CASE STUDY
Arcosa Aggregates: Seven Points Pit
- Enis, Texas
- LOCATION
- Aggregates: Sand & Gravel
- INDUSTRY
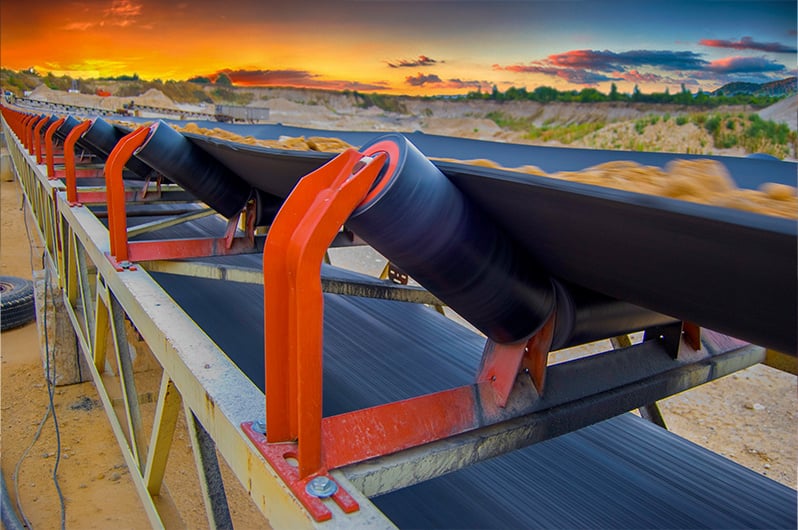
The Challenge
At Seven Points Sand & Gravel, traditional steel idler rolls proved problematic in their sand processing operations. Plant Manager Clay Wittwer faced frequent maintenance issues, including weekly roll changeouts due to sand contamination, which accelerated wear on the steel rolls. These problems often led to severe tracking issues, belt damage, and costly downtime. The challenge was to find a more durable solution that could withstand the harsh conditions and reduce maintenance frequency.
“This decision alone [to switch from standard steel to Moxie Rolls] is one of the biggest keys to our current efficiency.”
The Solution
During an upgrade to a new 400-tph wash plant, Seven Points Sand & Gravel opted to replace their traditional steel idler rolls with Superior Industries’ Moxie® Rolls, made from high-density polyethylene (HDPE). This retrofittable solution to their existing idler frames offered enhanced corrosion resistance, better material shedding, and a robust seal design. The Moxie Rolls feature SpinGuard® Bearing Seals with triple labyrinth technology to protect against bearing damage and minimize maintenance needs.
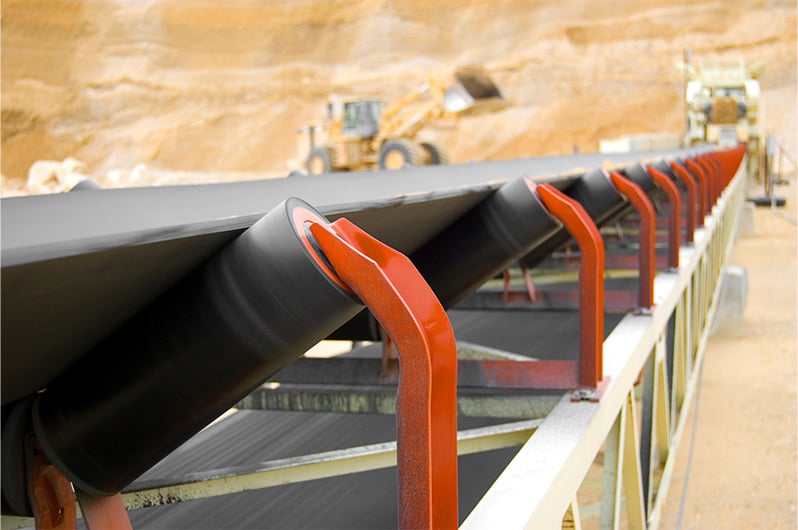
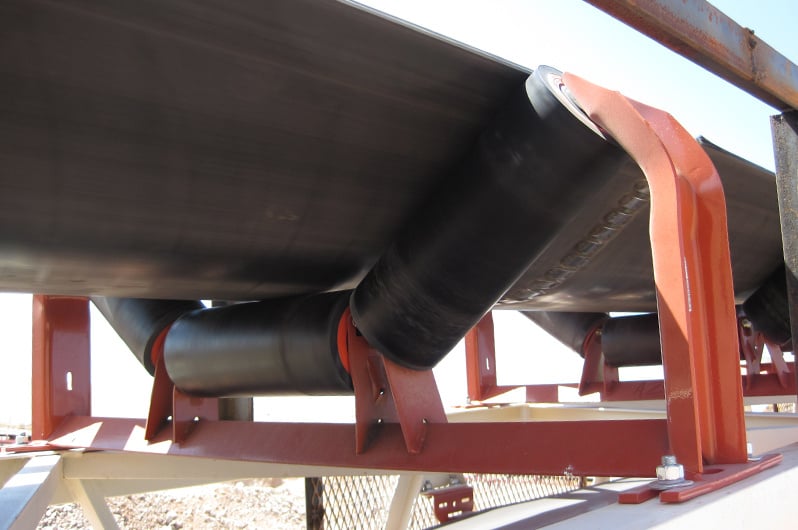
The Results
The switch to Moxie Rolls significantly improved maintenance efficiency and reduced operating costs. The new rolls offer extended wear life, lower roll resistance, and are up to 50% lighter than steel rolls, easing the burden of roll replacement when necessary. Additionally, the HDPE material reduces noise and is less prone to corrosion and material buildup. The pit has experienced fewer roll changeouts and lower overall maintenance, leading to increased operational efficiency and cost savings.
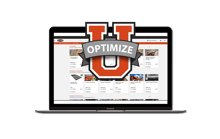
OptimizeU - Strategic Learning
Pursue greater production with comprehensive online courses in crushing, screening, conveying, and washing. Check out the premiere training resource in the construction aggregates industry.
More Projects & Resources
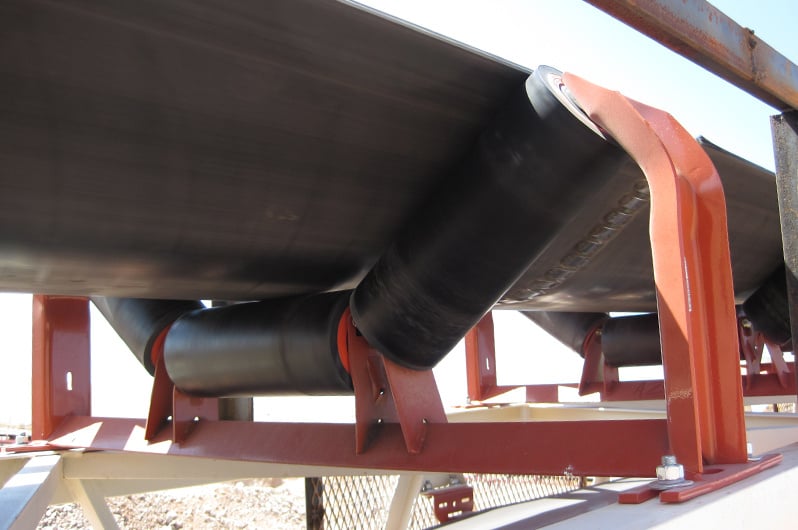
Harsh Application is Achieving 4x the Wear Life with Moxie® Rolls
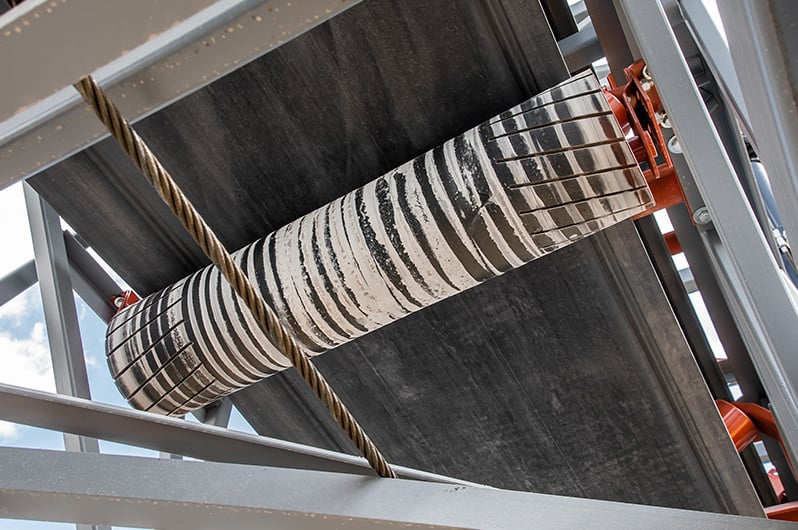
Killeen Crushed Stone’s Conveyor Belt Tracking Breakthrough
