Tech Tip: Screening Troubleshooting
Using Your Senses to Detect Vibrating Screen Issues
Stop a second – and just observe.
“What do you see, hear, or smell when taking an up-close look at a vibrating screen?" asks Ed Sauser, Superior's vibratory product manager. "Using their senses, many veteran plant operators are keenly aware of the sights, sounds, and smells that signal proper screen operation, or a potential need for maintenance.”
But whether you’re an industry veteran or a new trainee, Sauser stresses the importance of developing your observation skills when troubleshooting equipment. He shares what to look, and listen for, when the screen is running – and a few things to observe and note when inspecting the machine during shut down.
Look for Symmetrical Operation
When the screen is running, look for even operation from side to side. Is one side of the screen moving identically to the opposite side? Screen operation must be symmetrical. If not, screening efficiency is immediately affected, while costly damage to the machine is likely over the long term.
While operations may use the latest electronic sensors or gauges to measure the stroke (motion) of the machine, a manual “tracing” exercise has commonly been used over past decades. Just take a pencil and hold it firmly against the sidewall of the screen to see what kind of a “stroke pattern” it creates when the machine is operating. A pattern that’s even from side to side indicates that the angle of the stroke is also even from side to side.
Check Spring Lengths
Even if a screen seems to be running properly, it’s always best to measure the length of the springs on each side of the screen. On bigger screens, a 1/8-inch difference between the two isn’t a concern, but when you get beyond a 1/4-inch difference, it’s time to level up the machine.
Spring length does not need to be exactly the same from the feed end to the discharge end, as one end of the machine is usually a little heavier – but when the spring lengths vary from side to side – that’s an issue.
A ¼-inch difference side to side may not sound like much, but if the opposing corner on the other end of the screen measures the same ¼-inch difference, this indicates a ½-inch twist in the support structure – which is a huge problem. Always check for diagonal differences.
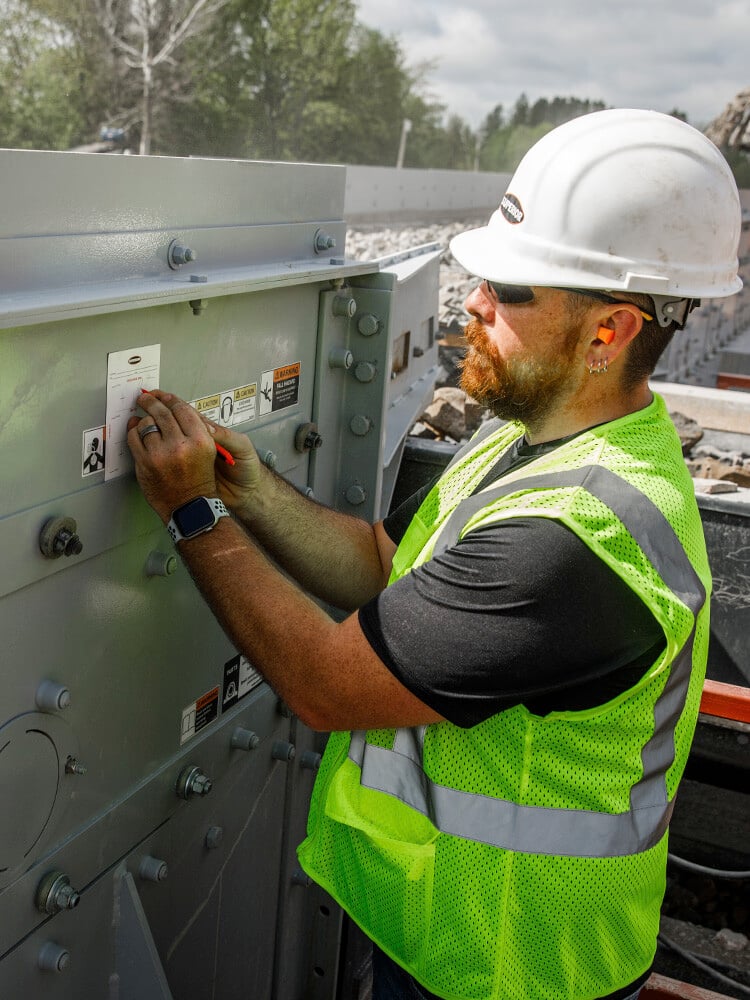
Listen to the Machine
During operation, do you hear banging, clanging, or hammering noises – all obvious signs of machine distress. Smells are important too. Do you smell hot oil or rubber? For example, the smell of hot rubber may indicate that the belts are slipping.
Also, listen to other crew members and operators. How do each of them think the machine is operating? Is it doing the job on each shift? Has anything in its operation changed recently? Having additional pairs of eyes and ears is always a good idea.
Ongoing Operation
When you think you’ve seen enough, look again – perhaps, at the product stockpiles. If you’re seeing an abundance of oversized material, there might be a hole in the screen media.
During shutdown, take a look at the wear patterns on the side walls of the machine. Are they similar on each side? Does it look like there’s been an even material depth and flow running down both sides of the machine? Also, look for material buildup on the feed or discharge end that could be adding more weight to one part of the screen over another.
No matter where you look, there’s always something more to see, learn, and improve. When combined with solid scheduled maintenance practices, ongoing observation leads to optimum processing efficiency.
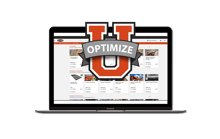
OptimizeU - Strategic Learning
Pursue greater production with comprehensive online courses in crushing, screening, conveying, and washing. Check out the premiere training resource in the construction aggregates industry.
Related Content
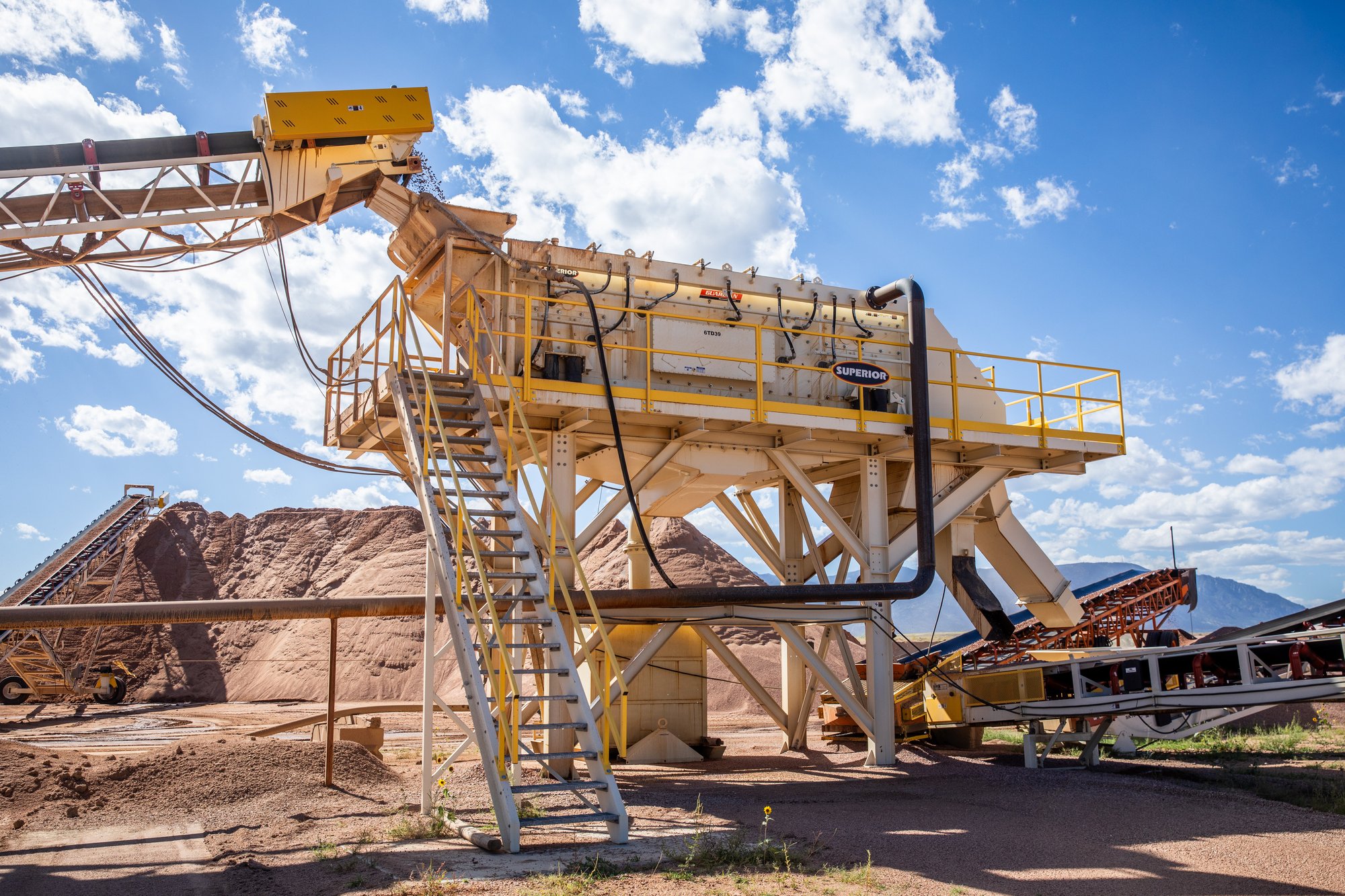
Clean & Efficient: Schmidt Construction's Fusion® Wash Plant Delivers Quality Sand
_5.jpg?width=2000&name=Desert%20Aggregates%20-%20Pheonix%2c%20AZ%20(2019-12)_5.jpg)
Faster Sand Sales : Desert Aggregates’ Success with Modular Sand Plant
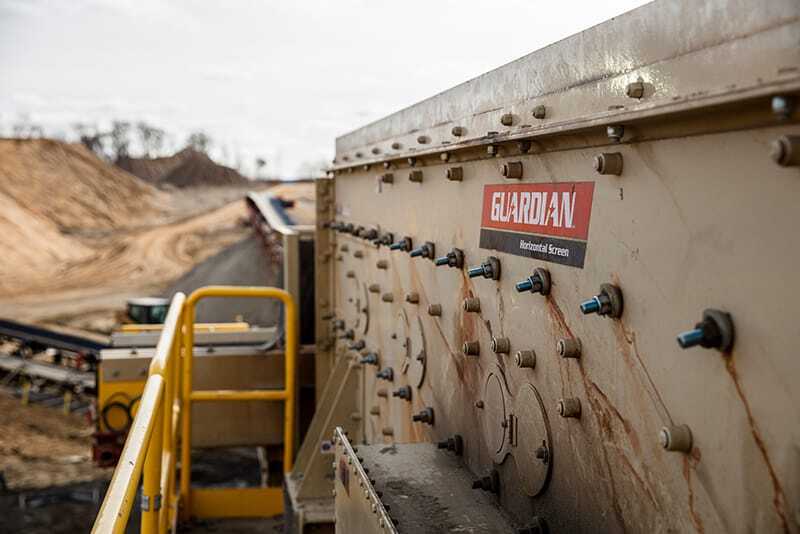
Aftermarket Support Seals the Deal for Anderson Brothers’ Screen Purchase
Talk to an Expert
Need more information? We'll get you in contact with a product expert in your area.