Tech Tip: Vantage® Intelligent Idlers
The Superpowers of Smart Conveyor Idler Rolls
Protecting operations from the potential of costly fire damage – and pinpointing even the slightest problem before it erupts into downtime. For next-level conveyor system monitoring, intelligent idlers access Industrial Internet of Things (IIoT) technologies.
These ever-expanding technologies are new to idler roll design and involve embedded hardware which transforms a passive roll into an active inspection tool. Its implementation, which began in the mining industry, is steadily emerging within other types of large dry bulk applications worldwide – specifically those that involve combustible materials such as the loading of coal onto maritime vessels, or the processing of paper and pulp.
Keeping An Eye On Hot Spots
Superior Industries, a U.S.-based bulk processing equipment manufacturer, engineered the first-of-its-kind Vantage® Conveyor Monitoring & Cloud Services System at the company’s Brazilian manufacturing facility which has traditionally served the region’s mining industry.
In mining operations particularly, potential conveyor belt fires are a serious threat to worker safety, capital equipment investments, and production output. As a sought-after solution, the Vantage System identifies and collects data on idler bearing temperature, rotation, and vibration, allowing operations to prevent catastrophic fires and production downtime by easily locating an idler roll hot spot before the component sparks or fails. Measured by different sensors embedded inside the rolls, key idler performance parameters and alerts are displayed on a control room computer screen or mobile device in real time.
Idler roll failures cause unplanned downtime, increasing operating costs, and putting at risk not only the equipment assets, but also the workers involved in the operation, inspection, and maintenance process. Certainly, traditional methods of detecting elevated temperatures and signs of potential failure of the idler roll are only marginally effective. Also, applications such as ship loaders, covered, or confined conveyors do not allow proper inspection while in operation.
The sheer quantity of idler rolls installed amplifies the problem. Consider that in Brazil, there are more than three million rolls installed. Assuming a replacement rate of 10-percent per year, mining operators have the impossible challenge of finding, every day, the 1,000 rolls that will reach the end-of-life among the three million installed. It’s like finding a needle in a haystack, and such a challenge requires a system that can collect and manage enormous amounts of data.
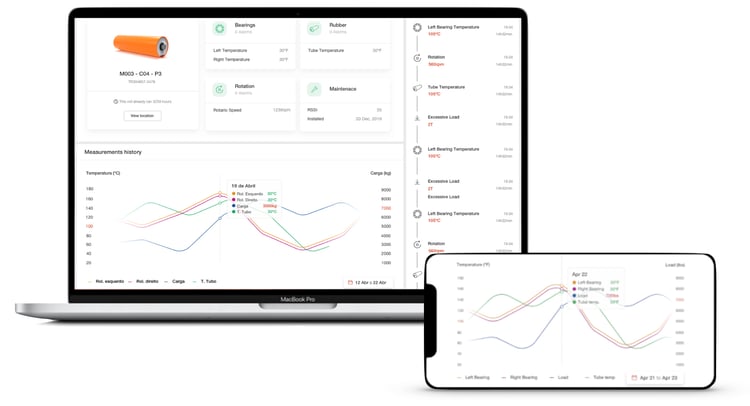
Behind The Vantage Technology
Within the Vantage System, both the software and hardware components are entirely developed by Superior Industries. With the advent of IIoT technology, opportunities opened to develop new forms of sensing and telemetry – and with the miniaturization of electronic components and the emergence of LPWAN (long-power/long-range) communication protocols such as LoRaWAN – Superior engineers found that idler roll monitoring is cost-effective and sustainable. Consider that a single gateway has a communication range of up to one mile and can connect with up to 3,000 devices.
Rolls operate in very harsh environments, filled with dust. They are subject to maintenance procedures that include periodic high-pressure washing. Additionally, roll installation practices often require workers to hit rolls with hammers or mallets to ensure a proper fit within older, existing idler frames. Each of these issues make the use of any external sensors quite risky. As such, Superior has embedded the sensors within the roll, allowing greater protection and accuracy, and there are no external antennas or connection wires.
For example, the bearing temperature sensors are placed in contact with the inner race of each bearing, providing a more reliable and accurate method for measuring bearing temperature. Alternatively, sensors that measure bearing temperature by indirect means, such as sensors placed on idler frames, result in a much lower degree of accuracy – as the separation between the sensor and the bearing allows too much heat dissipation, particularly in colder climates.
The monitored roll is as easy to install as any standard roll. Once the infrastructure and configurations are completed in the implementation phase, replacing a roll with a new one follows the same process as a standard roll. The only difference is the need to inform the system of the roll position, either through scanning the QR code of the new roll in a mobile device in the field or logging its position via the web. Recording the position of the roll is important as any alarm or alert can be related to the precise location of the roll. As soon as the conveyor is running again, the new roll will communicate with the cloud.
Data Delivery
Measurements from each of the different built-in sensors is available in real time, and data is transmitted using cost-efficient LoRa™ radio signals which require minimal energy and can “sleep” when not in use. The system monitors the data from each roll and sends it to the cloud using a LoRaWAN infrastructure.
Each idler roll has its own embedded generator (also developed by Superior) that creates the necessary energy to send data when in operation, even in low RPMs. This eliminates the use of a battery, which not only improves safety but also eliminates the issues involved in discarding used batteries.
Regarding software, the system incorporates certain features and algorithms to facilitate data analysis and create valuable operating information. Collecting data from the rolls allows operations to monitor the overall health of the conveyor. For example, it’s possible to view the temperature gradient of the conveyor and identify critical points such as uneven idler frames or a misalignment of the belt. Individual dashboards for each roll provide a detailed analysis of temperatures, vibration, and speed.
Alarms activate based on predetermined parameters for each type of roll and application. By triggering alarms based on predetermined parameters, operators can access the right information for their specific application and can take immediate action, minimizing any potential risk or damage.
Monitored Rolls With Flame-Retardant Rubber
To further mitigate fire risks, Superior has developed a UL94-V0 flame-retardant rubber, which is certified by the Mine Safety and Health Administration (MSHA). The specially formulated rubber compound coats the impact and return rolls to deliver abrasion and hardness levels compatible with those of the belts.
Superior’s Vantage System and the special UL94-V0 flame-retardant rubber is installed on the new Drum Reclaimer 3 at the Brucutu Mine, which is the second largest mine in Brazil, producing 30-million tons of iron ore annually. The new Drum Reclaimer is among the largest in the world in terms of iron ore capacity and is responsible for feeding the beneficiation plant. This is the world’s first machine with 100-percent monitored rollers.
Due to safety reasons, workers cannot enter the interior of the drum reclaimer while it is operating. If there is an attempt to open the access door, the operation is automatically interrupted, which is why electronic monitoring is so important.
The use of Superior’s monitoring solutions demonstrates the mine’s commitment to ensuring employee safety, while maintaining machine availability – and even reducing insurance costs due to increased machine protection and worker safety.
Also, amid growing concerns over pollution and worker health, regulations affecting material handling are rising, particularly in urban centers. As such, more operations are enclosing conveyors or using wind fences to prevent material loss. This creates confined spaces that make human inspection impossible. Consequently, next-generation conveyor monitoring is emerging as a viable option.
Transformation Via Technology
Superior’s conveyor monitoring technologies ensure roll failure detection capabilities, prevent fire, and belt damage, and reduce unexpected shutdowns, maintenance costs, and production losses – while improving operator safety. With 24/7 monitoring and predictive algorithms, operations can practice proactive maintenance strategies, while preemptively scheduling roll replacements, and avoiding production disruptions.
There is a growing demand for conveyor monitoring technologies in critical applications such as mining, ship loading, coal, paper and pulp, and other high-impact, high-value operations. As the cost of this technology is rapidly decreasing, it is probable that soon, all rolls shipped from Superior’s Brazilian manufacturing plant will leave as ‘intelligent’ idler rolls – already embedded with sensors and ‘superpowers.’
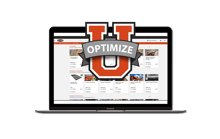
OptimizeU - Strategic Learning
Pursue greater production with comprehensive online courses in crushing, screening, conveying, and washing. Check out the premiere training resource in the construction aggregates industry.
Related Content
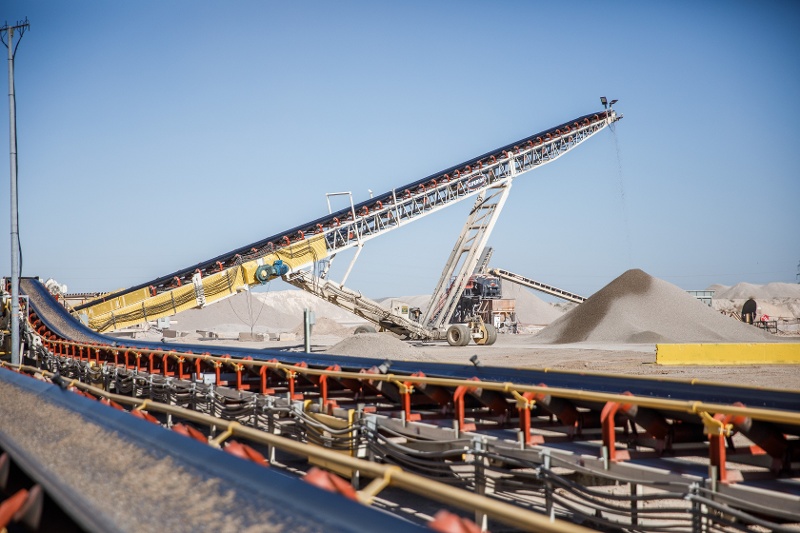
Consistency in Components: Standardization is Key for Conveyor Parts
Producers can avoid costly downtime headaches by standardizing conveyors and components for easy, cost-effective maintenance.

Conveyor Idlers: Don’t Overlook This Most Critical Component
While reliability of each conveyor component is key, it’s the often overlooked idler that should always receive proper consideration.
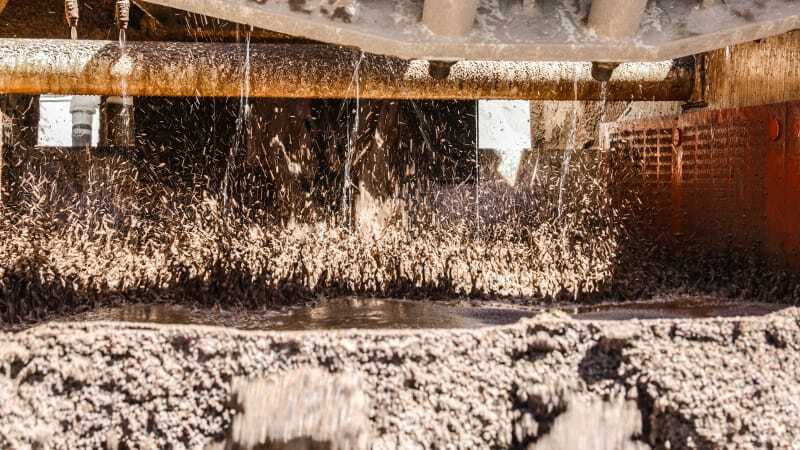
Low Water Sand Processing: Six Things to Optimize Your Wet Processing
Ensuring the proper jaw crusher closed-side setting size is essential for proper material flow throughout the entire plant.