Tech Tip: Low Water Sand Processing
Six Things to Optimize Your Wet Processing
Water shortages are worsening. Environmental regulations are tightening. Sustainable practices in sand processing have never been more important – not only to protectand preserve valuable resources – but also to maintain ongoing profitability.
How do you become water-wise? How do you practice and maintain low water sand processing? While there is no quick fix or one-size-fits-all solution, there are key steps that lead to reduced water use, maximum recovery, and overall efficient operation.
Based upon the expertise of veteran mineral wet process guru, John Bennington, we’ll outline the six biggest things you must know about low water sand processing.
1. Realize Proper Mainenance is Step One
If your processing equipment is not maintained properly, you’re putting material in the settling pond that belongs in the stockpile. You’re losing money on the salable product side, spending even more money on pond management, and wasting valuable water
resources day after day.
Always practice proactive (versus reactive) maintenance strategies. Get in the habit of conducting regular plant walkthroughs and for a strategy that catches smaller issues before they become larger costly concerns.
- Employ recommended lubrication practices.
- Maintain proper screen belt tensioning and inspect screen media weekly for opening wear or holes.
- Monitor your raw feed gradation to determine if any changes have happened.
Material processing is an end-to-end solution via a complete system. It makes little sense to put the latest, greatest component in the material flow chain if, for example, the screen ahead of the circuit isn’t functioning as specified.
Access the right support teams. It’s important to work with an equipment and service provider who examines your operation as a whole; and customizes solutions to meet your specific needs and product specifications.
2. Make Settling Ponds an Operational Plus
Some sites are ideally suited to the use of settling ponds and others are not. A common complaint is the issue of filling too quickly and requiring frequent, time-intensive bailing.
Again, make sure that the only material going to the pond is material that’s supposed to go to the pond. That’s the first thing.
The next thing is ensuring that the pond is big enough for the water volumes required. You can’t have a pond with a capacity to hold three weeks of silt, and then only bail it out every six months. Obviously, that doesn’t work.
In truth, operations often ignore the math. They don’t calculate the amount of silt that accumulates every single hour, and what space that ultimately requires.
If the operation is using flocculants to chemically treat the pond, that can help. Facilities may also add a fines recovery system and a water clarifier to the mix. In that case, flocculants are limited to just the quantities needed to treat the solids. That means that if you are cutting half the solids out of the waste stream, you’re only using half the chemicals – which is a big savings.
Lastly, if you are employing chemical treatments – regardless of what other mechanical systems you are using – you must have a water storage capacity that equals about a day’s runtime of the plant. Why? Because even with the best of systems, it’s difficult to
be exact on the optimal amount of chemicals to use in any given case. Too little and the system doesn’t work at all – while too much can result in unused, unwanted.
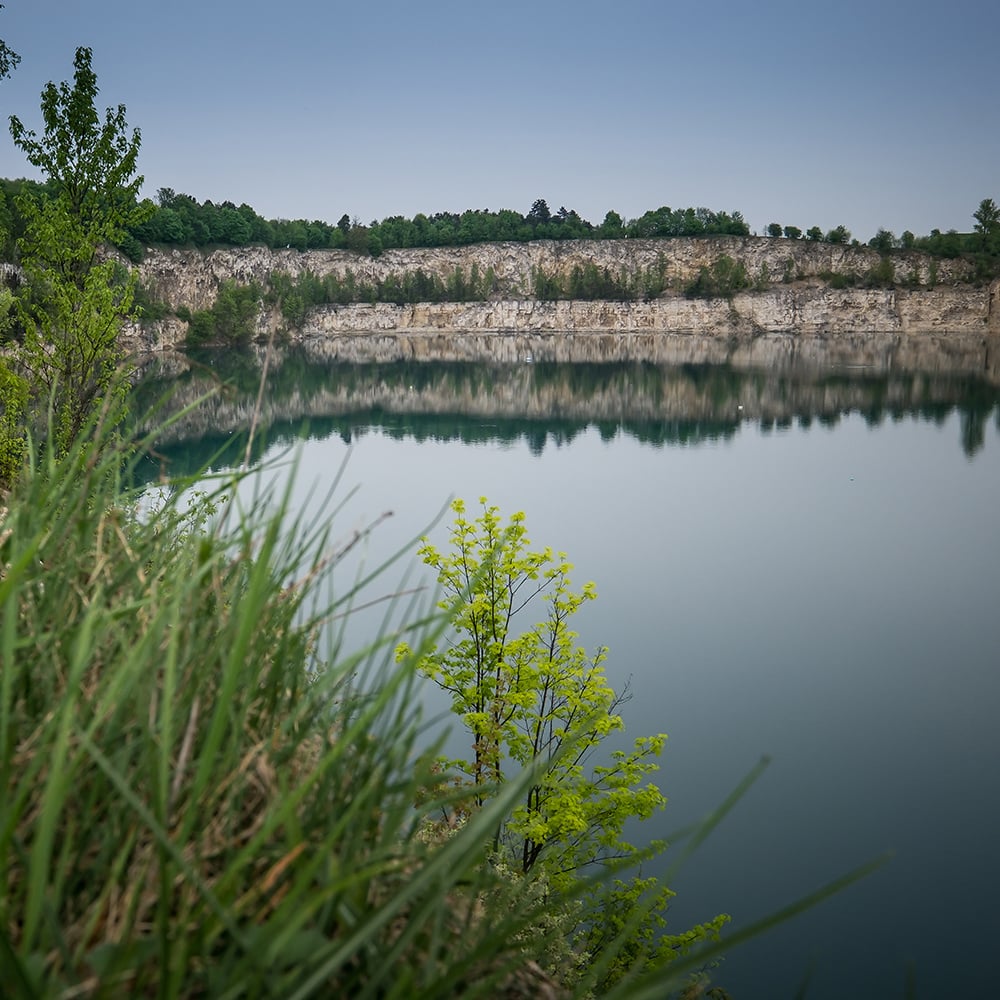
3. Understand Water Efficiency is Not a Quick Fix
To minimize pond use and maintenance, operations may turn to mechanical solutions such as filter presses, cyclones, water clarifiers, fines recovery systems, and more. While each has its advantages and disadvantages in an application, there is rarely just one quick fix, or just one piece of equipment recommended for any given situation. It’s usually a good idea to have more than one stage in an effective mechanical solution.
For example, it’s common to see producers placing a cyclone fines recovery plant in the middle of the waste stream before it’s discharged to the pond. Producers may view this as an easy, simple solution. However, consider that most cyclones generally keep only about half of the minus-200-mesh material from going to the pond. Consequently, much of the material that goes to the pond is ultra-fine. These particles are not easily bailed, as they simply flow around the excavator bucket. Someone once described this situation as “bailing smoke.” This supports the fact that quick fixes such as these can make the problem worse.
4. Incorporate Low Water Washing Technology
More and more operations are faced with severely limited water resources to pull from wells or from the environment. At issue is the amount of water required for conventional washing methods and the need for alternative and economical low water washing solutions.
As to conventional methods, a sand screw needs 50-gallons per minute of water for every ton of minus-200-mesh in the feed. Even if an operation is only running at 100-tons per hour, and their minus-200-mesh is at 15% – that is 15-tons of fines requiring 750-gallons per minute of water to adequately lift the silt over the weirs of the screw. That’s a lot of water for most crushing operations.
With the latter challenge in mind, Superior Industries has engineered its Alliance® Low Water Washer to cut water usage by up to 80%. The technology combines a specially designed agitator and a dewatering screen within one machine. It allows the operation to wash crusher dust right next to the crushing circuit, eliminating the cost of handling and hauling the fines to a separate washing circuit. The system accepts a dry feed directly from the crushing circuit and processes that material into a highervalue manufactured sand.
The agitator section in the low water washer is positioned at the front end of the screen where water is added to the dry feed and mixed, producing a thick slurry which is fed to a robust dewatering screen. A series of spray bars push the material down through the screen.
A sand screw requires considerable water usage to lift the silt over the weirs. Alternatively, the low water washer uses far less water as it pushes material down through the screen, while producing a product that is much lower in moisture content. Consequently, the big advantages are low water use, large throughput, efficient fines management and lower costs per ton.
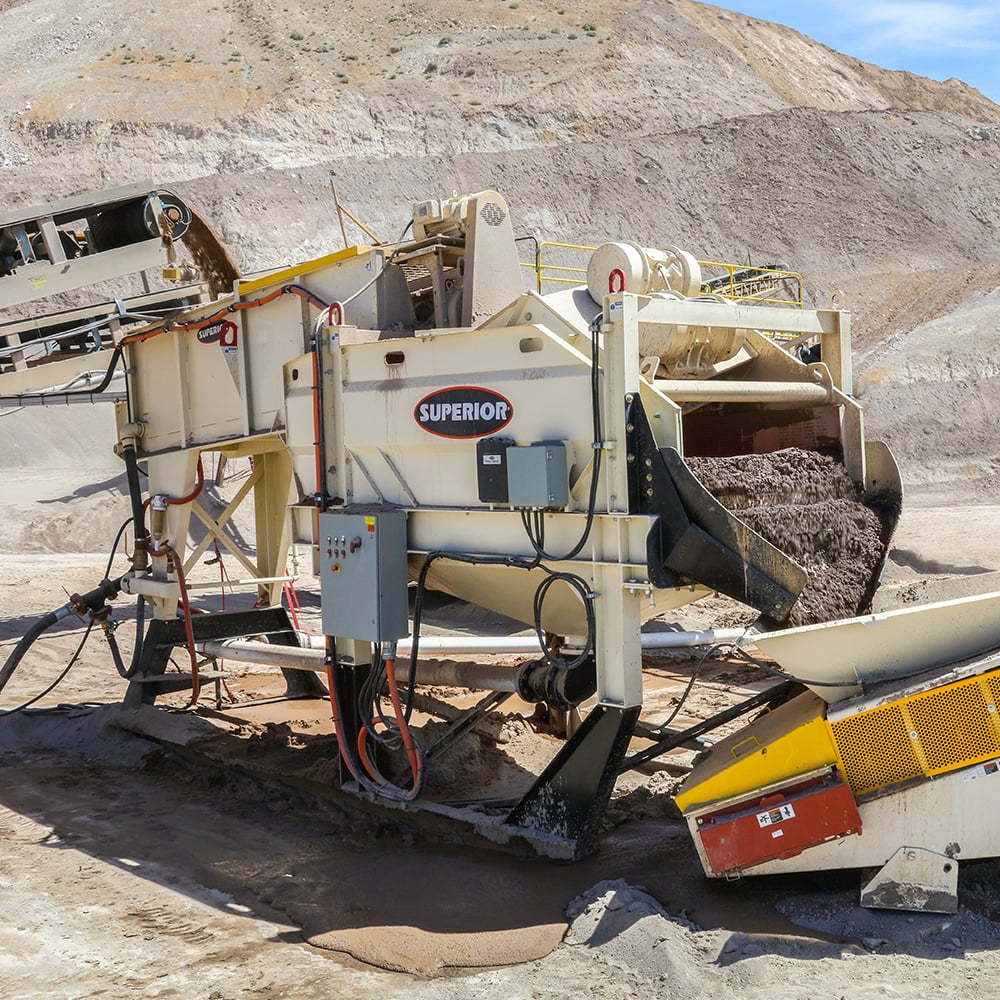
5. Use Dewatering Washers For Fines Recovery
For many operations, maximum water recovery is job one. They must achieve as much of a closed loop as possible within the wash plant. Consider that a standard sand screw will put about a gallon of water per minute/per ton into the stockpile. That water is a net loss. It’s not discharging into a pond or recycling back into the system. It’s either going into a truck or evaporating on the ground.
As a result, Superior has designed its Aggredry® Dewatering Washer to maximize recovery by capturing, recirculating, and reusing water within the system. Operations can cut water usage by 50% or more, when compared to conventional methods.
Within the Aggredry Washer, the clays, dirt and fines are separated before the sand moves to an attached dewatering screen. Lost fines are collected in an underflume and are flushed back to the screw. The resulting sand is discharged from the washer with a moisture content as low as 8%, making it immediately saleable.
While cyclones are commonly used in sand washing applications, the slurry pumps in cyclone plants significantly increase horsepower requirements and inflate energy costs. Using as little as one-third the horsepower per metric ton as that of the
typical cyclone, the Aggredry dewatering washer delivers energy cost savings, while producing a finished product that requires no drying time.
In short, the Aggredry Washer is designed to overcome the big disadvantages of wet processing – water and material waste; stockpiling space for drying time; and costly pond maintenance.
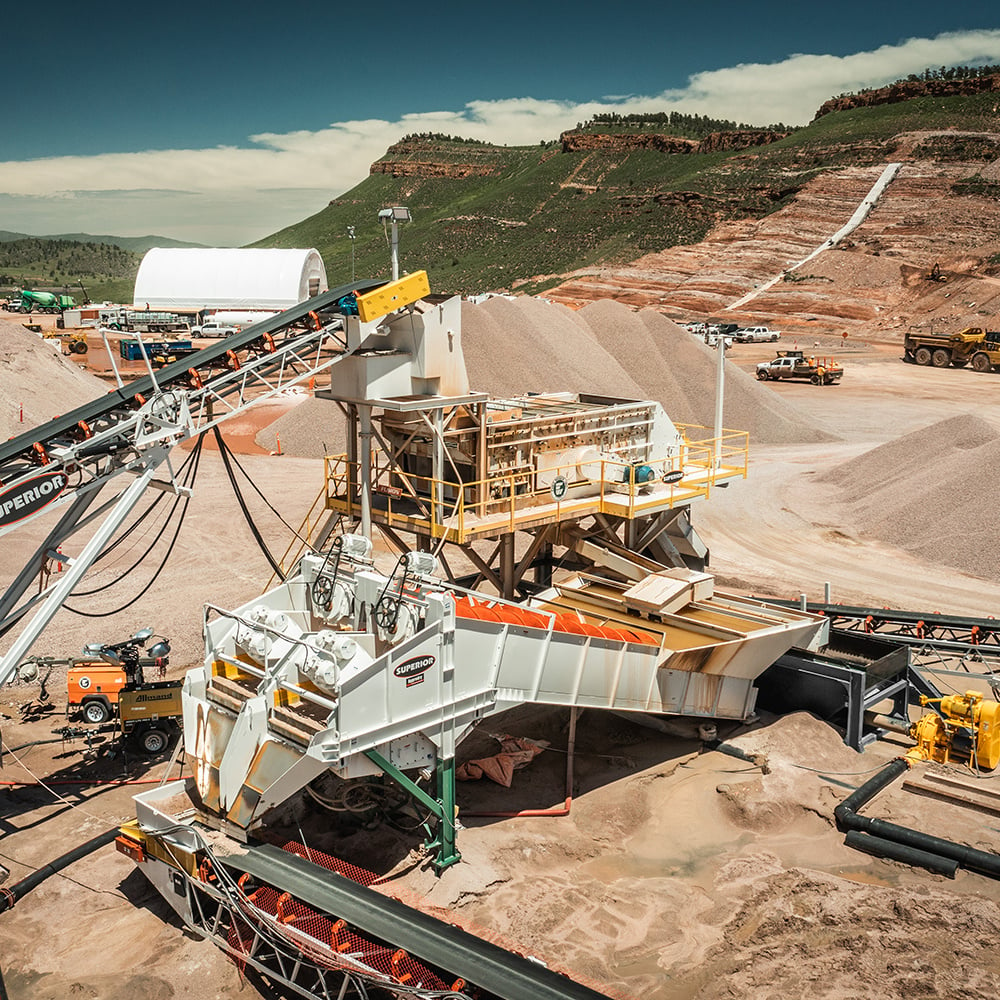
6. Profitability Requires More Water Recovery
In truth, efficient water use rarely gets the attention it deserves. Because water use is such a big part of sand processing, it needs just as much attention as your finished products require. By being wise in the use of valuable water resources, operations remain profitable while achieving much-sought-after sustainability goals.
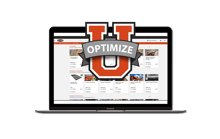
OptimizeU - Strategic Learning
Pursue greater production with comprehensive online courses in crushing, screening, conveying, and washing. Check out the premiere training resource in the construction aggregates industry.
Related Content
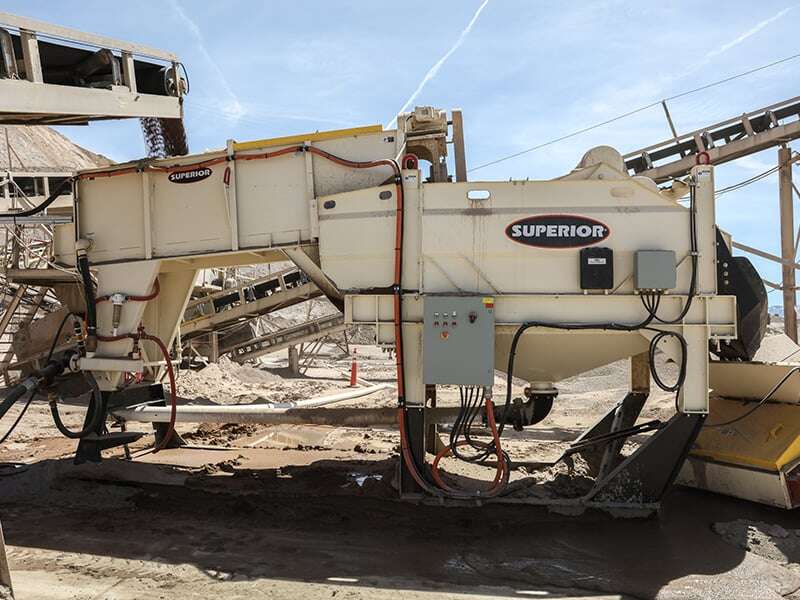
New Value From Crusher Fines: A Low-Water Solution for Manufactured Sand
20170209_0695-1.jpg)
Maximizing Profits, Minimizing Water Use: Wissota Sand’s Sustainable Solution
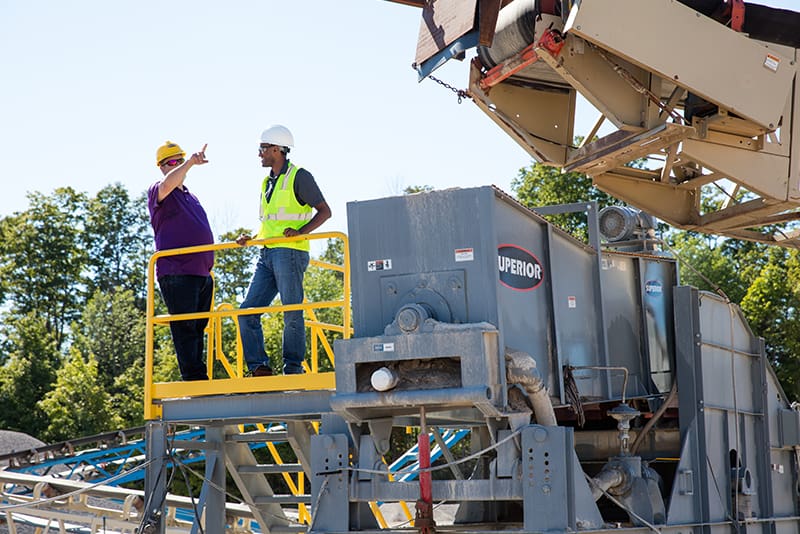