Case Study
Wissota Sand & Gravel
- Milwaukee, Wisconsin
- LOCATION
- Aggregates: Sand & Gravel
- INDUSTRY
20160824_0749-1.jpg?width=800&height=533&name=Wissota%20Sand-Richfield%20WI-Site%20Visit%20(2016-08)20160824_0749-1.jpg)
The Challenge
Wissota Sand & Gravel, a Milwaukee-based aggregate supplier with a century-long legacy, faced significant challenges in managing water resources while meeting the growing demand for washed aggregates.
The traditional sand screws used in their operations were producing sand with a high moisture content of 25%, leading to substantial water loss and inefficiencies. The company was losing about 400 gallons of water per minute, which required costly and unsustainable practices such as pumping from deep wells.
Additionally, managing fines and reducing waste were becoming increasingly difficult, especially as the face of the pit changed and dirtier material needed processing.
The Solution
To address these challenges, Wissota Sand & Gravel invested in the Aggredry® Dewatering Washer, an innovative system designed and manufactured by Superior Industries. This system combines fine material washers with high-frequency dewatering screens, effectively reducing the moisture content of the sand to just 8%.
The Aggredry Dewatering System also includes a fines recovery mechanism that reintroduces minus-quarter-millimeter sand back into the process, significantly improving fines management. This technology allowed Wissota to wash at a higher throughput while achieving better results with less water usage. The system's efficiency also reduced the need for extensive drying time and minimized wear and tear on equipment.
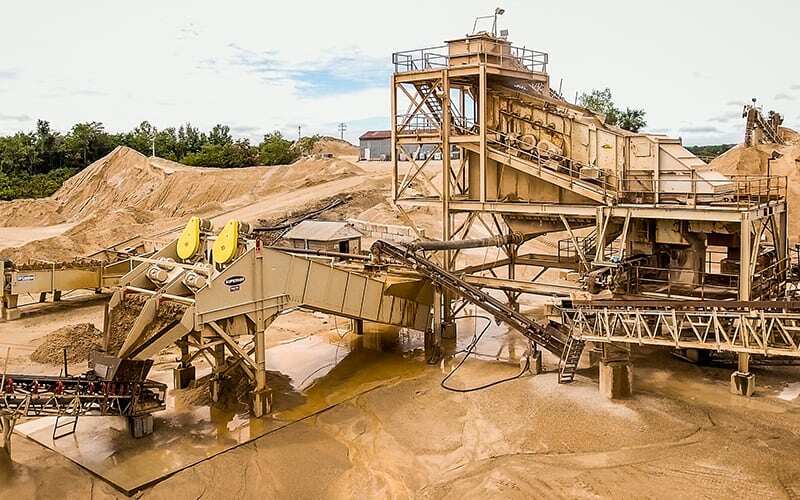
"With our prior sand screws, we could wash at 50 tons per hour and we would have to wash it twice to get to the three percent. With the new unit, we can wash at 100 tons and achieve less than three percent fines after washing it just once.”
20160824_0767-1.jpg?width=800&height=533&name=Wissota%20Sand-Richfield%20WI-Site%20Visit%20(2016-08)20160824_0767-1.jpg)
The Results
The implementation of the Aggredry® Dewatering Washer resulted in substantial improvements for Wissota Sand & Gravel. The operation now produces sand at just 8% moisture content, eliminating the need for prolonged drying periods and reducing water usage by about 350 gallons per minute. The fines recovery system saved up to 3% of material that would have otherwise been lost, translating into additional saleable products and increased profitability.
Furthermore, the improved efficiency allowed Wissota to handle dirtier material from the pit without compromising the quality of the final product. Overall, the new system not only supported Wissota's sustainability initiatives but also enhanced their ability to meet growing market demand while conserving valuable water resources.
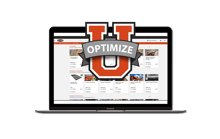
OptimizeU - Strategic Learning
Pursue greater production with comprehensive online courses in crushing, screening, conveying, and washing. Check out the premiere training resource in the construction aggregates industry.
Related Content
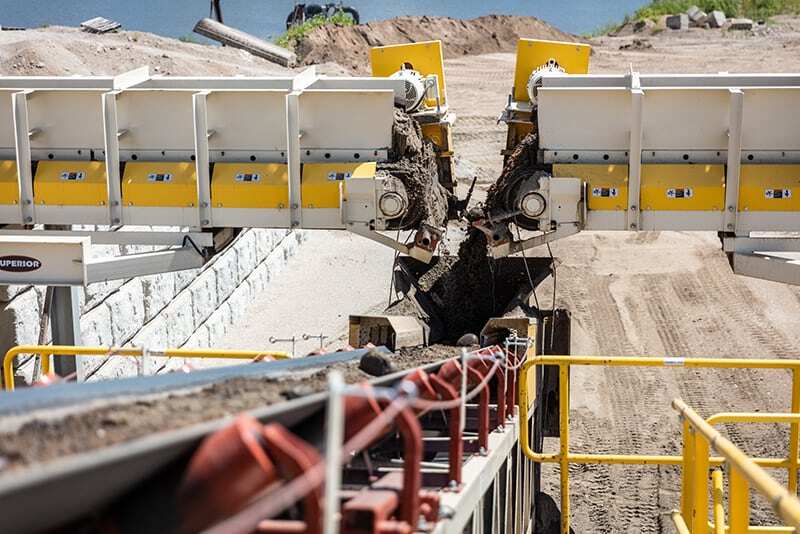
Cemstone Upgrades Operations with Aggredry® Washer for Immediate Saleable Product
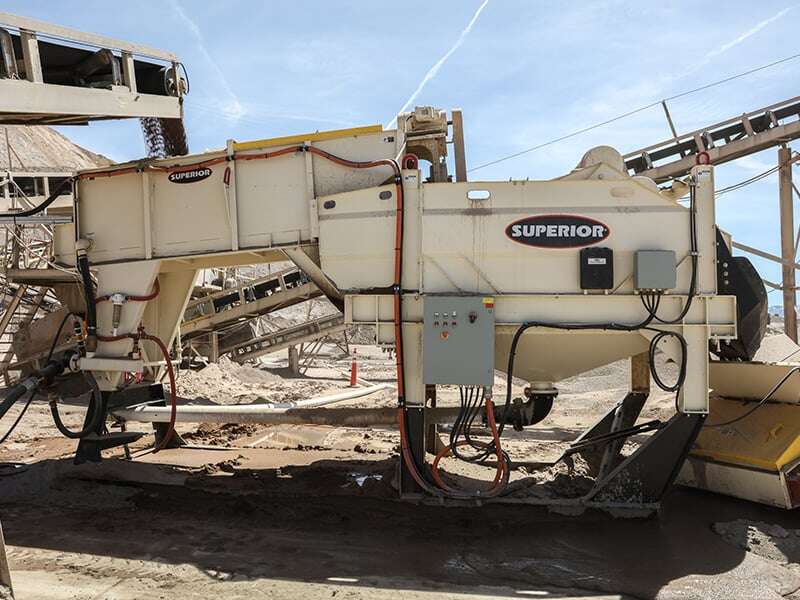
New Value From Crusher Fines: A Low-Water Solution for Manufactured Sand
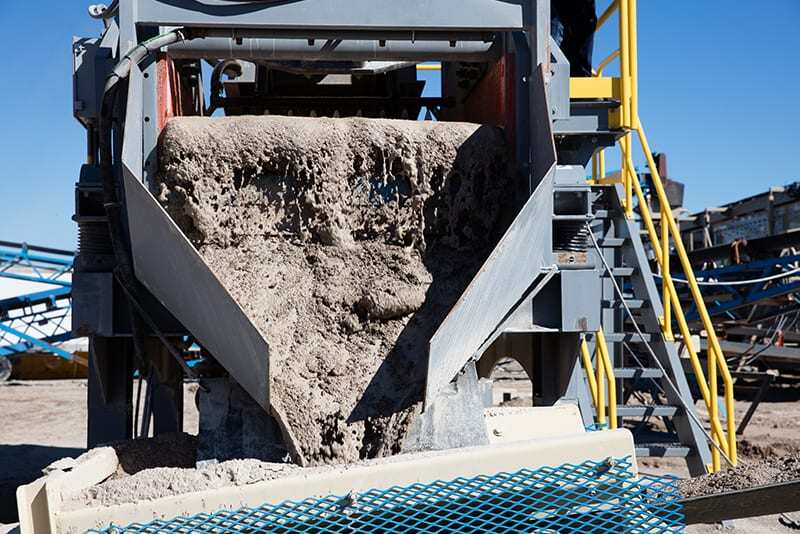