Tech Tip: Conveyor Belt Mistracking
Causes & Cures
Any effective cure requires a proper diagnosis followed by the correct remedy. Such is the case in conveyor belt mistracking – find the cause before you grab for the cure. There’s no need for a complete system overhaul if a simple tweak will truly solve the problem. Uncover the locations of the mistracking, determine the cause, and then choose the appropriate solution.
This sounds obvious, but consider that belt misalignment (and the resulting material spillage and wear costs) can often be a significant factor behind dwindling profit margins.
The most common causes of belt misalignment are:
- Conveyor structure and/or component problems
- A warped or improperly spliced belt
- Off-center material loading
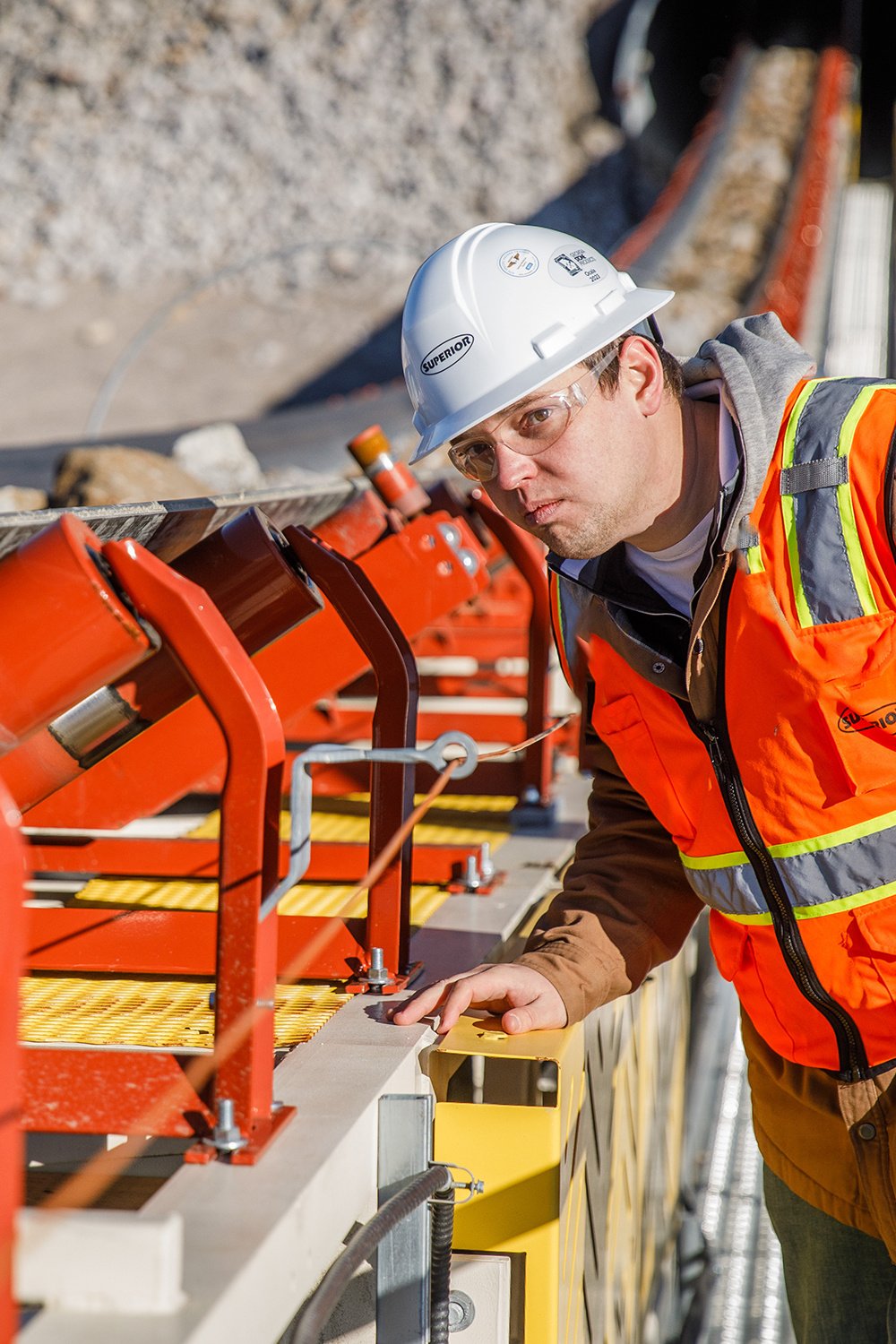
If a belt is free from any warping and curvature, and if proper material feeding systems are in place, then that belt can be trained to travel over the center area of troughing idlers, pulleys and return idlers. This is vitally important to trouble-free operation and minimized maintenance costs. Belt training involves adjusting idlers and loading conditions in a manner that will correct any off-center operation. The following basic steps in belt training are commonly known as “squaring the system.”
Squaring The System
- Level the frame. (Gravity forces the belt off-center if one side of the conveyor frame is lower than the other.)
- Square the tail pulleys with the frame. Be certain that all major pulleys are parallel, square, and functioning.
- Square all idlers with the frame. Measure from a straight edge on both sides of the conveyor and tighten the bolts.
- Square the belt splice. If there is a side creep at the splice area only, and this progresses along the conveyor instead of remaining at one point on the frame, the splice may have to be redone.
- Never attempt to train the belt by unequal adjustment of take-ups. Take-ups are used to maintain belt tension, not tracking.
- Adjusting individual idlers is commonly known as “knocking the idlers.” Loosen the bolts and pivot the idler. Mark the spot where the belt goes off to one side and locate the idler that precedes it by 15-25 25. Turn that idler slightly in the direction in which the belt is mistracking. If the belt continues to wander, follow the same process with the next idler closest to your mark.
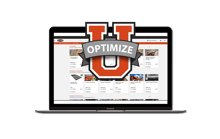
OptimizeU - Strategic Learning
Pursue greater production with comprehensive online courses in crushing, screening, conveying, and washing. Check out the premiere training resource in the construction aggregates industry.
Related Content
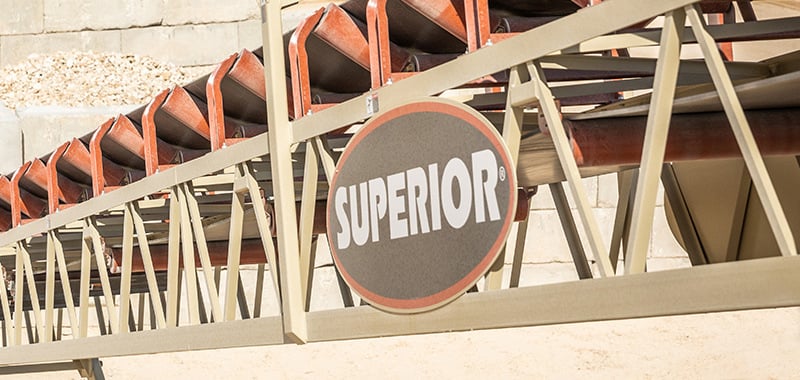
Conveyor Maintenance: Basic Design to Increase Your Uptime
Designing a conveyor to be maintenance friendly means providing adequate provisions for necessary service from the onset.
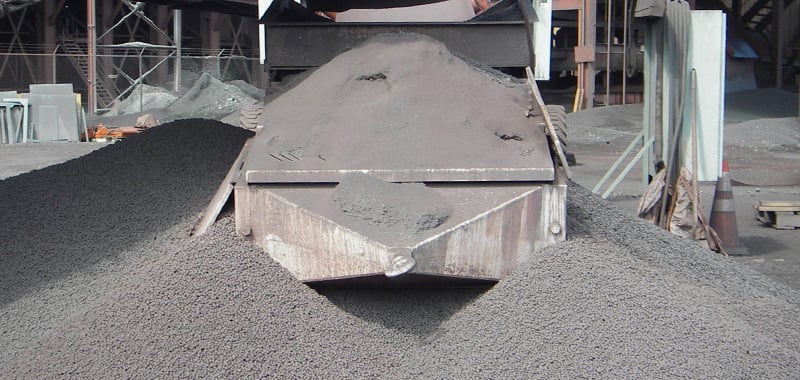
Conveyor Load Zones: Prevent Spillage with Simple Maintenance
Material spillage is a costly proposition and is common to many operations due to a lack of good preventive maintenance.
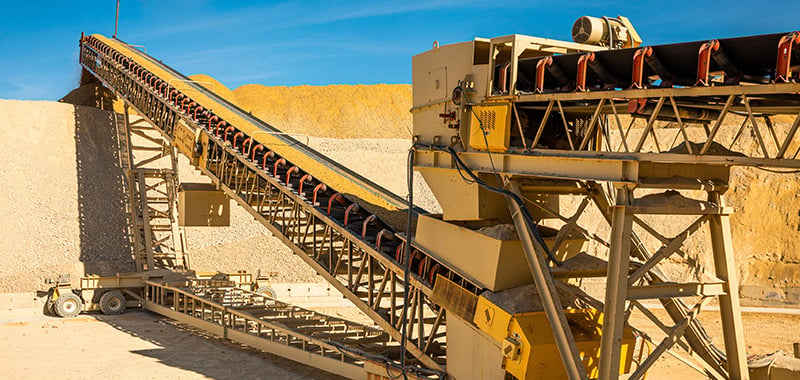
Conveyor Transfer Points: Useful Tips to Eliminate Spillage
Preventing spillage at transfer points is imperative, since cost reductions from elimination at one transfer are significant.
Talk to an Expert
Need more information? We'll get you in contact with a product expert in your area.