Tech Tip: Consistency in Components
Standardization is Key for Conveyor Parts
Regarding conveyors and components, standardization is the key to savings and ease of maintenance. As each brand is not the same as the next, simply choosing the current, lowest-priced conveyor, idler or pulley will no doubt cost you more in the long run.
Today, modern operations may access and maintain miles of conveyors with thousands of idlers. Consider that idlers, for example, are highly engineered, application-sensitive components that are critical in getting material from point A to point B–and it only takes one small malfunction to delay the entire production process. Producers can avoid costly downtime headaches by standardizing conveyors and components for easy, cost-effective maintenance.
Standardizing your conveyors and components will open the door to a host of benefits, including:
- Minimizes overall downtime
- Prevents compatibility problems
- Facilitates easier maintenance and replacement
- Allows integration with a wide range of accessories
- Delivers flexibility to easily reconfigure a system
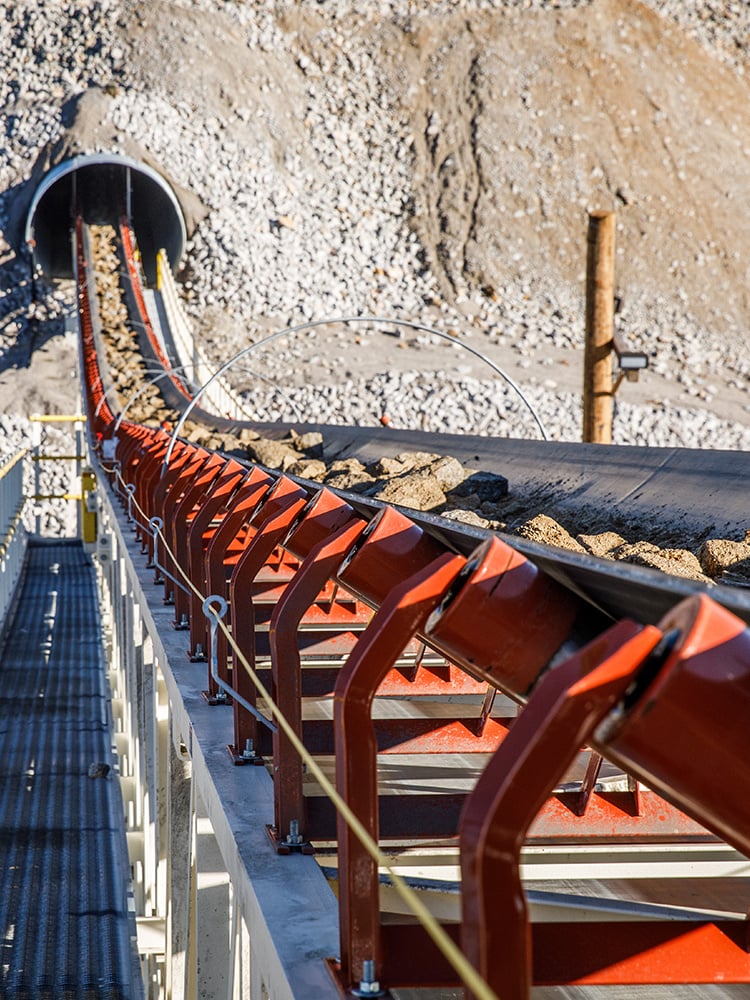
Many producers (particularly those with multiple sites) have found that standardization of idler components alone saves considerable time and money, cutting replacement parts costs by as much as 65%.
When mixing numerous idler brands, it becomes necessary to replace an entire idler rather than simply changing out one of its rollers. Also, it would be necessary to stock a greater amount of parts to keep systems running at every site. More downtime is incurred in trying to determine which idlers and which rollers will fit each particular conveyor.
With component standardization, if one roller freezes up or develops a bad spot, it’s far more cost-effective to replace one roller rather than replacing three rollers and a frame. One needs only to remove the worn roller and snap a new one into place.
Additionally, teaming poor quality idlers with high-quality belting leads to unnecessary belt damage and conveyor failure.
Well-planned component standardization seems like an obvious solution, but it is often not employed as operations may have different superintendents per each site, with no one coordinating purchases at the upper management level. Furthermore, the trend toward modular conveyor units is changing the way that producers view conveyor and component purchases.
Conveyor manufacturers are offering stackable, self-contained conveyor sections that are easily transported to a site, and can be configured and reconfigured based upon varying production demands. Once one has researched, tested and successfully employed modular units, it is likely that they will remain with the same supplier.
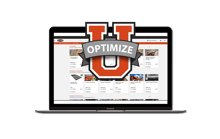
OptimizeU - Strategic Learning
Pursue greater production with comprehensive online courses in crushing, screening, conveying, and washing. Check out the premiere training resource in the construction aggregates industry.
Related Content
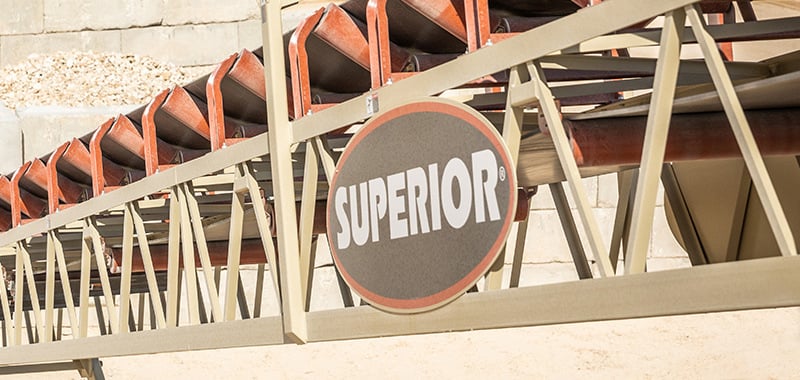
Conveyor Maintenance: Basic Design to Increase Your Uptime
Designing a conveyor to be maintenance friendly means providing adequate provisions for necessary service from the onset.
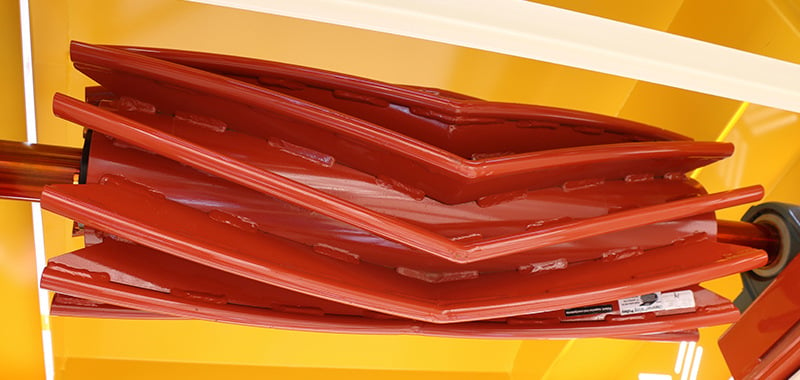
Modern Wing Pulleys: Extend Belt Life With V-Shaped Model

Conveyor Idlers: Don’t Overlook This Most Critical Component
While reliability of each conveyor component is key, it’s the often overlooked idler that should always receive proper consideration.
Talk to an Expert
Need more information? We'll get you in contact with a product expert in your area.