Get Double Bearing Life With a Smarter Screen Setup
Speed and stroke adjustments may seem small, but these overlooked details can mean the difference between frequent failures and lasting performance.
PUBLISHED: MAY 2025
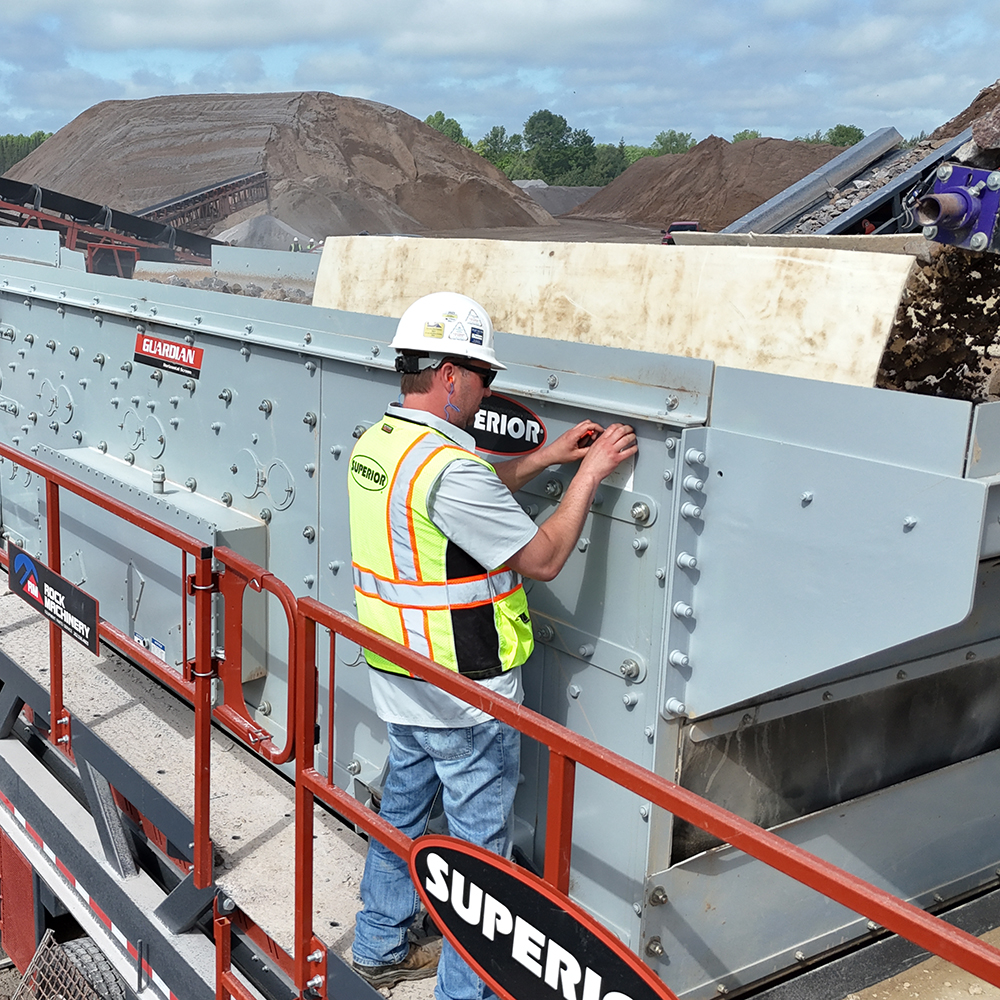
Maximizing screen performance requires getting off to a good start, and attention to detail on day one means more dollars made down the road.
When setting up a new screening circuit, there is much to consider, but first the vibrating screen’s operational settings must be adjusted and maintained to suit the specific application.
“Speed and stroke are two of the major factors to fine tune when setting up a screen,” says Ed Sauser, vibratory product manager at Superior.
He shares the following tips to achieve top screen productivity right from the start.
Dialing In Settings
Speed (RPM) and stroke (amplitude) work together in standard formulas that offer optimum screening efficiency in a specific application. In very general terms, finer screening requires less stroke and higher speed, while coarse separation needs increased stroke and lower speed.
Proper speed for a given application creates a material travel rate and a bed depth that allows finer materials to pass through. In combination with proper speed, the screen’s stroke must be set at a level that’s strong enough to prevent plugging without risking damage to any of the machine's components.
Most manufacturers use the Vibrating Screen Manufacturers Association (VSMA) formula to determine optimum screen capacity, which is the calculated capacity per square foot of screen area in tons per hour. Additionally, the VSMA handbook offers a detailed, illustrated resource for step-by-step screen setup.
A quick manual check with a stroke card can reveal whether your vibrating screen is running at optimal amplitude and motion.
Caution: Speed Kills
Often overlooked is the potential downside of higher speeds. Sauser cautions that “speed kills” as it can compromise the life of the machine. With vibratory equipment, bearing life is affected exponentially by speed.
Producers may not realize that if they reduce speed by 10% — and still meet specifications — they can potentially double bearing life on their vibratory equipment. Alternatively, if speed is increased by 10%, bearing life may be cut in half.
Don't run vibratory equipment any faster than needed. Obviously, if material is blinding or pegging, more speed is required. However, if you can do the job with less speed, it’s better for wear life.
Attention to Detail
Feed size, particle shape, moisture levels, media selection, size of openings, desired cut, tons per hour, and more — each little detail of the application affects optimum screen setup and performance.
Sauser emphasizes that producers often expect too much from a single screen or deck. For efficient screening, material must be evenly distributed, and the depth kept in check so smaller particles can reach the screen surface quickly. Ideally, material depth at the discharge end should be 4 to 6 times the media opening. For instance, with a 1/4" opening, depth should be no more than 1-1/4".
Define your application in detail and make sure the settings you choose support maximum screening efficiency and machine life.
Did Our New Magazine Land in Your Mailbox?
The first printed edition of our dealer-only magazine, THE ORANGE EDGE, has arrived in most of your mailboxes, featuring all-new content just for Superior’s dealer network.
Other Content This Month
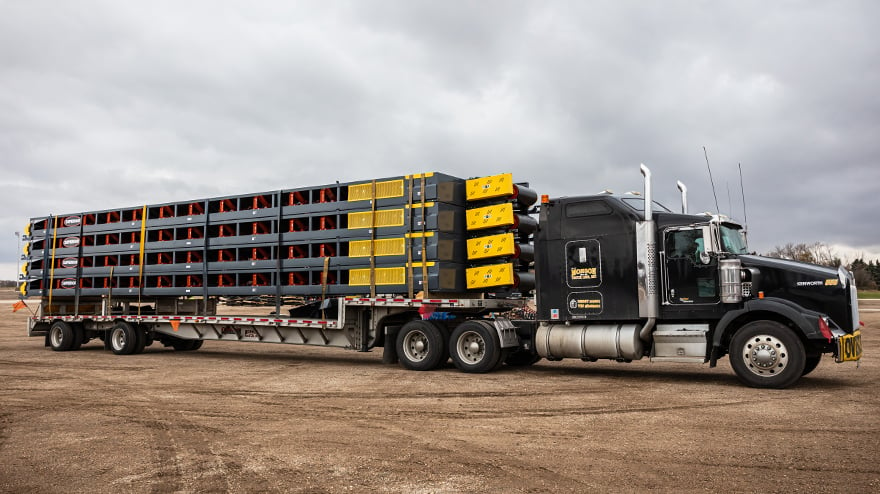
Dealer-Driven Conveyor Improvements Worth Knowing
From bolt-in skirting and anti-buildup take-up covers to new pricing on self-contained stackers, Superior is engineering solutions with dealer input.
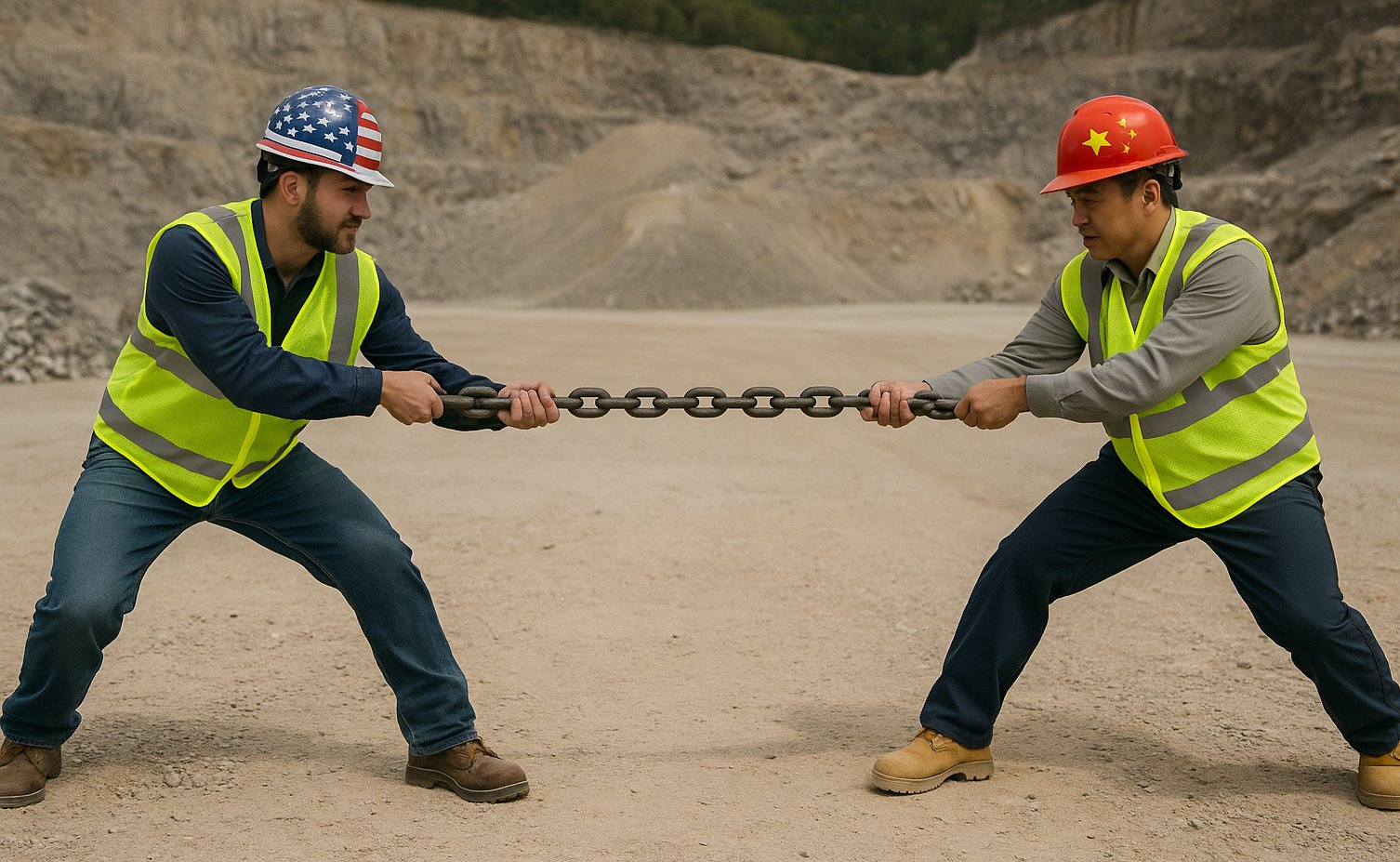
Making Sense of Shifting Tariff Policies for Equipment Dealers
With tariffs changing weekly, this update explains how Superior is staying ahead and helping you do the same during conversations with customers.
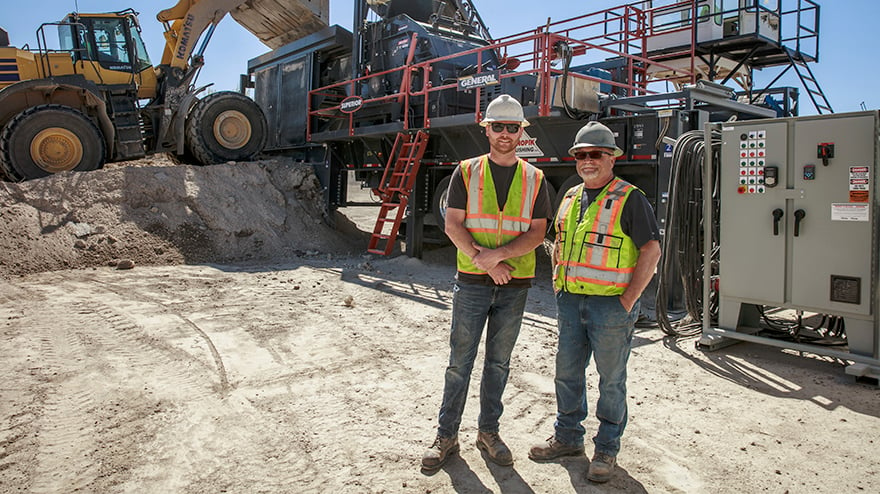
While Others Offshore, We're Building Home-Field Advantage
With strategic hiring, new facilities, and more capacity, Superior is laying the groundwork to help dealers win in a changing portable plant market.