Case Study
Carver Companies
- Charleston, South Carolina
- LOCATION
- Ocean Terminal: Ship Unloading
- INDUSTRY
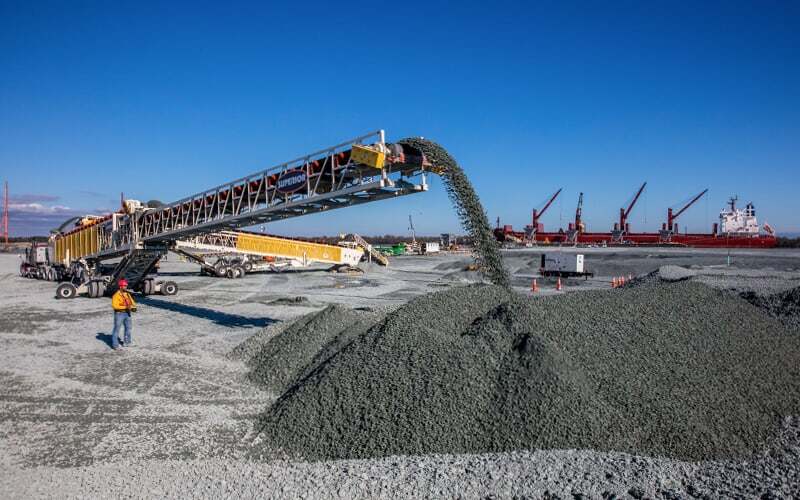
The Challenge
The South Carolina Ports Authority (SPA) faced a significant logistical and environmental challenge during the construction of the Hugh K. Leatherman Sr. Terminal. As part of their largest capital improvement initiative, the SPA needed to import nearly 4 million tons of aggregate fill material to prepare the 280-acre site for its eventual role in handling up to 1.4 million cargo boxes annually.
The SPA sought to avoid the emissions, dust, noise, and traffic congestion that would result from trucking the aggregate over land. Instead, they required a more efficient and environmentally friendly solution for offloading and distributing the material directly from ships.
“I’m big on buying American-made equipment and the Superior equipment is top-notch. Plus, the support they give us is an extreme blessing.”
The Solution
Carver Companies, specialists in marine offloading and material handling, provided a highly mobile and versatile conveying system to meet the SPA’s requirements. The setup featured a 72-inch RazerTail® Truck Unloader, multiple 42-inch Zipline® Conveyors, and several TeleStacker® Conveyors.
The system allowed for the seamless transloading of material from ships to a stationary barge outfitted with hoppers, which then fed the aggregate via the Zipline Conveyors to an onshore TeleStacker Conveyor. From there, the material was transported to the containment area using a 500-foot Trailblazer® Conveyor and distributed across the site using additional TeleStacker Conveyors. This mobile system provided the flexibility to handle varying material types and vessel sizes while operating within the limited footprint of the construction site.
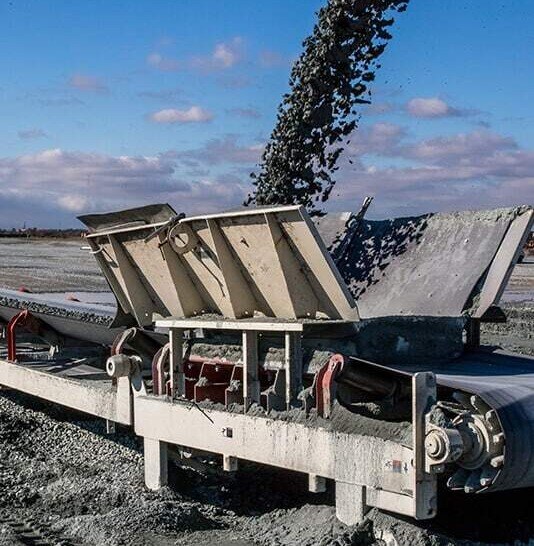
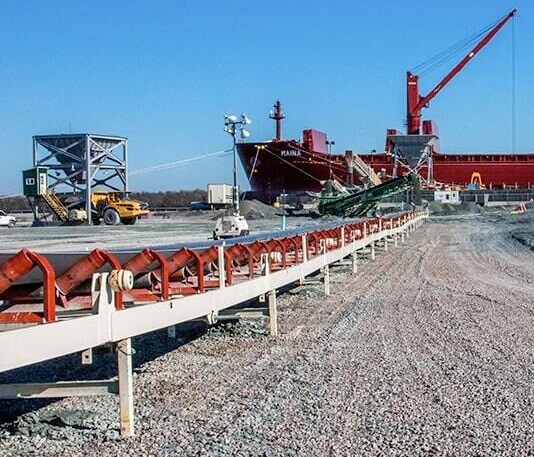
The Results
Carver Companies’ mobile conveying system successfully offloaded and distributed the aggregate material at a rate of 1,000 to 1,300 tons per hour, significantly reducing the time and cost associated with the project. The use of mobile conveyors eliminated the need for multiple material handling steps, such as using trucks and loaders, which resulted in substantial savings in labor, fuel, and equipment wear.
The system’s ability to operate efficiently within a confined space also minimized emissions and dust, aligning with SPA’s commitment to community and environmental mitigation. The successful implementation of this system positioned Carver Companies for future growth, with the capability to quickly deploy their mobile conveying equipment to other projects along the East Coast.
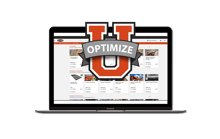
OptimizeU - Strategic Learning
Pursue greater production with comprehensive online courses in crushing, screening, conveying, and washing. Check out the premiere training resource in the construction aggregates industry.
Related Content
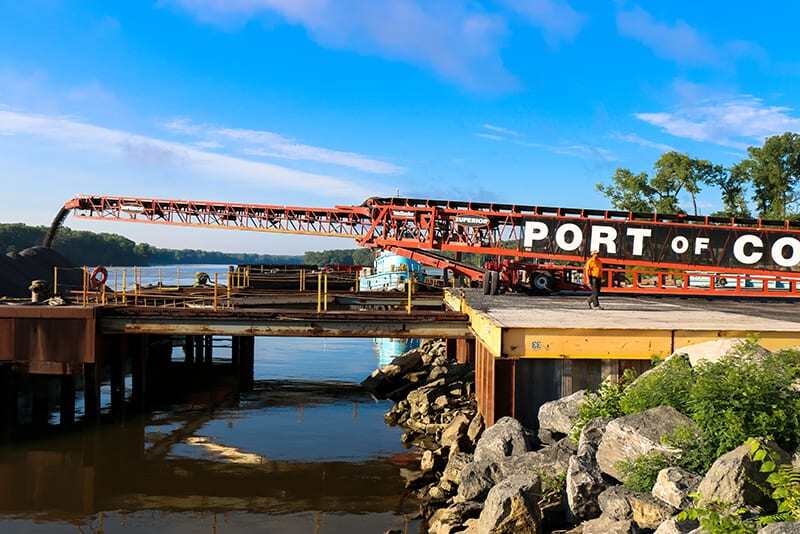
Carver Companies Saves $1 Per Ton on 2 Million Tons Annually at Port of Coeymans
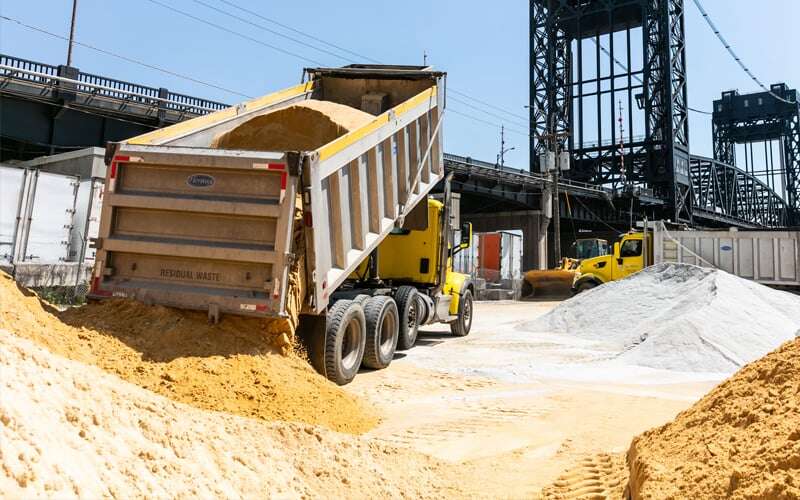
Gotham Aggregates Cuts Shipping Costs by 35% with Barge-Loading TeleStacker® Conveyor
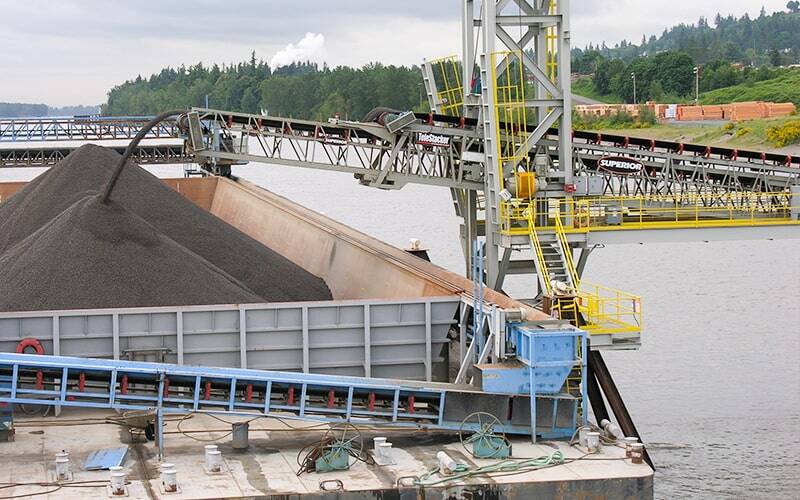