Momentum Builds for Larger Liberty® Jaw Crushers
Jeff Gray, Superior's director of sales, reflects on the growth of the jaws and explains how Superior maneuvered into a more competitive position in recent years.
PUBLISHED: JANUARY 2025
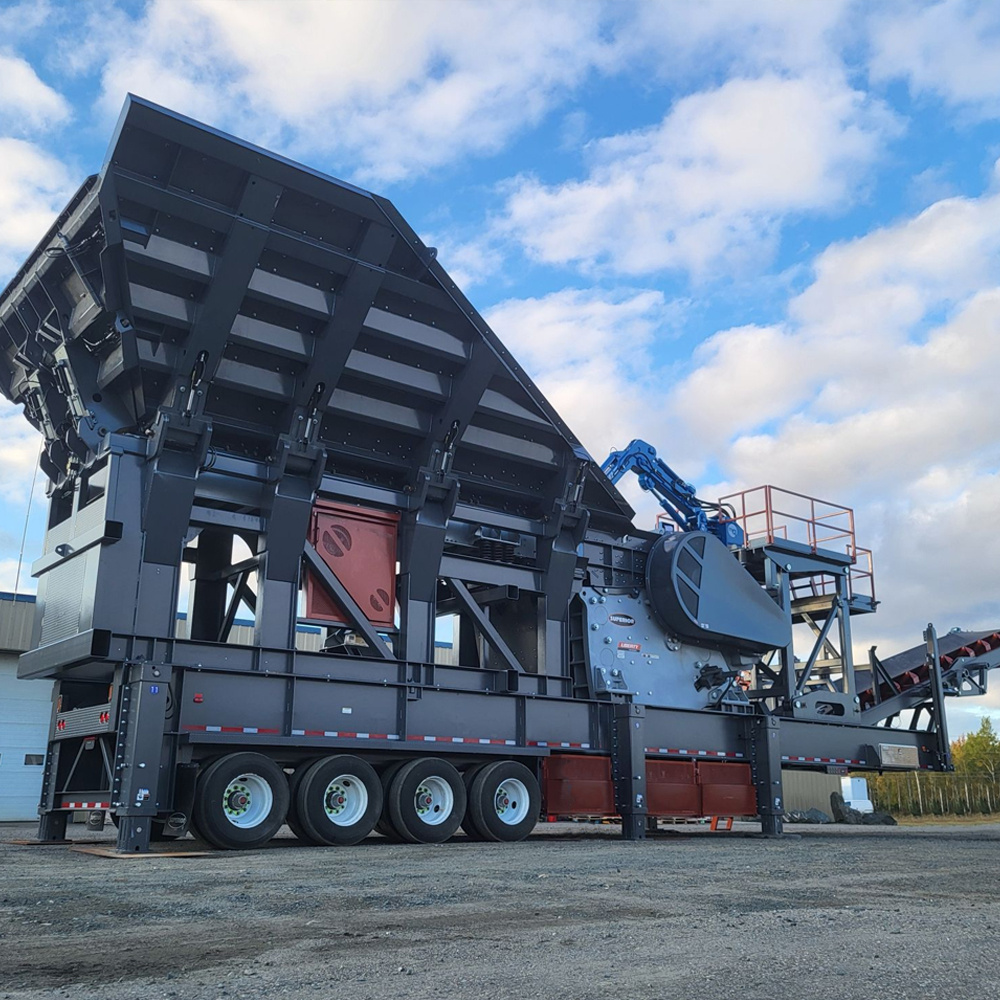
Product development isn’t over when an item is added to a price book or made available on a website. It continues in the field, as dealers and end users provide feedback to make the best products possible.
Customer Feedback Shapes Design
This approach has been especially valuable for Superior’s Liberty Jaw Crushers, which were introduced in 2016. The customer input Superior received about its earliest models was particularly valuable, paving paths for us to expand these primary crushers into the 11 models that make up the line today.
“The most popular sizes, typically the 3042’s and 3055’s, are those that cross over and can be mounted on either wheeled chassis or used in stationary applications,” says Jeff Gray. “That’s where we really got into the market and got good, quick feedback in a lot of applications.”
Ultimately, Superior reflected on the feedback from customers and applied that knowledge as it developed larger sizes.
“We heard about the good and the bad – maybe a component didn’t have the longevity expected or a desired feature was needed – so we tweaked those before we got too deep into larger models,” Gray says.
A Competitive Edge Building
The newest addition to the Liberty Jaw portfolio is a 5165, which fits between the 4655 and 6080, and one Superior has committed to building and stocking for dealers.
“That’s a size where you really must have a résumé and people need to have trust in our design,” Gray says. “If you were to put that into a primary stationary plant that’s running 1,000 to 1,200 tons per hour, it would take two or three portable jaw plants to make up for it if it goes down.”
From Gray’s view, Superior’s 5165 is a competitive offering to a pair of prominent models in its size category: Telsmith’s 5060 Iron Giant and Lippmann’s 5062. He believes Superior’s model has a leg up on rivals in total cost of ownership.
“I think we’re very competitive on the upfront purchase price, but the cost of ownership is where you start to add in maintenance costs outside of wear cost,” Gray says. “It’s maintenance of bearings, adjusting componentry and hydraulics where the cost of ownership really factors in.”
While some jaw crusher manufacturers have added new features to their offerings in recent years, Gray stresses that many of these require their own maintenance that can slow operators down in the long run.
Those little features have hydraulics, electrohydraulics and controls.
“Over time, those features need maintenance," he says. "Does an operation have the skilled people to do that, or do they need to wait for a dealer or manufacturer to answer questions and concerns?”
At a greenfield installation in Arizona, this 4655 jaw is capable of producing up to 1,000 tons per hour.
Easy-to-Maintain Design Sets Liberty Jaws Apart
Superior’s approach with Liberty Jaws, on the other hand, is to provide machines that can easily be maintained over 20 to 30-plus years. Gray points to the pitman area – specifically the bearing housing – as a design approach that adds to the Liberty Jaw’s longevity.
“Our Liberty Jaw Crushers use what I call a ‘cartridge-style’ bearing housing,” Gray explains. “This housing is bolted to the side plates of the mainframe, making it much easier to maintain over the crusher’s lifecycle, especially when the bearings eventually need replacement.”
Gray elaborates that this design allows the entire pitman assembly, including the bearing housings, to be unbolted and removed for servicing. “The assembly can be sent out for bearing replacement while the rest of the machine remains in place,” he says.
This process is much simpler compared to some competing crushers.
“On other machines, if bearing components become worn or damaged, it often requires removing the entire mainframe,” Gray says. “That’s because the bottom half of the housing is welded directly into the mainframe. In such cases, the whole machine needs to be disassembled, taken off its structure, and sent to a facility for repairs—a costly and time-consuming process.”
With the Liberty Jaw’s bolt-on housing design, customers have a choice: they can either rebuild the housing or replace it entirely. “Either way, the mainframe stays put, and you’re working with a smaller, more manageable component,” Gray adds.
Superior's new standalone crusher manufacturing facility in Minnesota went online in November.
Building Capacity for Future Demands
Another factor making Superior more competitive is its new manufacturing facility in Minnesota, which produces jaw, cone and impact crushers. It increases Superior’s crusher manufacturing capacity in Minnesota by more than 50 percent and provides an assortment of other benefits, as well.
“We can be testing multiple crusher types simultaneously in the building,” Gray says. “We also have the ability to pull in a portable chassis and mount crushers right next to the crusher test stand.”
The new space is proving beneficial from a crusher component standpoint, too.
“Small and medium size components used on various crushers are all warehoused adjacent to the assembly area” Gray says. “We store many more parts inside today than we were able to just last year.”
Other Content This Month
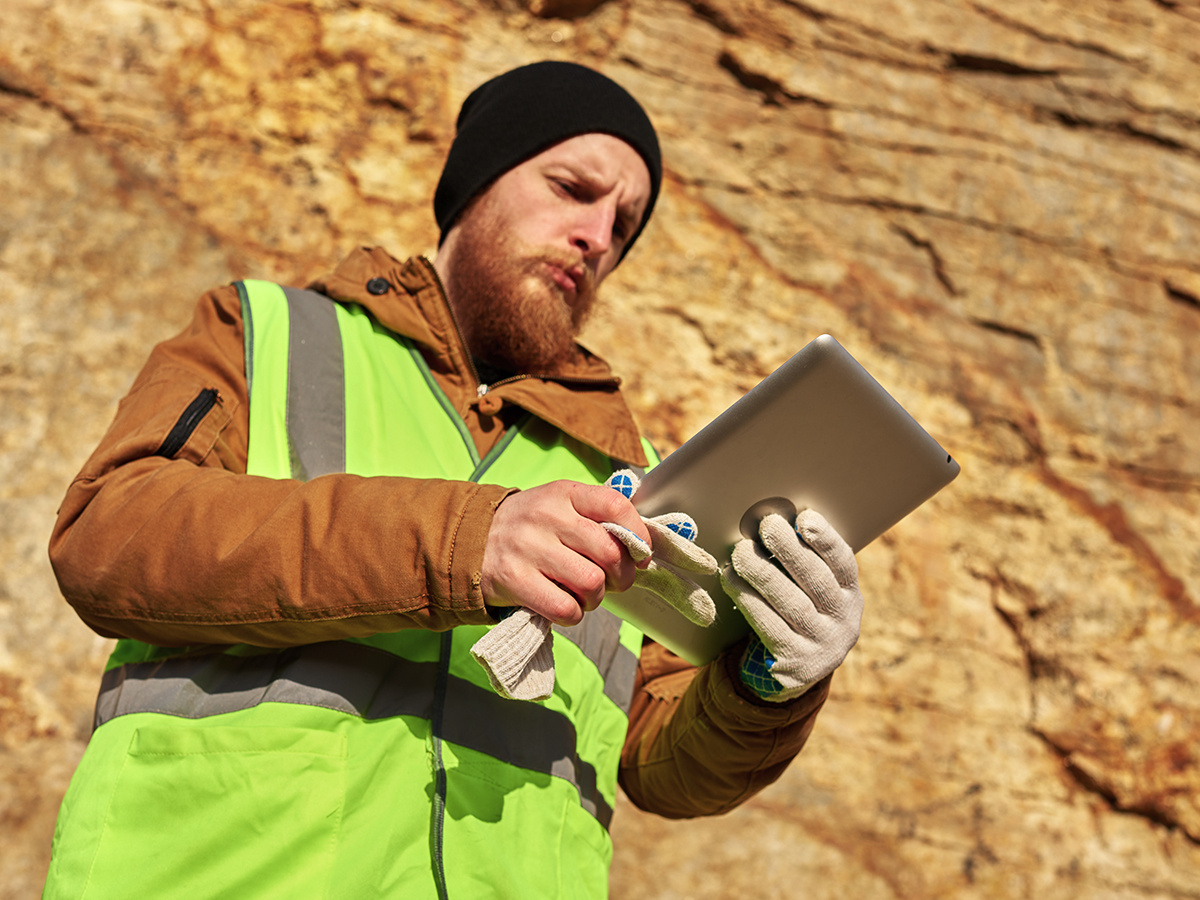
OptimizeU: Empowering the Future of Learning
OU is our new, on-demand learning platform with courses to expand your product knowledge, enhance technical skills, and master operational best practices.
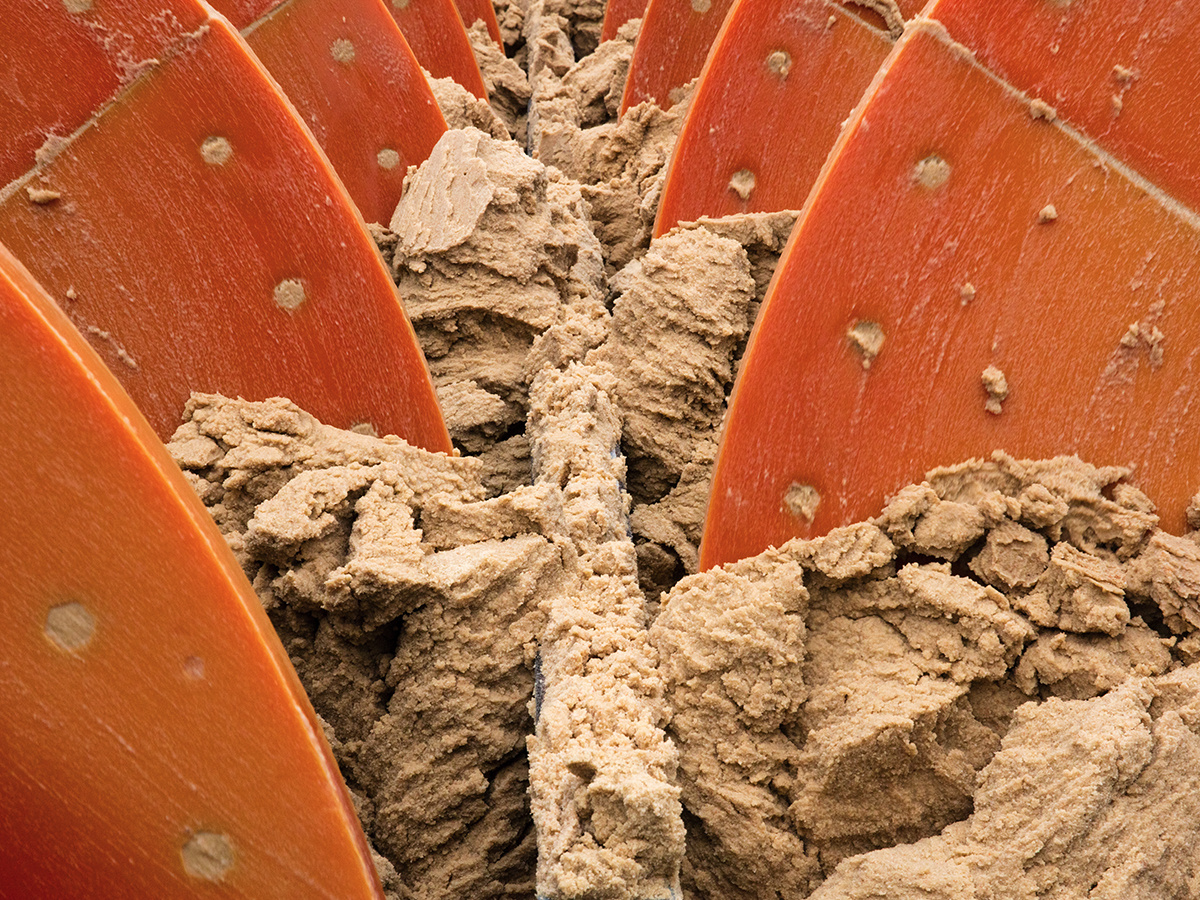
Preventing Premature Wear of Screw Shoes
Learn how the right screw washer shoe maintenance and material choice can save years of downtime and costly repairs, with insights from Superior's John Bennington.
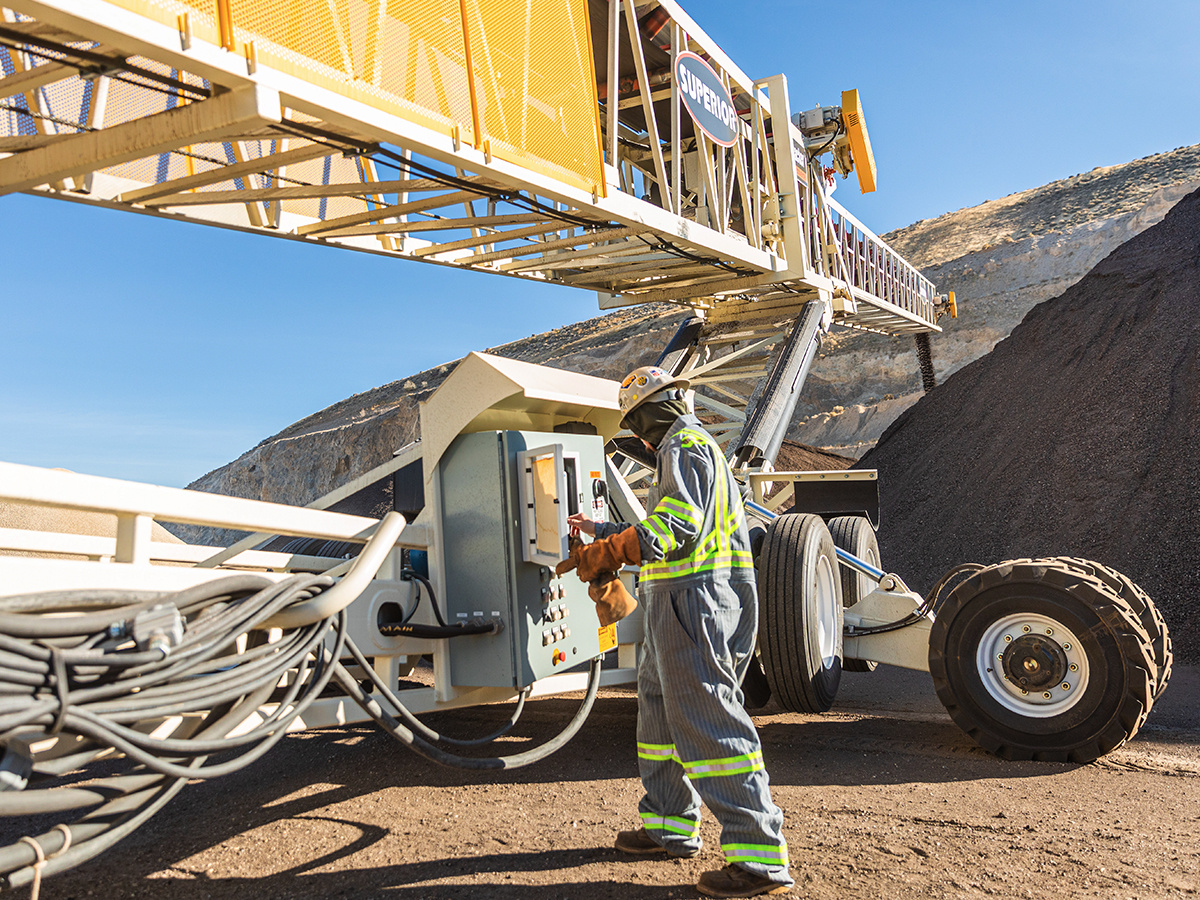
Major Update to TeleStacker® Conveyor Automation
Learn how the latest PilePro™ Automation update brings smarter controls, web-based access, and enhanced performance to the TeleStacker® Conveyor.