Tech Tip: Conveyor Transfer Points
Useful Tips to Eliminate Spillage
A transfer point is any point where material is loaded onto or unloaded from a conveyor. Preventing spillage at any given transfer point is imperative as the cost reductions from eliminating spillage at just a single transfer point are significant.
It is estimated that 85% of conveyor maintenance is a result of fugitive material, says the Mining Safety and Health Research (MSHA) group who has assembled some figures on the labor costs of one person spending one hour per shift to clean spillage at one transfer point.
The labor cost for one year exceeds $22,000, and over a ten-year period costs top $220,000! Also consider that the elimination of 5,200 hours of repetitive manual material handling over a ten-year period means fewer injuries and worker’s compensation claims. Properly designed transfer points also mean cost reductions resulting from less equipment damage, reduced conveyor maintenance and increased conveyor uptime.
Ideally, a transfer point should be designed to load the belt in the center and at a uniform rate. Also, transfer points should be engineered to reduce the impact of material falling on the belt. Loading zone impacts cause wear and damage to the conveyor belt, weakening the belt carcass. To reduce impact at transfer points, impact cradles can be positioned under the conveyor. Or, impact idlers may be used at a transfer point. These are troughing idlers that have rubber-cushioned rollers to absorb impact.
Also, it’s important that skirtboards and loading or discharge chutes be selected and installed to match the characteristics of the material as well as the conveyor. For example, the Conveyor Equipment Manufacturer’s Association (CEMA) suggests that the width of a loading chute should be no greater than two-thirds the width of the receiving belt. The inside width of the loading chute should be at least two-and-a-half to three-times the largest dimension of uniformly sized lumps, when they represent a considerable percentage of the material flow. Where lumps and fines are mixed, the inside width of the chute may be as small as two times maximum lump size.
As an extension of the loading chute, skirtboards are used to keep transfer material on the belt after it leaves the loading chute and until it reaches belt speed. Skirtboard length can be based on a rule of thumb of 2- to 3-feet per 100 feet-perminute of belt travel (600-900mm per 30m-per-minute). The material should be traveling the same speed as the belt when it leaves the load area.
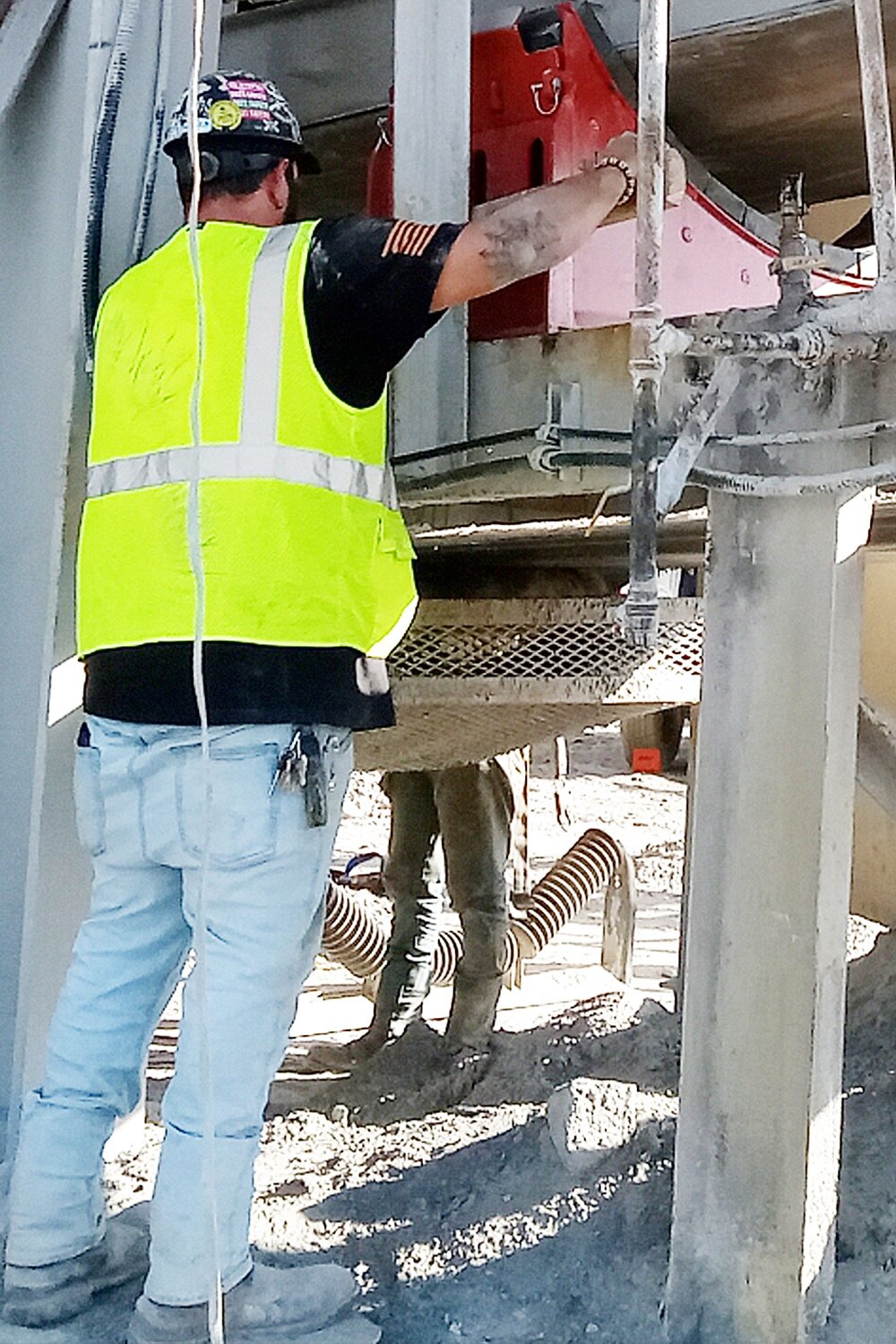
Additionally, the distance between the skirtboard and the conveyor belt is critical. Skirtboards need to be placed high enough so that they do not come in contact with the belt. However, the gap between the belt and the skirtboard should be as small as allowable, so that a flexible rubber strip that’s attached or clamped to the exterior of the skirtboard can easily seal it.
Remember, it is not uncommon for an inadequate conveying system to generate 1% to 3% fugitive material. Just a two-percent reduction, says MSHA, translates to a 67% cost reduction for conveyor maintenance due to fugitive material. It also translates to 67% fewer hours required for cleanup. That amounts to vast payback over time.
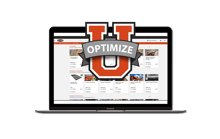
OptimizeU - Strategic Learning
Pursue greater production with comprehensive online courses in crushing, screening, conveying, and washing. Check out the premiere training resource in the construction aggregates industry.
Related Content
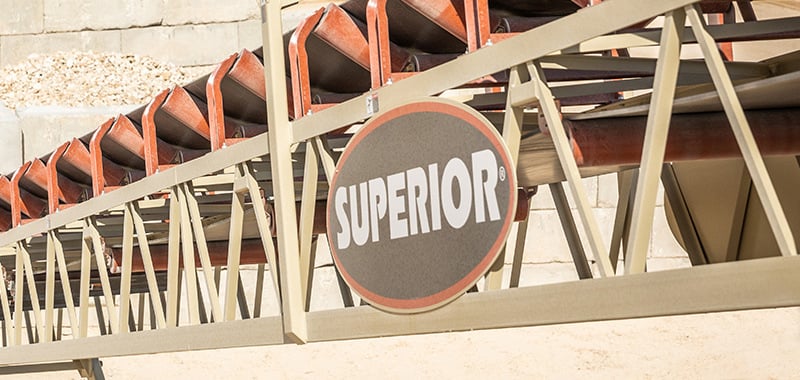
Conveyor Maintenance: Basic Design to Increase Your Uptime
Designing a conveyor to be maintenance friendly means providing adequate provisions for necessary service from the onset.
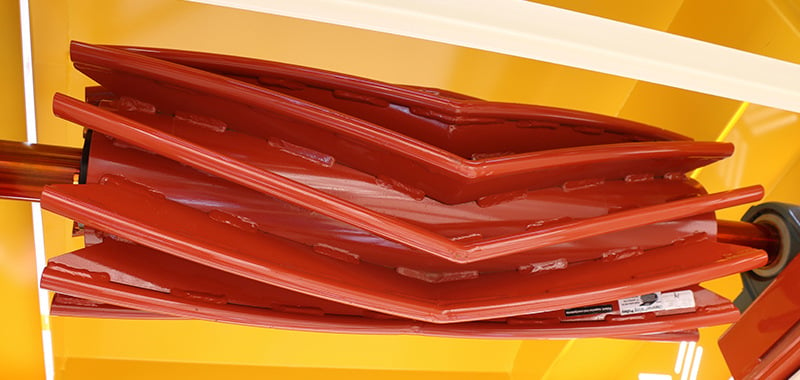
Modern Wing Pulleys: Extend Belt Life With V-Shaped Model
It is common for operations to stick with traditional conveyor components even though they are causing maintenance challenges.
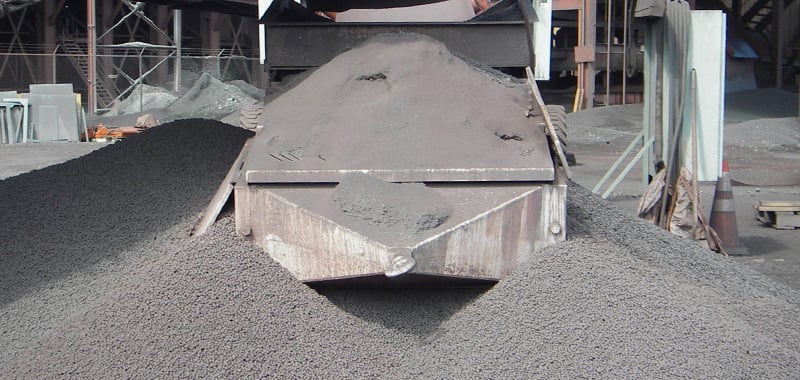
Conveyor Load Zones: Prevent Spillage with Simple Maintenance
Material spillage is a costly proposition and is common to many operations due to a lack of good preventive maintenance.
Talk to an Expert
Need more information? We'll get you in contact with a product expert in your area.