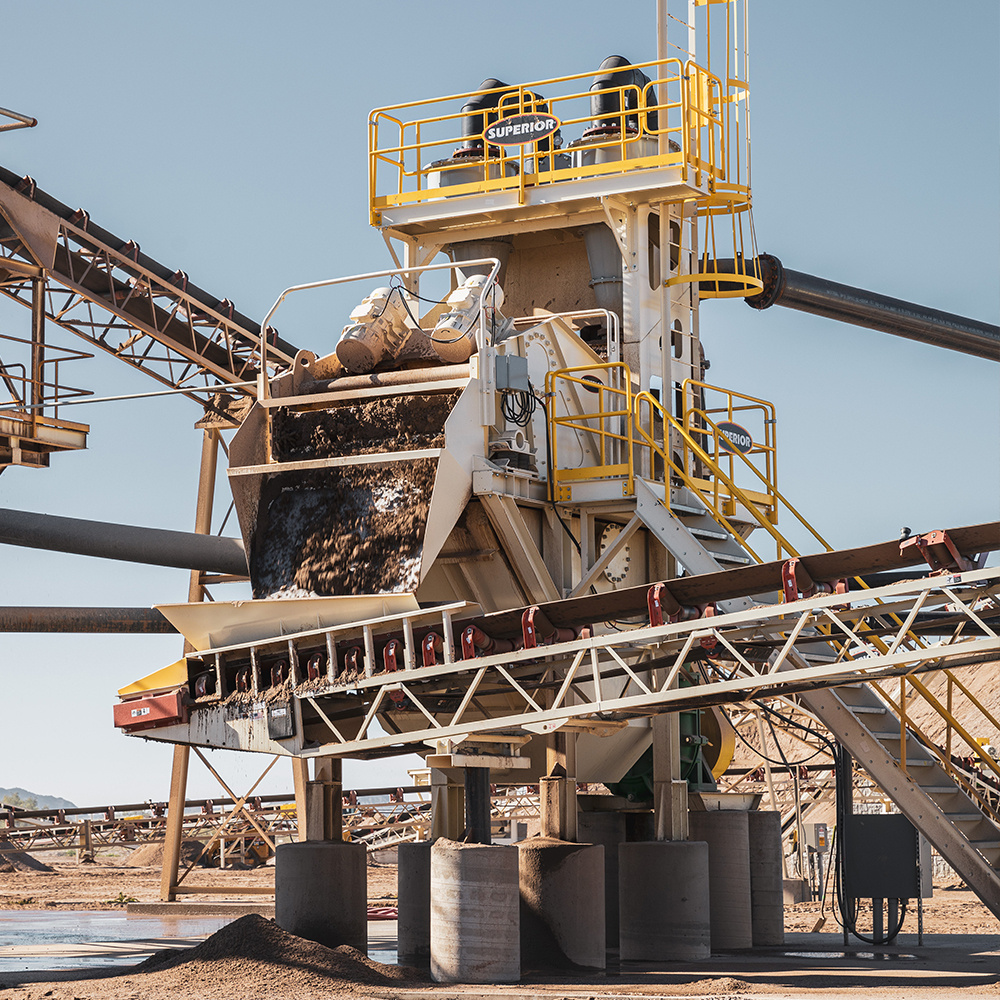
Spirit® Sand Plant
Completely tailored, the Spirit Sand Plant is a modular system that delivers cost-efficient sand production, fines recovery, and dewatering via a single, compact plant.
The modular plant offers custom configurations that combine Superior’s Helix® Cyclones with a dewatering screen, sump tank, and slurry pump. Each plant is configured with the right cyclone and screen for the particular sands and fines recovery cut points. Dewatering screens are sized to the application and installed with the appropriate media and with the required settings and angle of inclination.
Cyclones can be an ideal choice depending upon desired goals – especially where water is scarce and footprints cannot support settling ponds. While cyclones typically consume more horsepower, they can pull out more unwanted silts than a sand screw in one pass and at a more efficient cut point. This results in more fines recovery, maximizing the saleable product to stockpiles, minimizing pond maintenance, and delivering greater efficiency in separating finer materials from the finished product.
- Captal Invement: High
- Power Consumption: Very High
- Water Usage: Very High
- Footprint: Low
- Maximum Production: 300 TPH
- Moisture at Discharge: Low
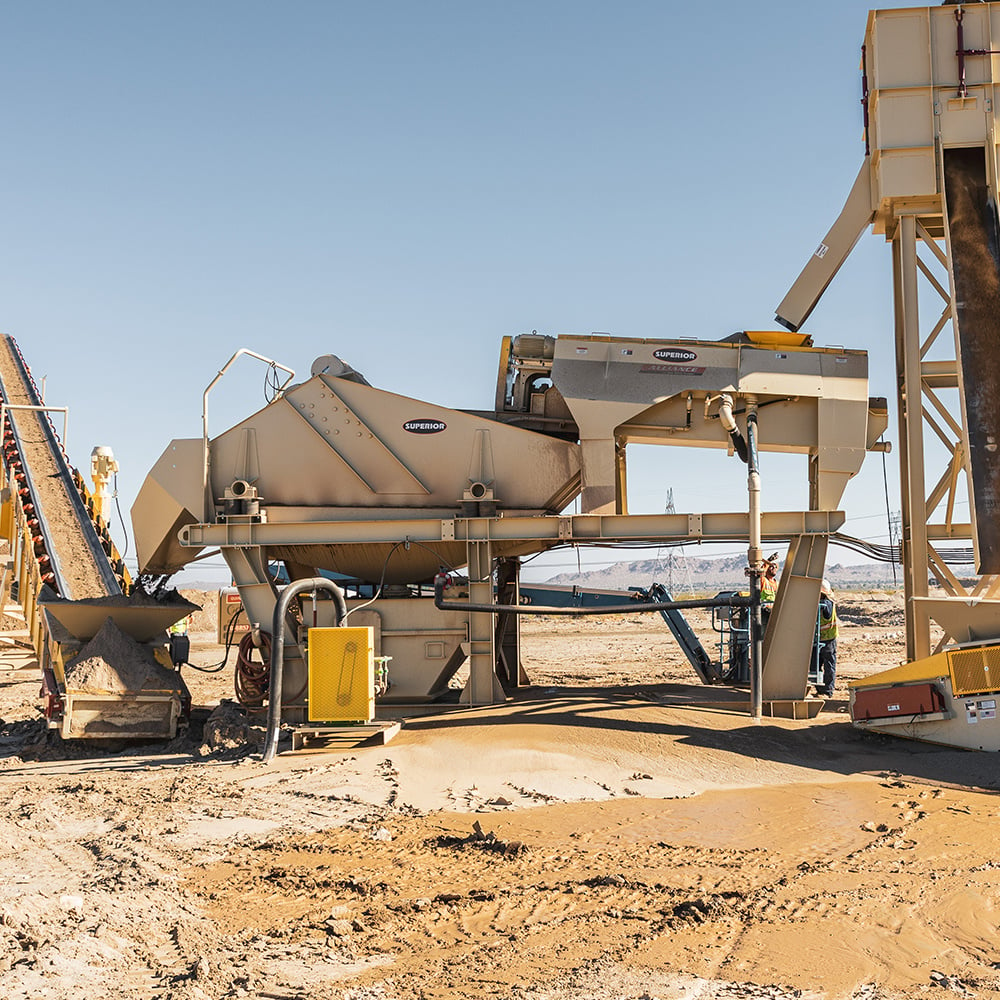
Alliance® Low Water Washer
An issue for many crushing operations is the amount of water required for conventional washing methods.
Superior has engineered an economical solution to efficient crusher fines management with the Alliance Low Water Washer, which combines a specially designed agitator and a dewatering screen within one machine. It allows an operation to wash crusher dust right next to the crushing circuit, eliminating the cost of handling and hauling the fines to a separate washing circuit.
Notably, the system accepts dry feed directly from the crushing circuit and processes the material into a higher-value manufactured sand, while requiring significantly less water in the process.
Consider that a sand screw needs 50-gallons per minute of water for every ton of minus-200-mesh in the feed. Even if an operation is only running at 100-tons per hour, and their minus-200-mesh is at 15-percent – that’s 15 tons of fines requiring 750-gallons per minute of water to adequately lift the silt over the weirs of the screw.
- Captal Invement: High
- Power Consumption: Moderate
- Water Usage: Low
- Footprint: High
- Maximum Production: 300 TPH
- Moisture at Discharge: Low
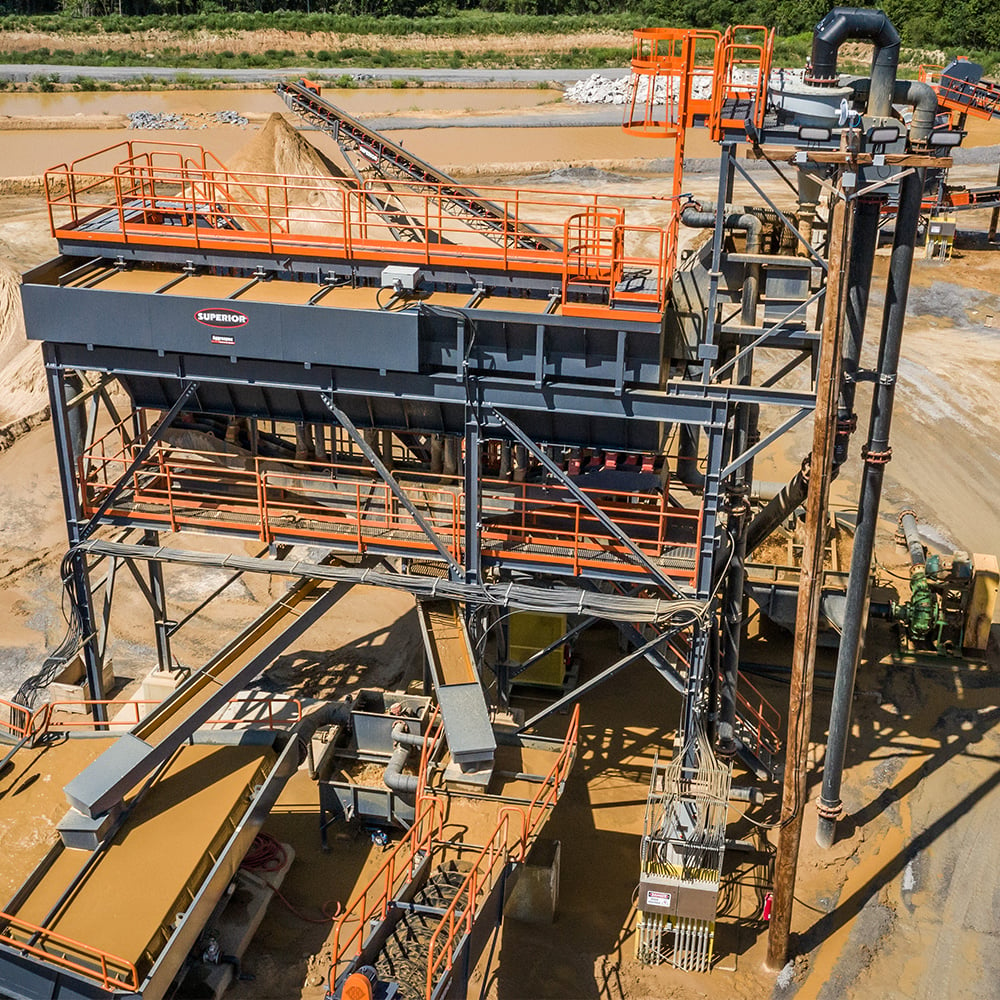
Classifying Tanks
Particularly effective for handling fine materials and making precise cuts, classifying tanks use water, gravity, and settling rates to separate sand into similar mesh sizes while removing unwanted silts.
After sizing and separation, classifying tanks blend sized materials according to specification input. State of the art, computer controlled, high pressure valves allow blending to exacting, top-dollar specifications.
Often seen in dredging applications, classifying tanks are commonly used to remove or scalp off lots of excess water.
- Captal Invement: High
- Power Consumption: High
- Water Usage: High
- Footprint: High
- Maximum Production: 600 TPH
- Moisture at Discharge: High
Producing Cleaner Sand
Depleted natural sand reserves and decade-long permitting processes force producers to mine the entire deposit.
Producing cleaner sand from a dirtier pit demands an ability to combine washing technologies to tackle multiple stages of wet processing and to customize those systems to ensure the right fit for applications that are getting harder to handle in every way.
Almost any equipment combination is possible – such as simply adding a fine material washer after a classifier for dewatering purposes; or putting a cyclone ahead of a classifying tank when dealing with higher percentages of material passing minus-200-mesh.
Another example refers back to the modular Spirit Sand Plant, which offers custom configurations combining Superior’s cyclones with a dewatering screen, sump tank, and slurry pump. By manufacturing a wide range of cyclones and dewatering screens, Superior ensures that the plant is configured with the right equipment for each application.
As Superior manufactures all the processing and material handling equipment and components, each part of the operation can be customized – from the chassis to the washing, crushing, screening, and conveying equipment. It’s also popular to customize the mounting, support structure, and access areas to offer greater flexibility, safety, and ease of maintenance.
Depend on Experts
When considering wet processing solutions, back up your choices with the right expertise from data gathering to design, and throughout installation, startup, and ongoing support.
Let’s face it. Veteran wash plant operators, plus the personnel who’ve “washed rocks for years” are hard to find. Relying upon solid expertise from your chosen equipment manufacturer and their netork of dealers will ensure reliable day-to-day operation, ease of maintenance, and solid staff training.
Whether you’re installing a new wash plant, or upgrading an existing circuit, avoid the so-called quick fix, or the typical choice that’s safe just because it’s always been done before. Instead, realize that when optimizing wet processing solutions, it all depends upon expert analysisto find the right fit for you.
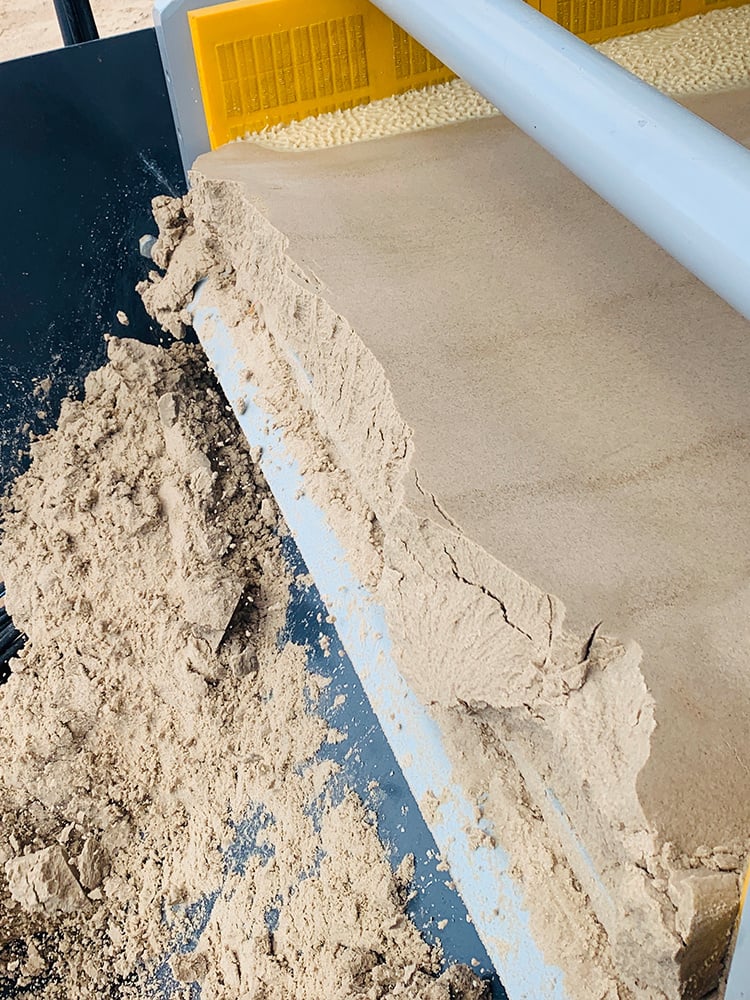
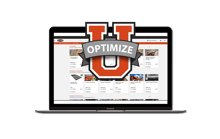
OptimizeU - Strategic Learning
Pursue greater production with comprehensive online courses in crushing, screening, conveying, and washing. Check out the premiere training resource in the construction aggregates industry.
Related Content
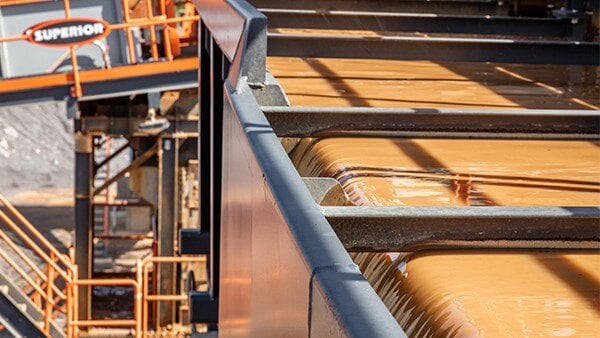
Recycling Wash Water: Water-Saving Basics & Best Practices
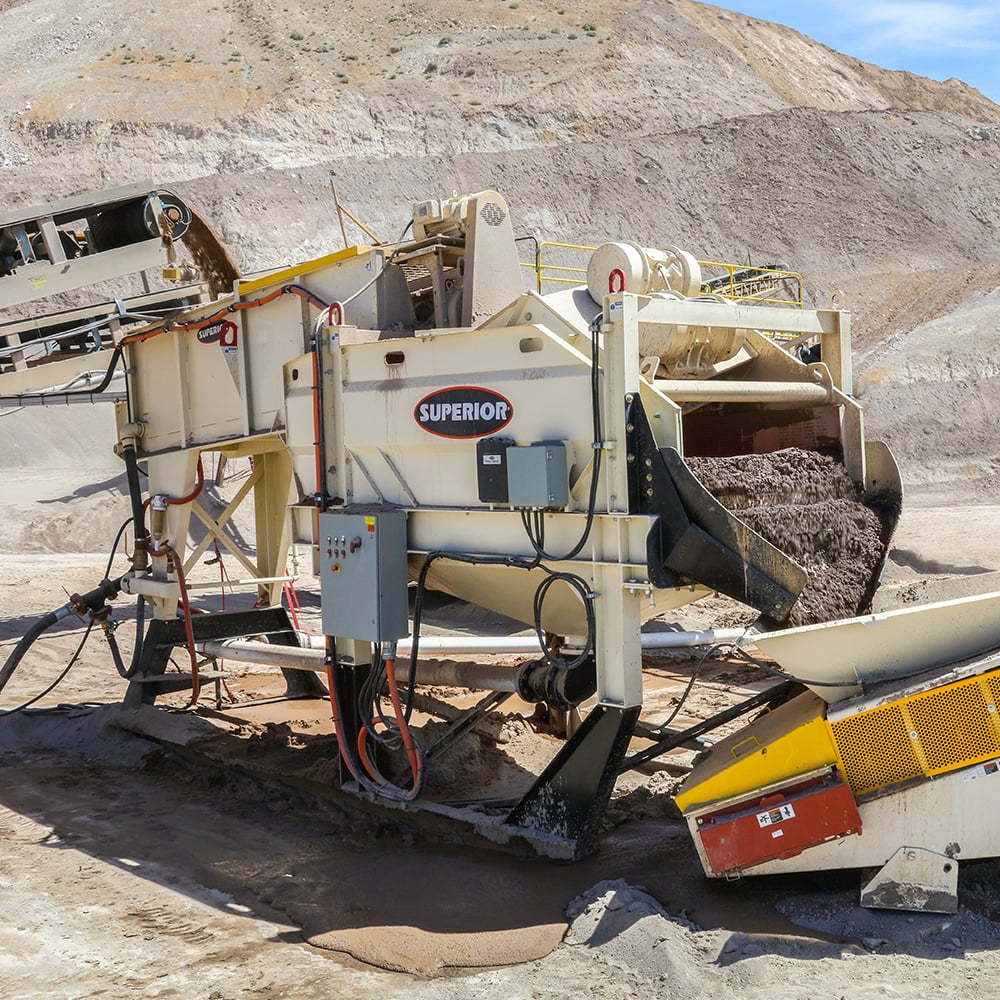
Low Water Sand Processing: Six Things to Optimize Your Wet Processing
20170209_0695-1.jpg)
Maximizing Profits, Minimizing Water Use: Wissota Sand’s Sustainable Solution
Talk to an Expert
Need more information? We'll get you in contact with a product expert in your area.