Dust Compliance is Coming: Are Your Customers Ready?
With MSHA’s new silica rule looming, now’s the time to turn passive dust control into a proactive sales strategy. Superior’s off-the-shelf solutions save customers money and prep them for compliance.
PUBLISHED: JUNE 2025
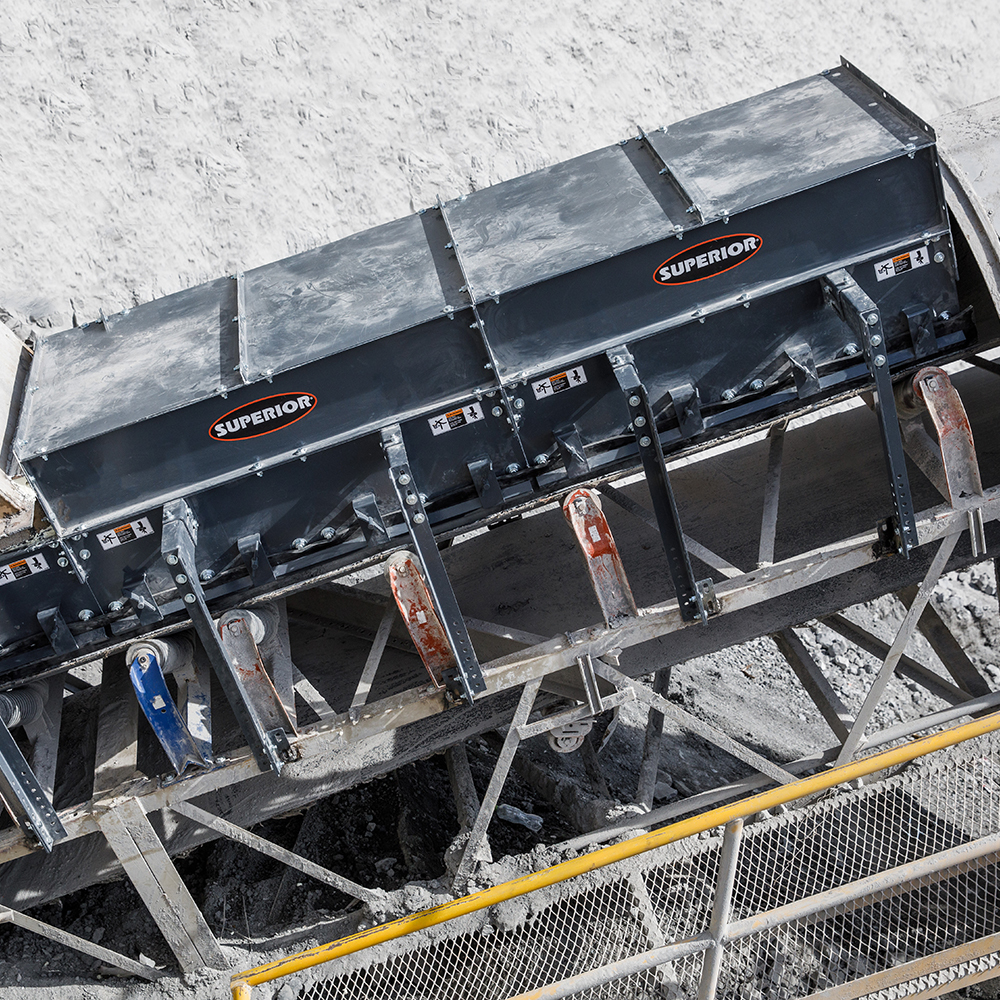
Dust management doesn’t usually top the list of attention-grabbing topics, so it’s not the first thing equipment dealers aim to sell. Yet, dust controls have a place in practically every dry crushing and screening application.
With enforcement coming, now is the time for dealers to start the conversation. MSHA’s updated silica rule goes into effect next April, capping the amount of airborne dust quarry workers can be exposed to. Sites that ignore it could be cited for things like poor containment at transfer points or lack of dust control near crushers.
Coincidentally, Superior has developed a package of conveyor solutions over the last several years with the intent of mitigating dust. Things like skirting, clamping and wear liners specifically designed for conveyor transfer points.
These solutions aren’t cutting-edge inventions, but they’re practical, off-the-shelf, and easy-to-install components that fit most environments.
“I like to compare it to buying a common set of idlers instead of designing some custom configuration,” Gibson explains. “These are standardized solutions that eliminate the need for custom engineering."
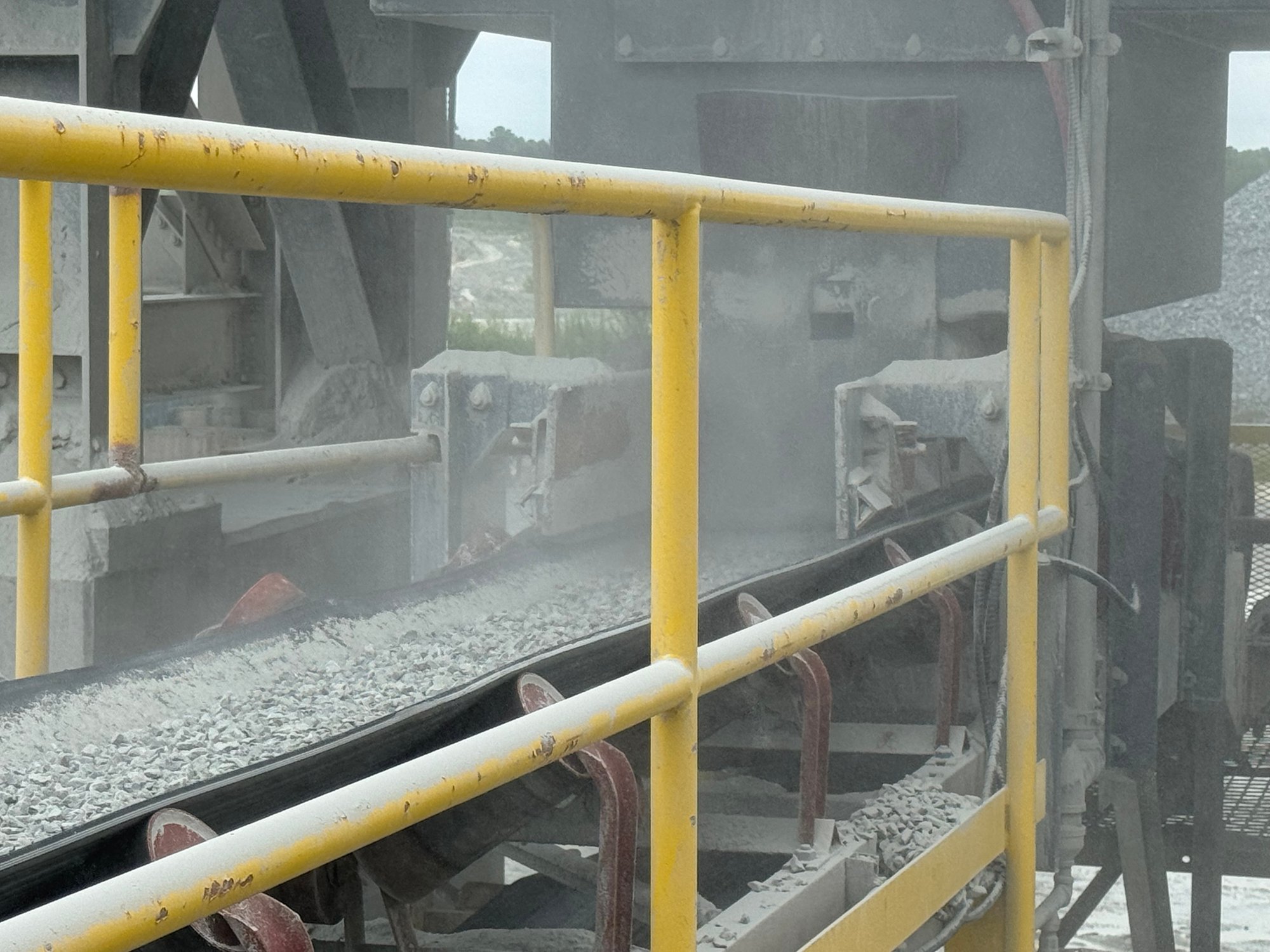
BEFORE: Dust clouds escape the load zone under a cone crusher creating unsafe and unhealthy conditions.
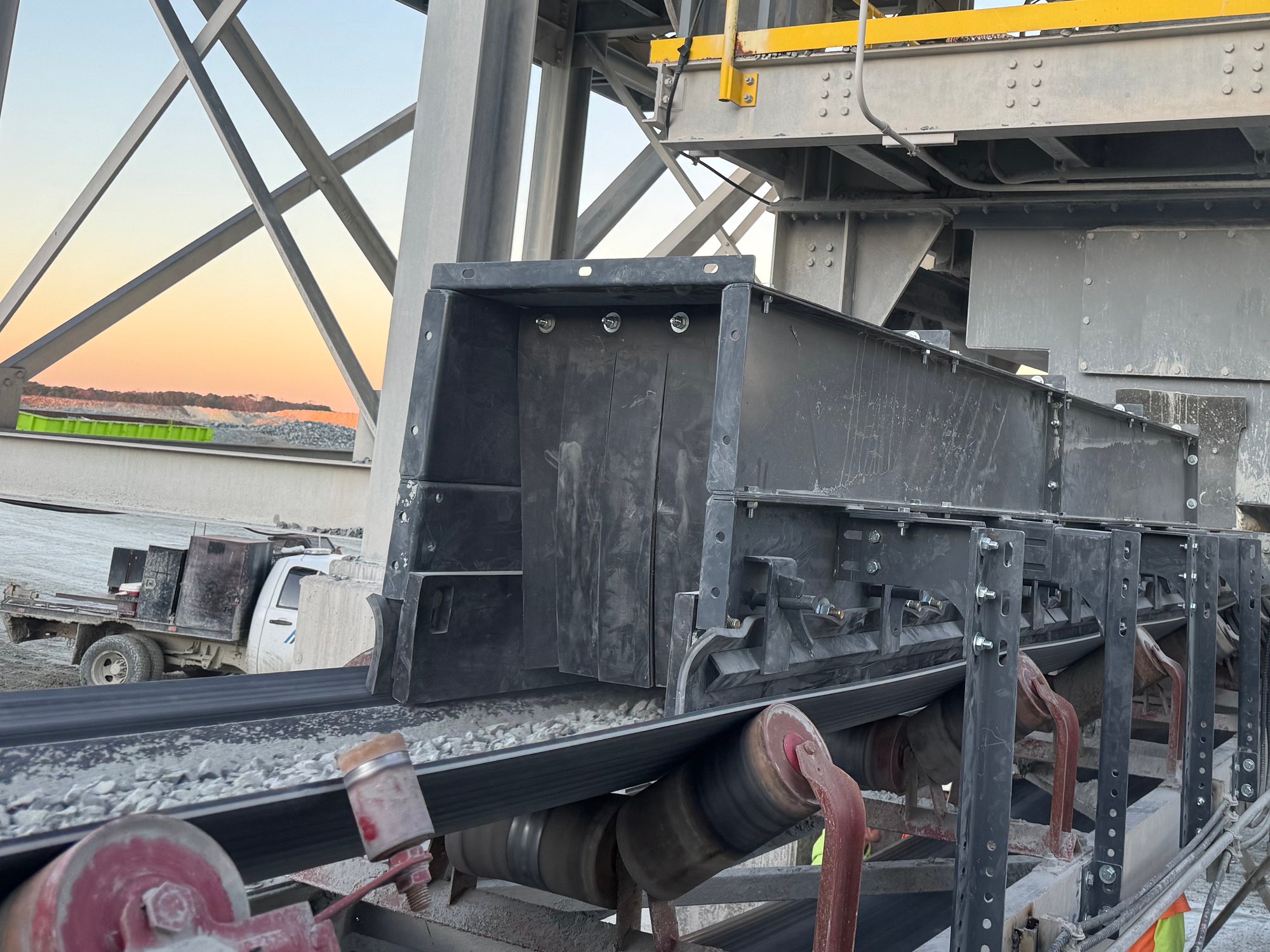
AFTER: With Superior’s Skirting System installed, dust is eliminated, improving air quality, safety, and regulatory compliance.
Look for the Signs
From Gibson’s perspective, almost every operation he visits is a contender for dust controls.
“Probably one-percent or less is doing a good job of controlling their dust today,” he says. “They really haven’t had to think about it before."
While equipment dealers may not directly pitch dust control solutions, Gibson recommends weaving the topic into existing conversations.
“When you visit a site, look for dust in the air during operation,” he says. “If they’re not running, look for fine dust that has settled throughout the plant.”
From there, dealers can pose a series of questions:
- How much time do you spend cleaning up the site of fine particles?
- Are you dealing with dust blowing onto trucks or nearby property?
- Do you anticipate making changes to meet the new dust exposure limits?
Dealers can then take the time to explain how dust damages critical moving parts.
“Airborne dust will find its way into tail pulleys, idler rolls, belt seals, and load zone components, accelerating wear across the system,” Gibson says.
Uncontrolled dust has also been known to contaminate finished materials as it settles on and into stockpiles.
MSHA’s silica rule limits exposure to the amount of dust that would fit on the tip of a pencil spread over an 8-hour shift.
Seal the Deal
A good dust seal takes the whole system of conveyor components working together, from skirting to belt support.
“If you see visible dust coming from belt-to-belt transfers, we can fix that problem with our conveyor skirting system and stilling box,” Gibson says.
In many cases, that's a good starting point, but truly mitigating the problem typically calls for additional measures.
“Installing skirting is a good step, but if the belt is sagging from poor load support, you’ll still see leaks,” Gibson says. “That’s why an impact system and strong belt support are also critical for effective containment."
Dust control extends beyond conveyors to critical crushing zones as well.
“We’ve got proven dust control setups for material coming off single and dual cone crusher configurations,” Gibson says. “And we have effective solutions for jaw crushers, too.”
A dust containment solution for impactors is next on the to-do list.
“We’re going to be testing a stilling box at an active VSI site,” Gibson says. “In the next six to eight months, we expect to have solid solutions for both HSIs and VSIs.”
The Future is Pre-Installed
Superior will soon make passive dust control solutions available as an option on its Fusion® Modular Platforms.
“Producers will be able to request built-in dust control when investing in these pre-engineered, plug-and-play processing plants,” Gibson says. “They'll be designed for fast setup, layout flexibility—and now—cleaner operation.”
Although Gibson figures only about one in 100 sites currently utilize passive dust control effectively, he expects adoption to increase as MSHA enforcement begins.
“It’s being pushed by the government as a regulation, but in reality, it’s a money-saving item for the end user in the long run,” he says. “If they’re not controlling dust, there will be component failure, cleanup issues, and environmental concerns."
"It's going to pay for itself relatively quickly," he concludes.
Other Content This Month
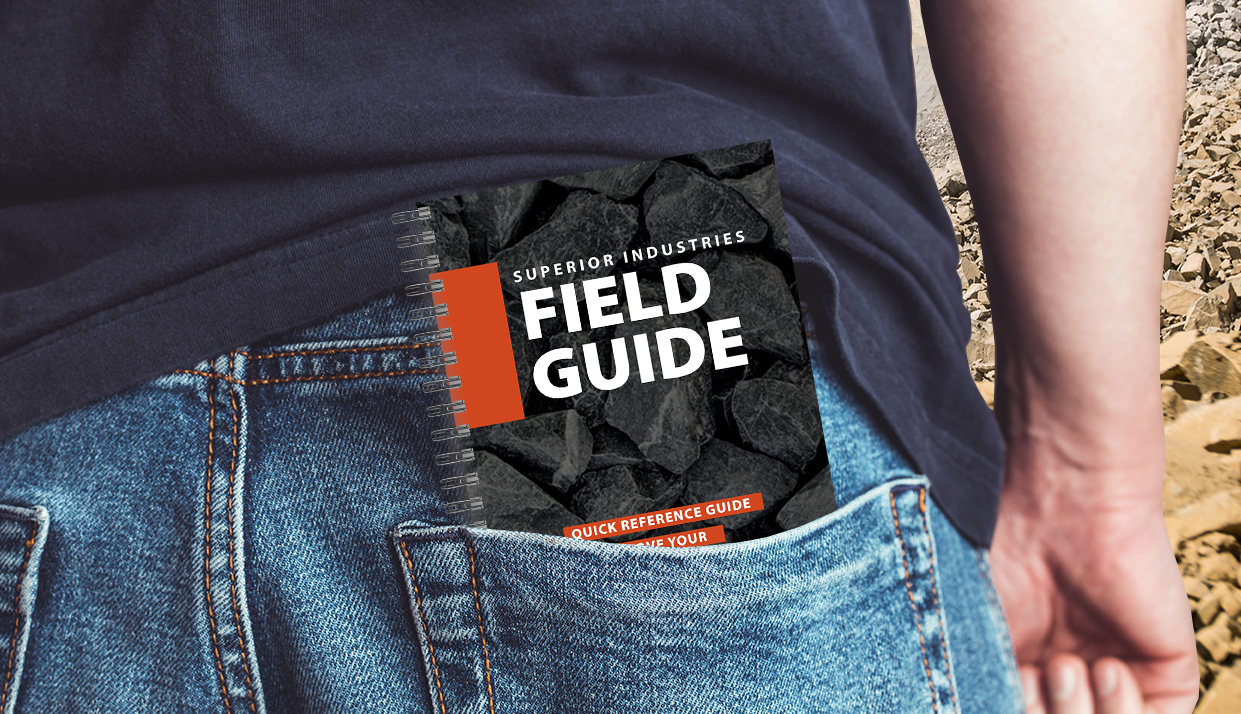
The Updated Field Guide Delivers Real-World Support
From updated specs to troubleshooting tips, this hands-on reference helps your team spec, service, and sell Superior equipment with confidence.
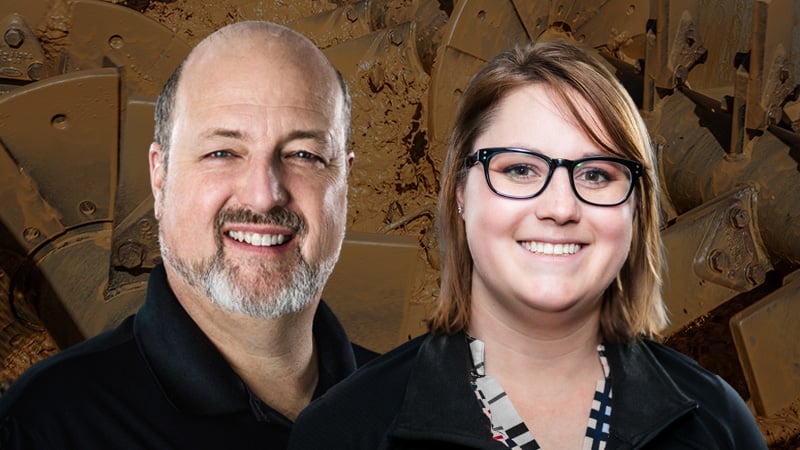
Washing School Recap: Five Hot Topics to Know
From man sand to water recovery and equipment overlap, here are topics that got the most attention at our recent Washing Equipment Dealer Sales School.
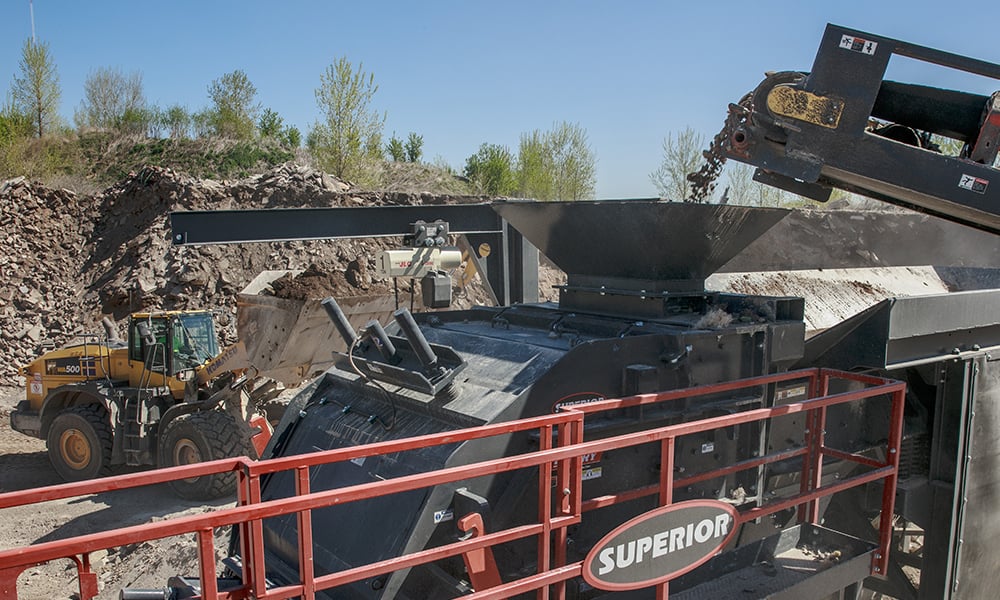
HSI Cheat Sheet: Match the Model to the Mission
Choosing the right horizontal shaft impactor isn’t one-size-fits-all. This breakdown helps dealers align machine performance with applications.