Preventing Premature Wear of Screw Shoes
Learn how the right screw washer shoe maintenance and material choice can save years of downtime and costly repairs, with insights from Superior's John Bennington.
PUBLISHED: JANUARY 2025
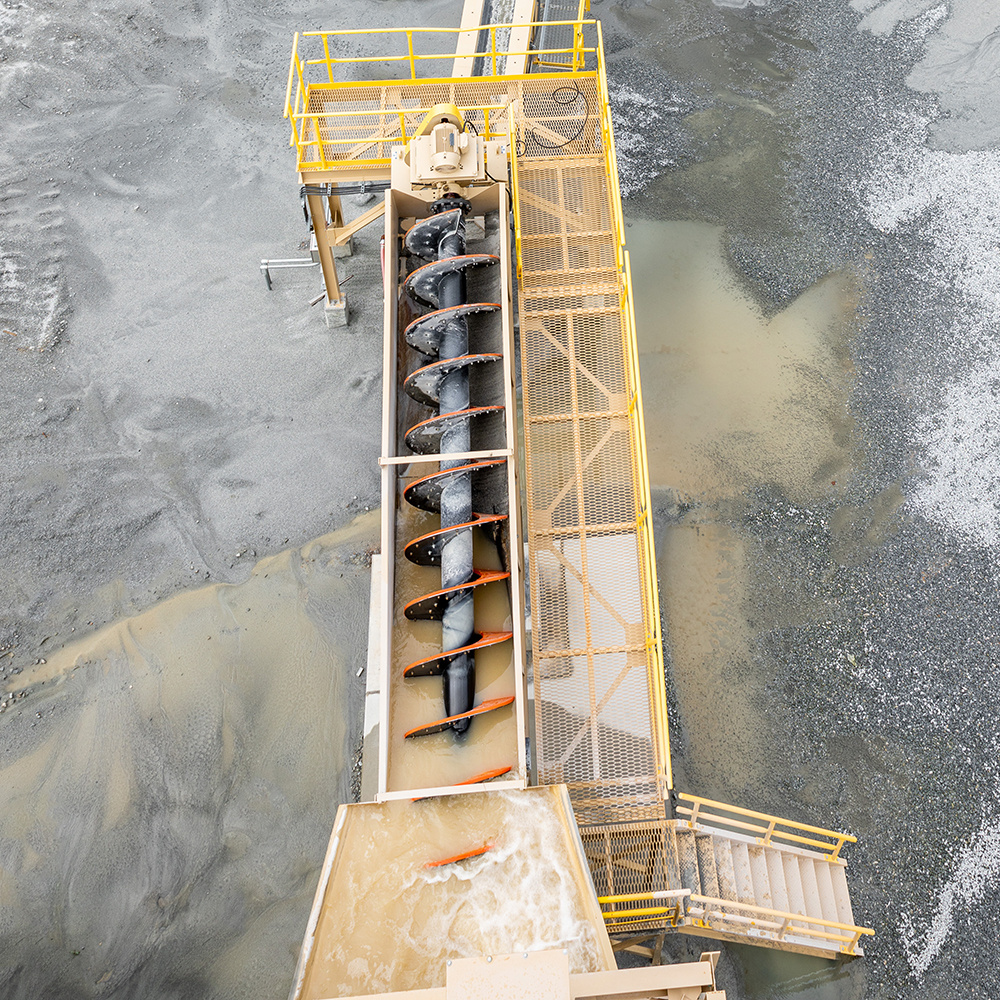
Understanding Wear Patterns
“In a normal sand screw application, you can expect the middle third of a shaft's wear shoes, around the tub's water line, to wear out in about three or four years,” says John Bennington, product champion of washing. “The following year, the shoes at the tub's discharge should wear out, followed by the ones at the feed end, typically under the water, after that."
After three or four years, replacing one-third of the shoes annually is the most cost-effective maintenance approach, but many operators overlook this simple routine in an effort to further streamline maintenance, often to their detriment.
Wear shoes, shown here as orange urethane, protect screw flights from abrasion and wear during washing operations.
The Consequences of Untimely Maintenance
“What ends up happening is that the steel welded to the shaft has to be cut off because it gets worn,” Bennington says. “You lose production in the sense that it takes longer to do the repair maintenance.”
Instead of a short shutdown to replace a full set of shoes, operators find themselves out of commission for a couple of days because flights must be cut off and replaced with new ones.
One indicator of the path most operators follow with shoe maintenance is the orders Superior receives.
“A lot of times, we’ll get orders from customers for a set of shoes for an entire shaft,” Bennington says. “What that tells me is that at least one-third of those shoes are being replaced two years later than they should be.”
Selecting the Right Shoes for the Job
Utilizing the wrong shoes for the application at hand continues to plague operators, as well. Shoes are commonly made of materials like A532 cast iron (Ni-Hard), rubber and urethane, with each offering advantages in distinct applications.
- Ni-Hard: Best for crushed aggregates, high-silica feed, glass, or metals.
- Rubber: Excels in natural aggregates, crushed limestone, and frac sand.
- Urethane: Cost-effective for natural materials, but less durable in sharp material.
“Ni-Hard is kind of the straight line,” Bennington says. “No matter what you feed it, it wears at a certain rate per ton, whereas rubber wears slower in natural material and faster in sharp material.”
So, pay attention to the type of shoes fitted to flights – whether on a screw washer that’s brand new or otherwise.
“We had a customer in a granite quarry in the Southeast who bought a unit out of stock that was already fitted with urethane shoes,” Bennington says. “The shoes lasted four or five months, which was largely due to how sharp the material was.”
FOR MORE INFORMATION: CONTACT JOHN BENNINGTON
(515) 777-4706
john.bennington@superior-ind.com
Other Content This Month
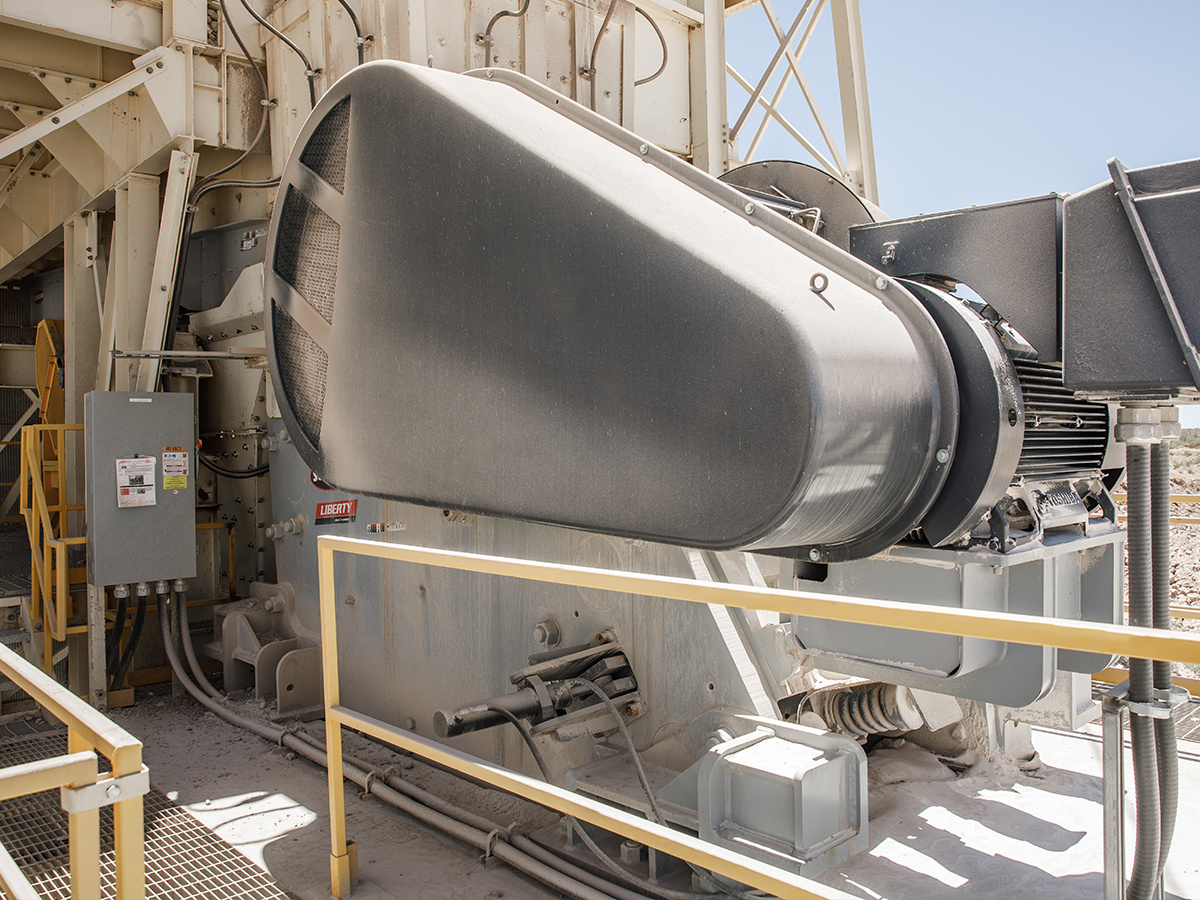
Proven Power: High Capacity Jaw Crushers
Jeff Gray, Superior's director of sales, reflects on the growth of the jaws and explains how Superior maneuvered into a more competitive position in recent years.
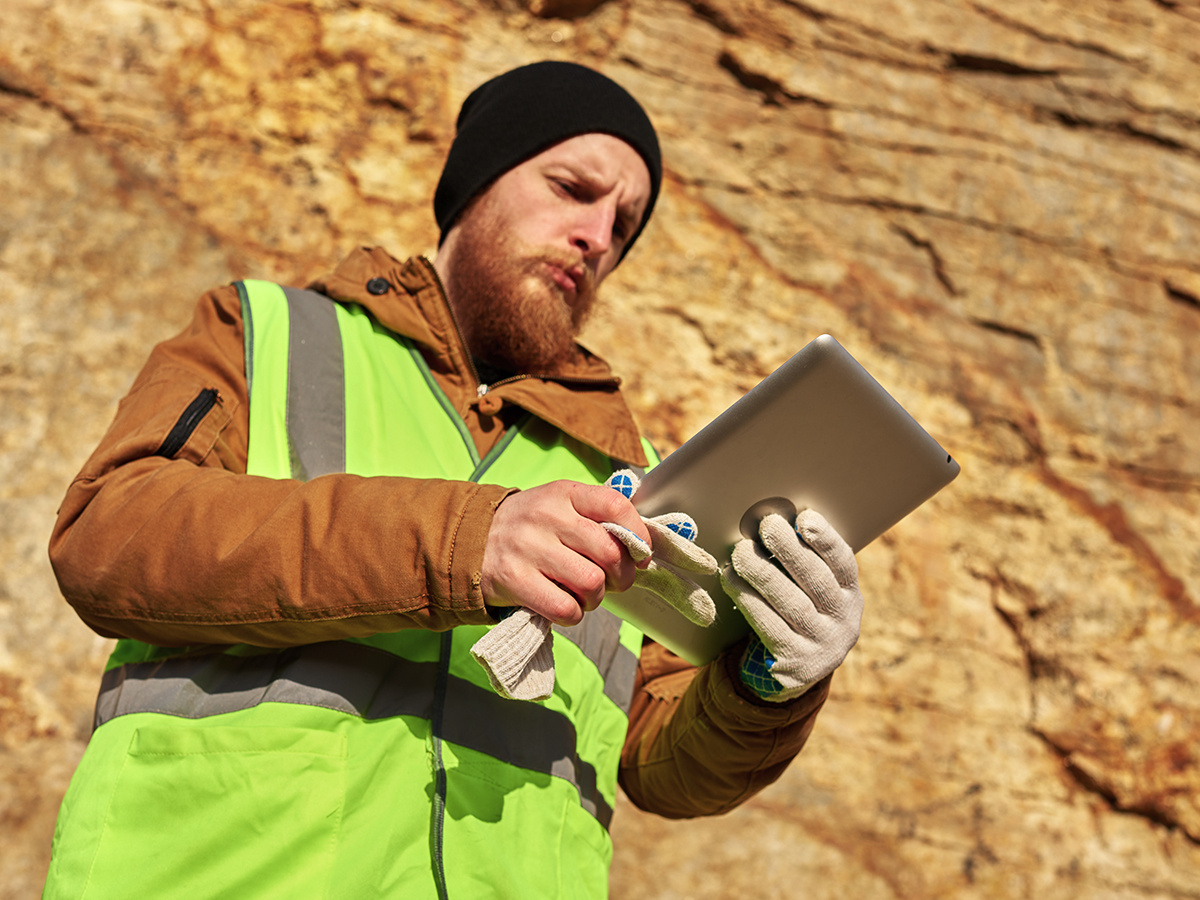
OptimizeU: Empowering the Future of Learning
OU is our new, on-demand learning platform with courses to expand your product knowledge, enhance technical skills, and master operational best practices.
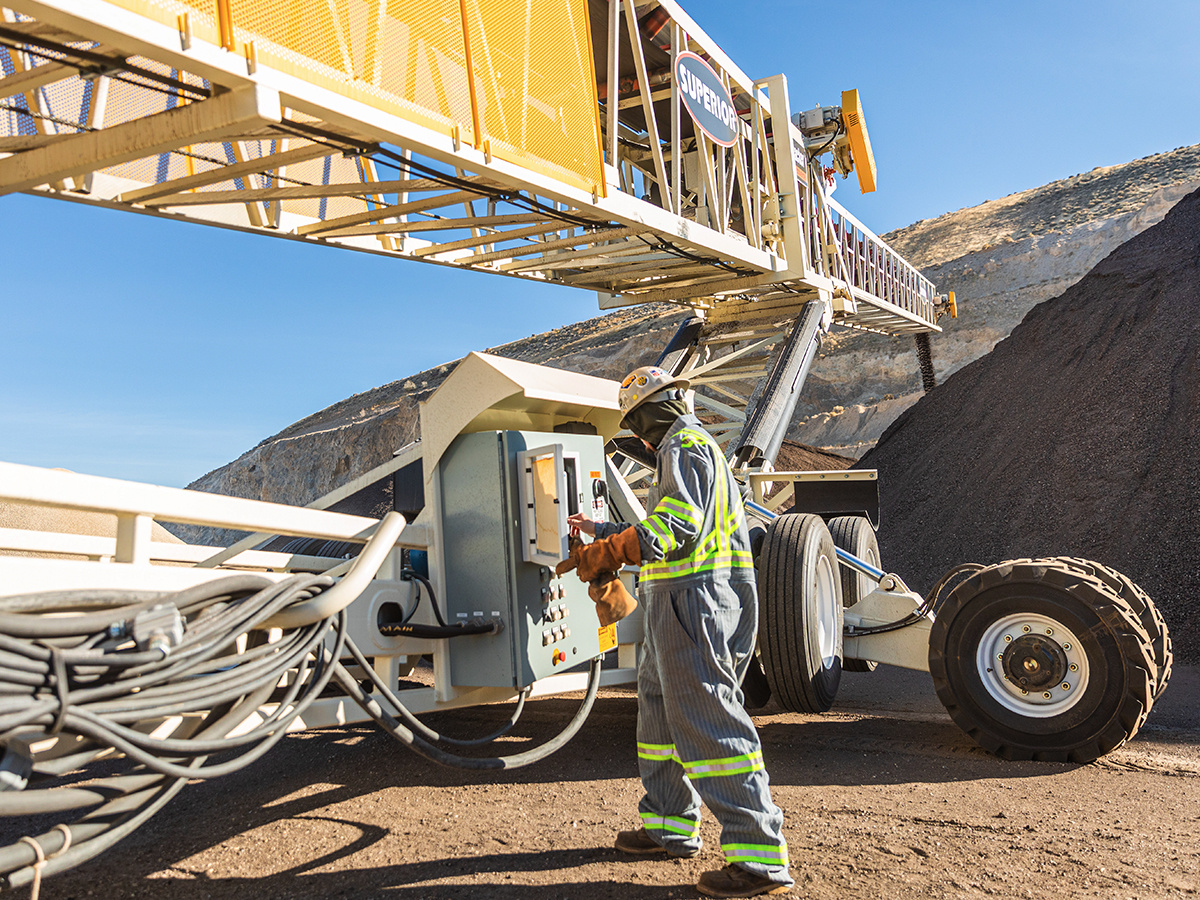
Major Update to TeleStacker® Conveyor Automation
Learn how the latest PilePro™ Automation update brings smarter controls, web-based access, and enhanced performance to the TeleStacker® Conveyor.