Tech Tip: Conveyor Pulley Lagging
The Rubber Layer That Decreases Downtime
Referred to as lagging, conveyor pulleys are often covered with some form of rubber, fabric, urethane, ceramic or other material. Lagging increases the traction between the belt and the pulley, which in turn reduces load and wear on the drive, belt, pulleys, bearings, and take-up. When seeking highly efficient and economical conveyor operation, proper pulley lagging is an integral detail – one that delivers the following key benefits:
- Extends life of conveyor components
- Reduces wear from abrasive materials
- Prevents belt slippage by increasing friction
- Creates self-cleaning action and prevents buildup
- Reduces drive size required
The Conveyor Equipment Manufacturers Association (CEMA) recommends that lagging be used for all drive pulleys, particularly those in high-tension applications. Non-driving pulleys (especially on the carrying side of the belt) should be lagged in abrasive environments.
Lagging thickness can vary from a few thousandths of an inch, as with sprayed-on coating, to a thickness of one- to two-inches (25-50mm), as with some solid rubber coverings, says CEMA. A 60-durometer lagging is the standard to ensure the long wear life and traction desired in most applications.
Most often, lagging is attached to the pulley via vulcanizing (preferred in heavy-duty applications). Or, replaceable lagging can be used. These lagging strips are bolted or welded to the face of the pulley and can be easily replaced in the field.
Also, growing in popularity is the use of ceramic pulley lagging that is constructed from hundreds of individual ceramic tiles molded into a durable rubber backing. In certain applications, ceramic lagging can significantly increase drive traction.
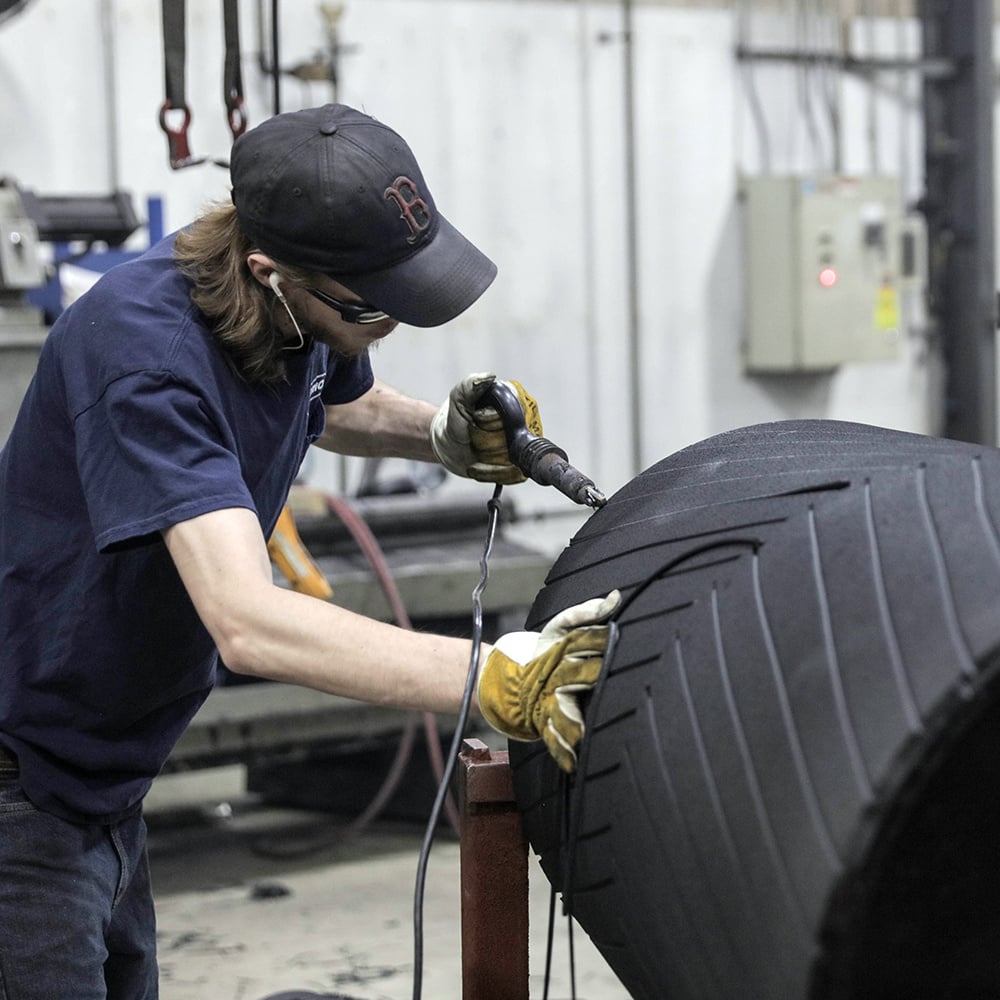
Lagging Specification Tips
- Steel drum pulleys with no lagging are best in dry, clean environments where no carryback is on the return belt.
- Drum pulleys with plain rubber lagging are typically used in snub applications where traction is not critical.
- Drive pulleys that operate in wet conditions are commonly grooved and available in smooth, herringbone, or diamond styles.
- There are also groove configurations and lagging that can enhance belt tracking or reduce material buildup on the pulley face.
- If a shaft is to be installed in a pulley, the groove pattern is usually consistent with the direction of the rotation.
- Lagged wing pulleys are used in applications with abrasive material on the return side of the belt.
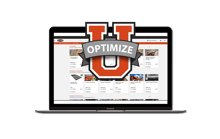
OptimizeU - Strategic Learning
Pursue greater production with comprehensive online courses in crushing, screening, conveying, and washing. Check out the premiere training resource in the construction aggregates industry.
Related Content
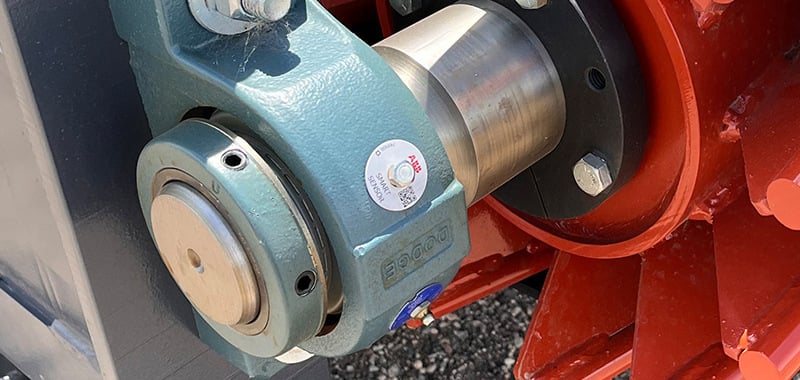
Conveyor Pulley Shafting: Proper Selection Matters
A conveyor pulley assembly is an integral structure that relies upon the pulley and shaft working and functioning together.
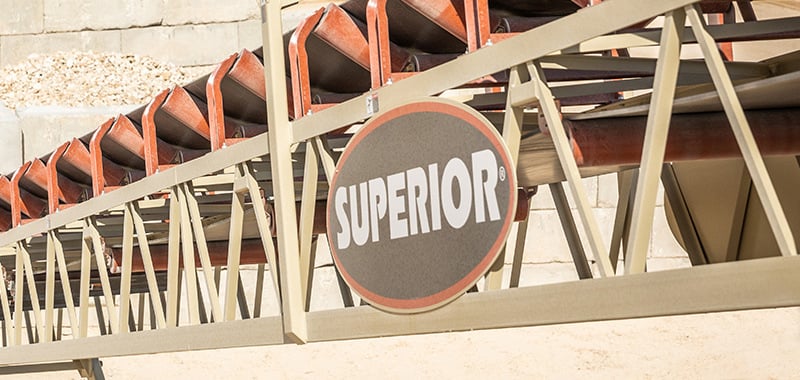
Conveyor Maintenance: Basic Design to Increase Your Uptime
Designing a conveyor to be maintenance friendly means providing adequate provisions for necessary service from the onset.
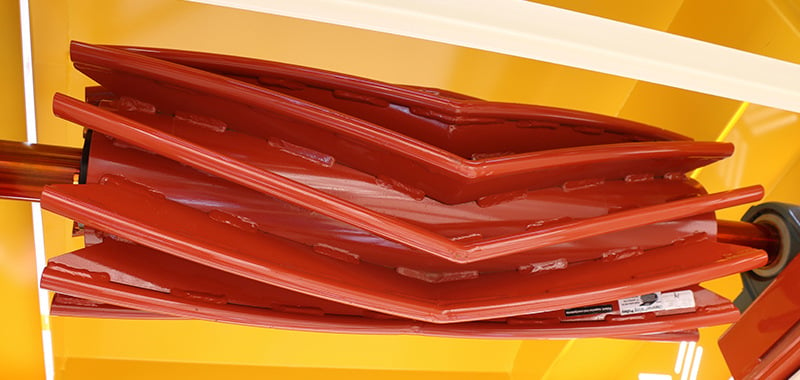
Modern Wing Pulleys: Extend Belt Life With V-Shaped Model
It is common for operations to stick with traditional conveyor components even though they are causing maintenance challenges.
Talk to an Expert
Need more information? We'll get you in contact with a product expert in your area.