Tech Tip: Sizing the Jaw Crusher
Three Simple Rules to Size By
Whether you’re a seasoned crushing veteran, or tackling your first season on the job, one should always employ the “best practices” toward crushing efficiency.
“First off, specifying the right jaw crusher for ‘the given application parameters’ is essential to cost-per-ton efficiency,” says Jarrod Adcock. As the Crushing Product Manager with Superior Industries, Adcock helps producers fine-tune crushing circuits to ensure proper material flow throughout the entire plant.
He outlines three simple rules behind properly sizing a jaw crusher.
Rule #1: Identify Maximum Feed Size
The size of the crusher opening directly determines the maximum feed size going into the crusher. For example, if the jaw has a 30-inch opening (gape), the maximum feed size should not exceed 80% (or 24-inches).
Rule #2: Determine Desired Product Size
Your closed-side setting (CSS) of the crusher determines the desired product size that will be produced. The CSS is the minimum distance between the jaw liners at the bottom of the crushing chamber when in operation. For example, a 40x51-inch jaw crusher calls for a maximum feed size of 32-inches (a CSS range of 4-8 inches) and produces a desired product size that fits within that CSS range.
Rule #3: Define Tonnage Goals
The desired production capacity, or tonnage-per-hour required directly correlates to the width of the crusher and the closed-side setting. That means that a jaw with a 42-inch width – and a CSS range of 2.75-inches to 8-inches – will average a production capacity of 165-550 tons per hour, while a similar crusher with a 55-inch width will have a capacity range of 265-855 tons per hour.
Adcock says that another element to consider in crusher capacity is material hardness and the percentage of material in the feed that is smaller than the crusher CSS.
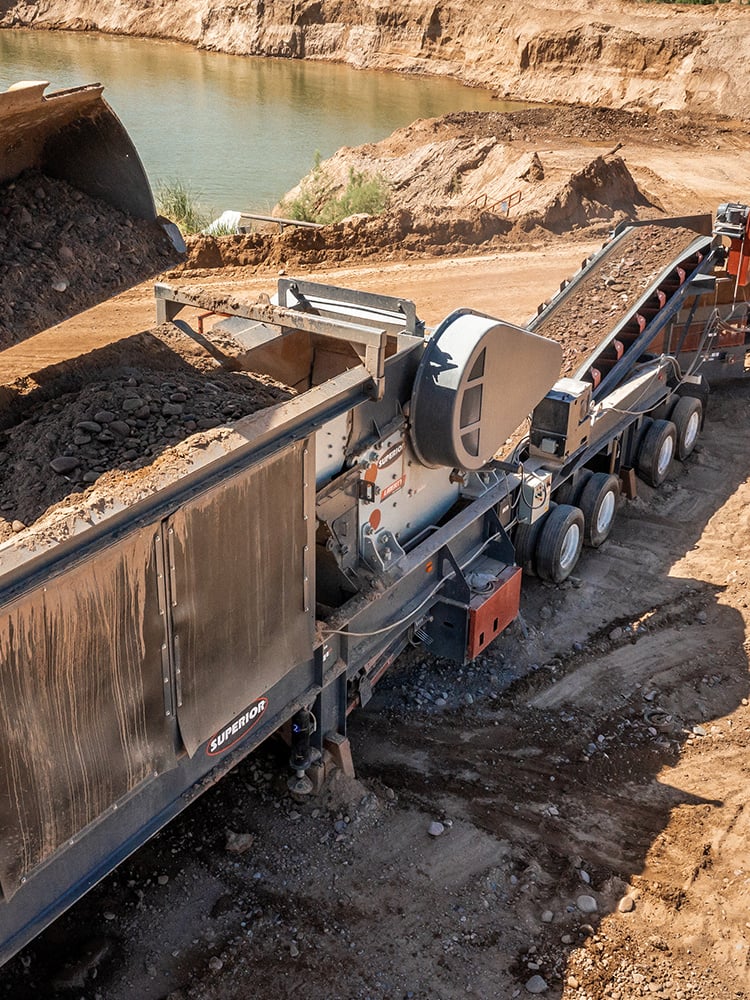
Right-sizing From the Start
Always match the crusher to the task. If the jaw crusher is too small, you’re not going to get the desired tonnage out of the machine – and if your feed material is too large, you will certainly experience excessive wear and tear, plus costly damage and downtime.
Alternatively, if the jaw crusher is too large for the application – the operation is spending too much money within that circuit and is inefficient in purchasing power.
Most producers can easily identify the jaw crusher size they’re looking for, as their choice is often based upon what jaw they previously ran – and if they need something similar or different. However, there are also those operations who rely upon the assistance and expertise of their chosen crusher manufacturer.
Bottom-line, Adcock says that if the producer provides accurate data on feed size, desired product size, and tonnage goals, “we can select the right crusher for the application.”
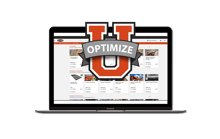
OptimizeU - Strategic Learning
Pursue greater production with comprehensive online courses in crushing, screening, conveying, and washing. Check out the premiere training resource in the construction aggregates industry.
Related Content
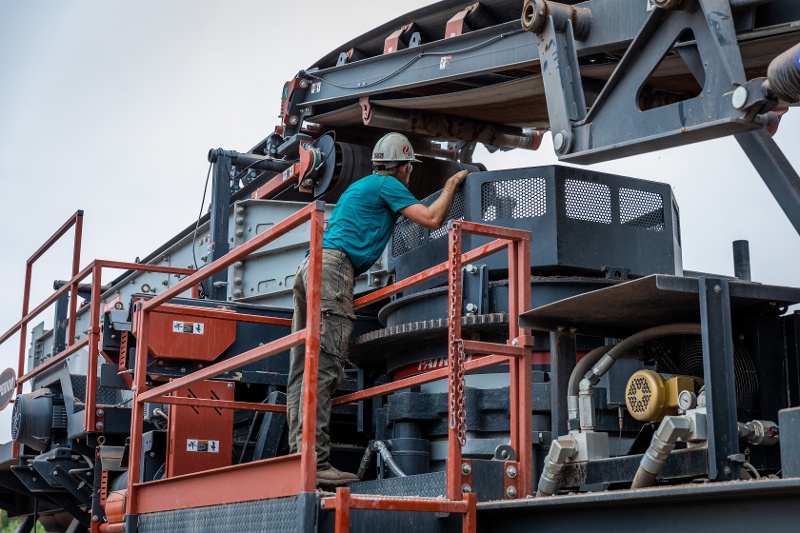
Maximizing Cone Crusher Performance: Achieve Peak Performance in Quarrying & Mining
Maximize cone crusher performance in quarrying & mining with proactive maintenance, proper circuit design, and easy-to-use automation. Learn how to achieve peak crushing performance.
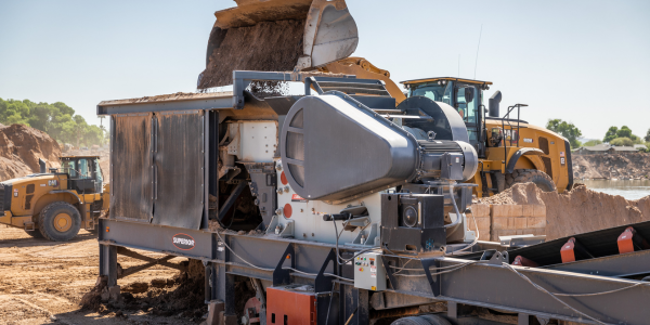
Selecting Jaw CSS: Maintain the Right Closed Side Settings
Designing a conveyor to be maintenance friendly means providing adequate provisions for necessary service from the onset.
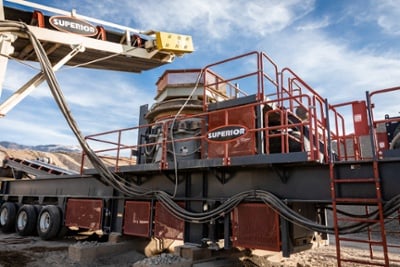
Cone Liner Selection: The Right Data for the Right Fit
Select the right cone crusher liner by understanding your application needs and feed size. Collaborate with experts to optimize processing circuits and maximize productivity.