Tech Tip: Maximizing Cone Crusher Performance
Achieve Peak Performance in Quarrying & Mining
Every producer wants peak crushing performance, but not everyone knows how to achieve it. Getting there may require just a few tweaks or even a total rebuild. To remain at peak levels requires proactive maintenance practices combined with expert consultation and continuing education.
When operations truly maximize cone performance, the perennial paybacks include:
- Lower cost per ton
- Greater plant uptime
- Increased production capacities
- Generation of more highly saleable material
- Reduced maintenance and wear costs
"Maximum cone crushing performance requires a complete understanding of the application parameters, design limitations of the crushing machine, and the processing circuitry needed to support that machine,” says Jarrod “Hollywood” Adcock, crushing product manager for Superior Industries.
Seek Versatility & Value
The cone crusher is a versatile machine that can be used in all phases of material reduction – from the rock face to product finishing – but more often than not, its duties are targeted to secondary, tertiary, and quaternary aggregate and mining applications. A cone is a compression crusher that effectively crushes abrasive material, as well as a wide variety of stone from medium to very hard compressive strength. How can this very versatile machine deliver the most value while minimizing operating costs per ton?
From a bottom-line standpoint, Adcock says that maxing performance and cutting wear costs means “getting every stone through that cone crusher that we safely can – while preventing any machine damage – and still meeting or exceeding production goals.”
From the basics to the big picture, Adcock discusses the following solutions and strategies toward maximizing cone crusher performance.
Define All Parameters Upfront
Whether specifying a new machine or fine-tuning an exsisting crushing circuit, all key parameters must be defined upfront. "What is the true work that you're asking that crusher to do?" asks Adcock.
- Operations must provide data on proper feed gradation, desired output, tonnage, and material type.
- Knowing precise composition, compressive strength, and chemical properties of stone is a huge factor!
"Many operations try to do too much with one machine, pushing it beyond its design limitations; and causing excessive component stress and wear, and the potential of serious damage," says Adcock.
All crushers are designed for certain reduction ratio limitations. In most cases, cone crushers provide reduction ratios of 4-to-1 and up to 6-to-1 (meaning the ratio of the feed size to the crusher vs the size of the crusher discharge).
“The reduction ratio design limitations; and the rated capacity (tons per hour) of the cone crusher are the most important factors to consider when designing a crushing circuit – and determining how much that crusher can safely do,” he says.
With complete application data in hand, Adcock says that it’s important for operations to work closely with their crusher supplier to select the right crusher.
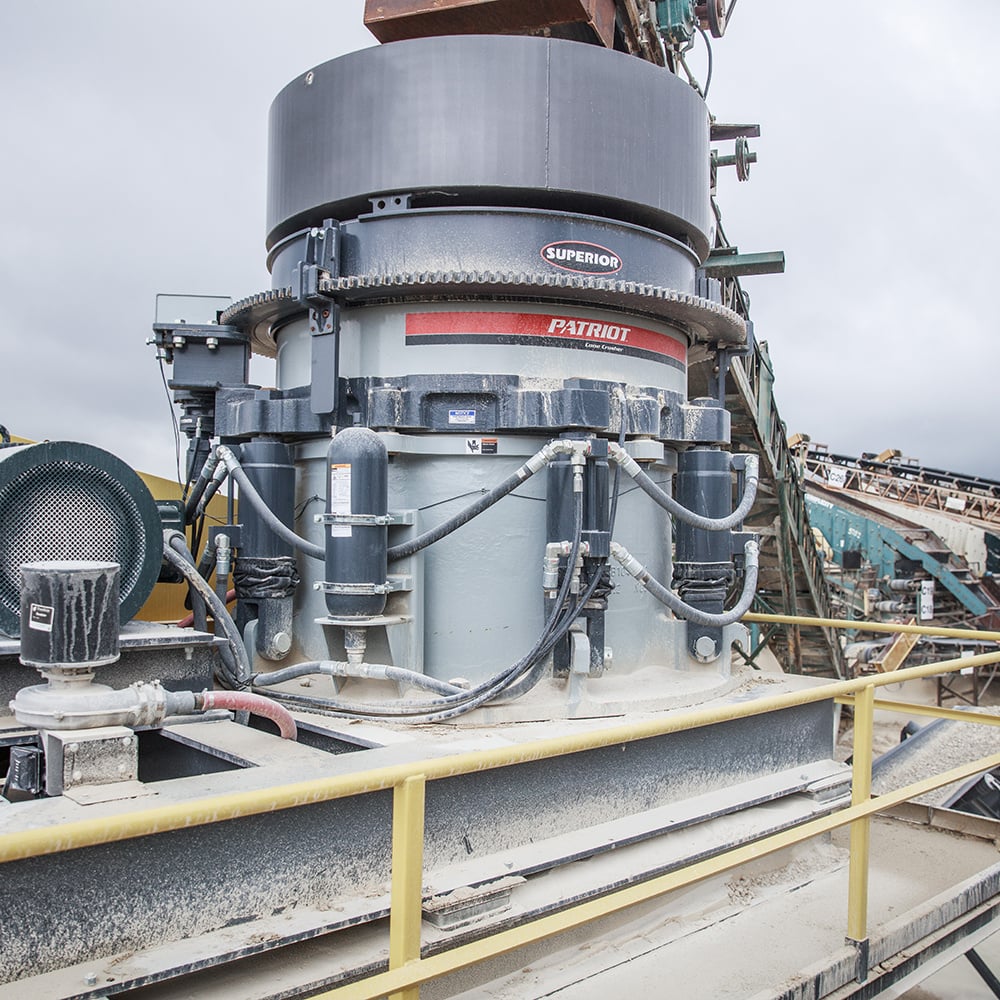
Key Considerations
- Crushing speed
- Chamber design
- Liner configurations
- Crusher settings
"There are myriad choices of machine configurations. Whether it's minimizing fines or maximizing fines; or trying to reate the highest yield of a particular product, there are chamber and liner configuations designed specifically to meet the desired product yield," says Adcock.
Design Proper Circuitry
For performance efficiencies, proper circuitry should be designed around the cone. Importantly, the circuit should be engineered to provide the cone with choke-fed material, or enough material to keep the crusher full.
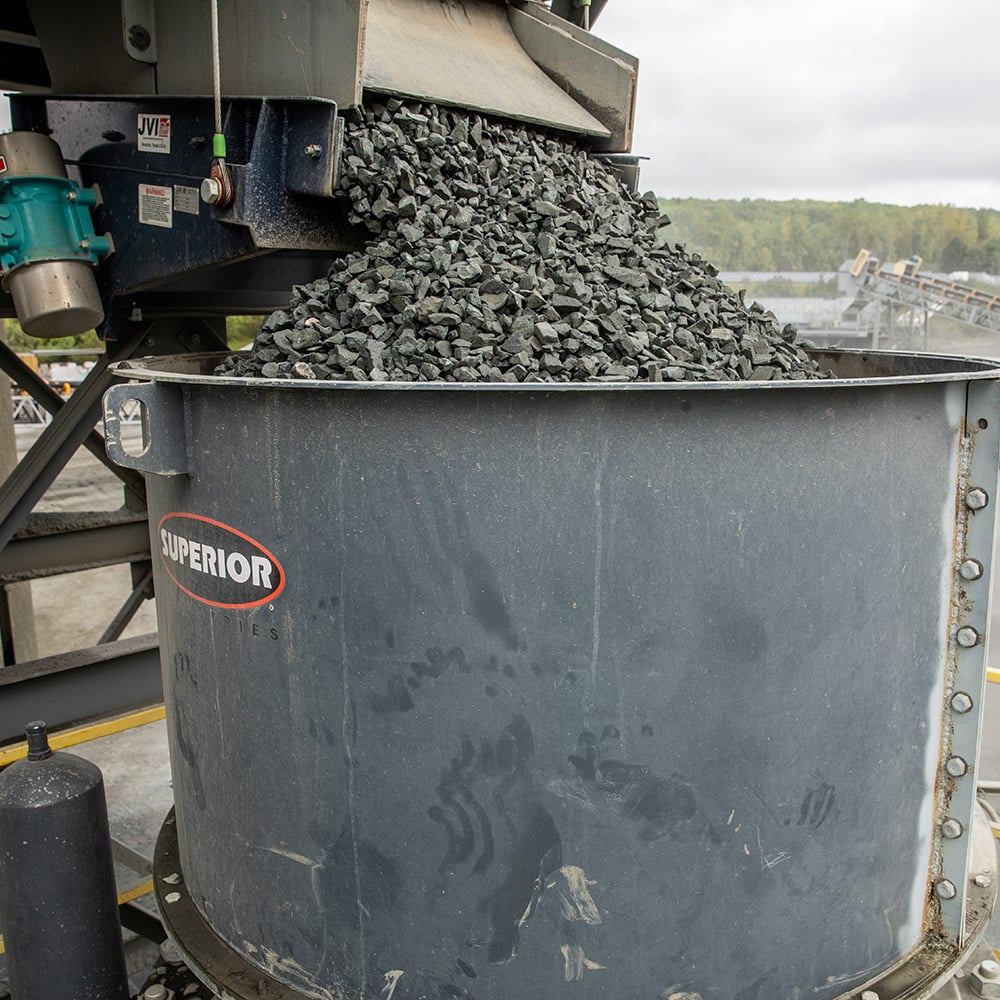
Having adequate screening capacity downstream of the crushing circuit is another key factor. In a closed-circuit setup, material that is not properly sized is recirculated back to the crusher for further reduction.
“It’s very common to see operations that have a bottleneck at the screening circuit. They do not have enough screening capacity, so properly crushed material is sent back to the cone. These unnecessary recirculating loads simply eat up more space and horsepower in the crusher while increasing wear,” says Adcock.
Tap Into Automation
“To significantly affect cone performance, automation doesn’t need to be over-thetop and super complicated, but rather quite simple and very easy to control,” says Adcock, adding that one of the biggest things that automation delivers is protecting the machine from damage by acting as a warning system that alerts operators to conditions such as bowl float, excessive amperage or temperatures, and lubrication or low-flow oil issues.
Adcock points to Superior’s Patriot® Cone (one of three unique cone models), which features a three-sensor “bowl float” or “ring bounce” monitoring system that alerts the operator if conditions are over exceeding the design limitations of the cone. He explains that the top and the bottom of the cone are basically held together by hydraulic cylinders.
When the crushing action on the cone exceeds the pressure that is holding those two pieces together, it causes bowl float or ring bounce, which is any movement at all (even slight) between the top and the bottom of the crusher. Undetected bowl float will eventually lead to component failures.
“When operating a cone, preventing bowl float is arguably the single most important thing you should ensure,” adds Adcock.
Most cone crushers are designed to open up due to tramp metal or an uncrushable situation. However, none are designed to operate with ring bounce.
“There should be zero ring bounce or bowl float under normal operating conditions. Without automation, it can be difficult to detect ring bounce at times. You can literally be standing on the machine, and you cannot detect even the slightest ring bounce – so having that automated warning system is an enormous advantage,” he says.
Adcock also encourages operations to tie an automated warning system into the designed amperage utilization of the machine.
“Our automation package works in conjunction with the drive motors and essentially reads the amp draw of the machine. If the motor and the machine are being overworked, the system will either take steps to reduce the amp draw, or will send an alarm to the operator,” he says.
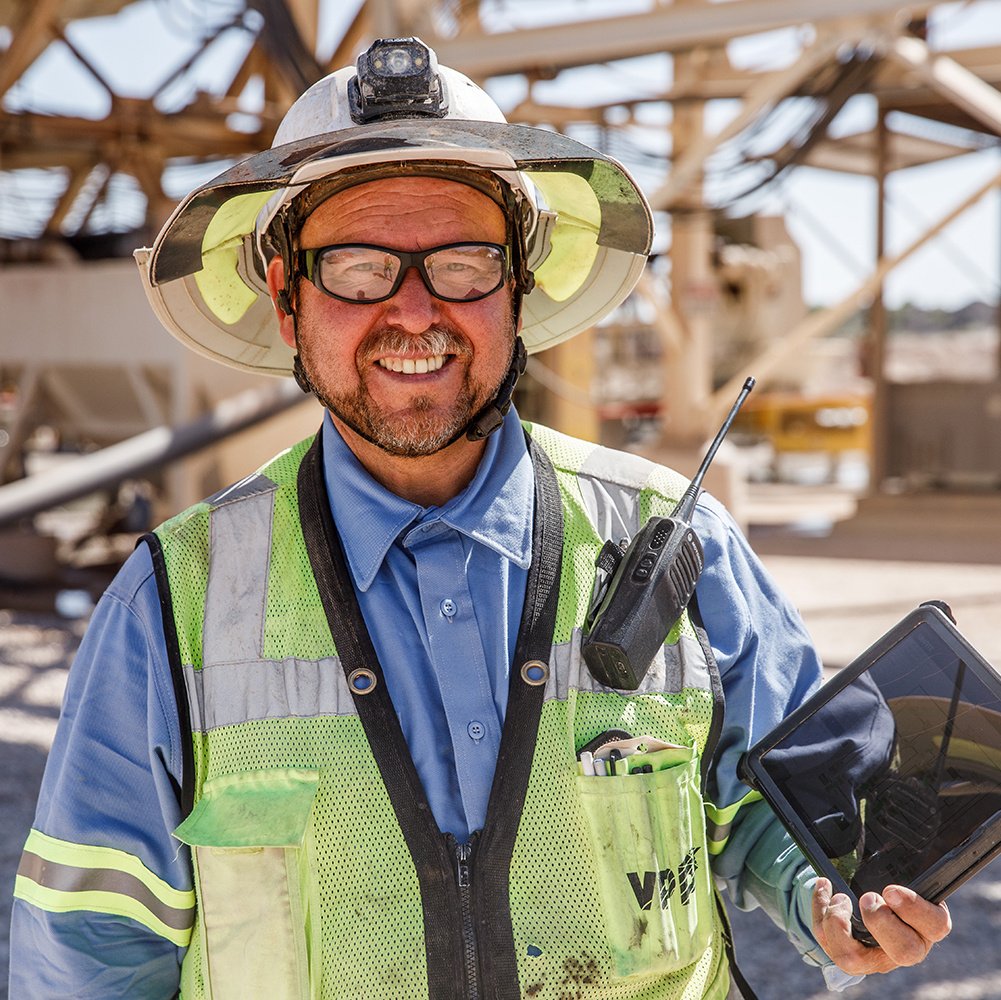
Automation features are also designed to maximize the life of wear components. For example, Superior’s automation package for all its cone models includes autowear compensation. As liners begin to wear, the crusher is designed to automatically compensate for that wear in order to maintain the same settings in the machine. With liner wear, the space between the two compression components expands. At the same time, the auto wear compensation system automatically closes the machine down to
maintain proper settings throughout the life of the wear components.
Know the True Limiting Factors
One of the major misconceptions Adcock encounters in the field, he says, is the way operators may view the closed side setting (the material discharge opening from maximum to minimum) of the cone. Operators often try to maintain a specified closed side setting (CSS), assuming they will yield the desired product output no matter what. Often, they close the setting down to the smallest point possible and then let the machine beat itself up.
Adcock suggests a better approach to setting up a cone for maximum performance.
First, consider that the true limiting factors of any cone crusher are attached power and crushing force. After determining the proper speed and liner configuration, it is possible to “dial in the proper settings of the machine” based on maximizing the amp draw to a desired set point – while making sure that the machine does not incur ring bounce at that point.
Practice Proper Lifecycle Management
Throughout its lifecycle, a cone crusher needs to withstand daily abuse. Operators should practice the following to optimize crusher performance:
- Invest in high quality equipment and components upfront.
- Maintaining ongoing preventive, predictive and reactive maintenance programs.
- Proper training of personnel is key to overall performance and efficiancy.
- Partner with crushing experts and suppliers who are accurate, accessible, and willing to offer onsite troubleshooting.
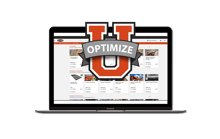
OptimizeU - Strategic Learning
Pursue greater production with comprehensive online courses in crushing, screening, conveying, and washing. Check out the premiere training resource in the construction aggregates industry.
Related Content
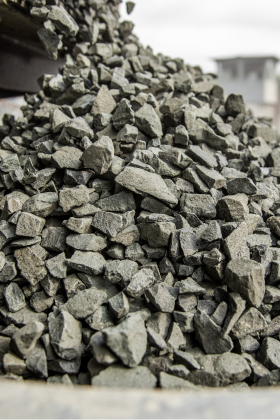
Sizing the Jaw Crusher: Three Simple Rules to Size By
Every producer wants peak crushing performance, but not every producer knows how to achieve it. Getting there may require just a few tweaks or even a total rebuild.
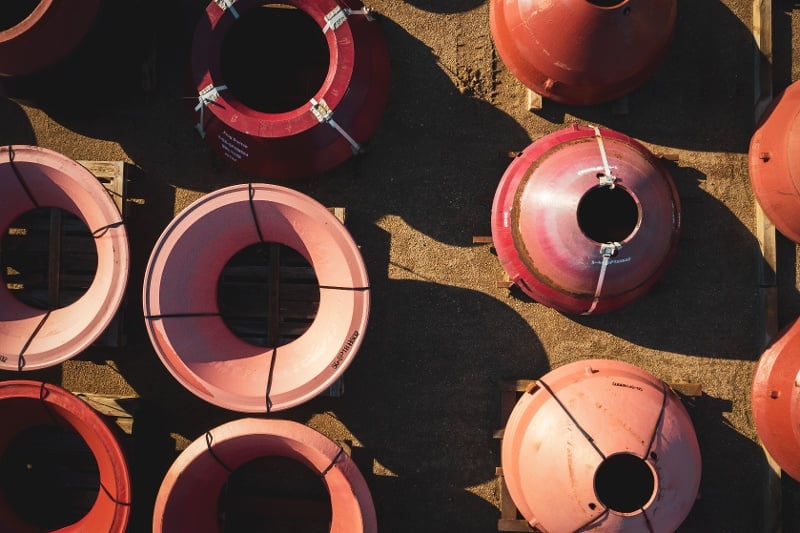
Boost Cone Liner Wear Life: Get Up to 30% More Wear Life
Boost your cone crusher liner wear-life by considering several key strategies.
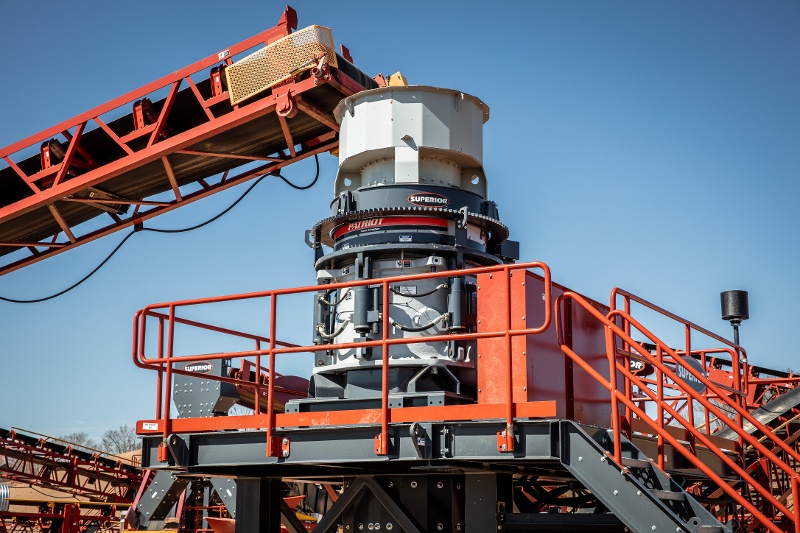
Air Breather Maintenance: Don't Overlook Crucial Crusher Protection
If your crusher runs with a dirty air breather, that positive air flow becomes a negative air flow that sucks dirt and dust into the machine.