Tech Tip: Air Breather Maintenance
Don't Overlook Crucial Crusher Protection
“Air breather maintenance is more important than you think. Ignoring it can lead to a nasty situation, which can be described as lubricating your crusher with ‘sandpaper-laced’ oil. Don’t forget to inspect air breathers weekly and clean out any dirt and debris. Then replace the air breather with a new one every month or two,” says Curt Theisen, crushing technical support engineer for Superior Industries. He explains why proper air breather maintenance is key to protecting cone crusher performance.
“Unfortunately, the air breather is a commonly neglected component,” says Theisen, as he shares the following example: When attending a crusher service training school, one of the participants wondered why his facility consistently had problems with dirty oil in the crusher lube system. He swore up and down that his crew was managing everything on the maintenance checklist.
When a fellow trainee offered to take a look at the crusher, it took only seconds for him to say, “I can tell you right now that you haven’t been checking your air breathers.” He pointed to the accumulation of thick, hardened dirt and debris sitting on top of the air breather itself. Obviously, no one had removed the air breather cap in order to inspect it in quite some time. Lesson learned.
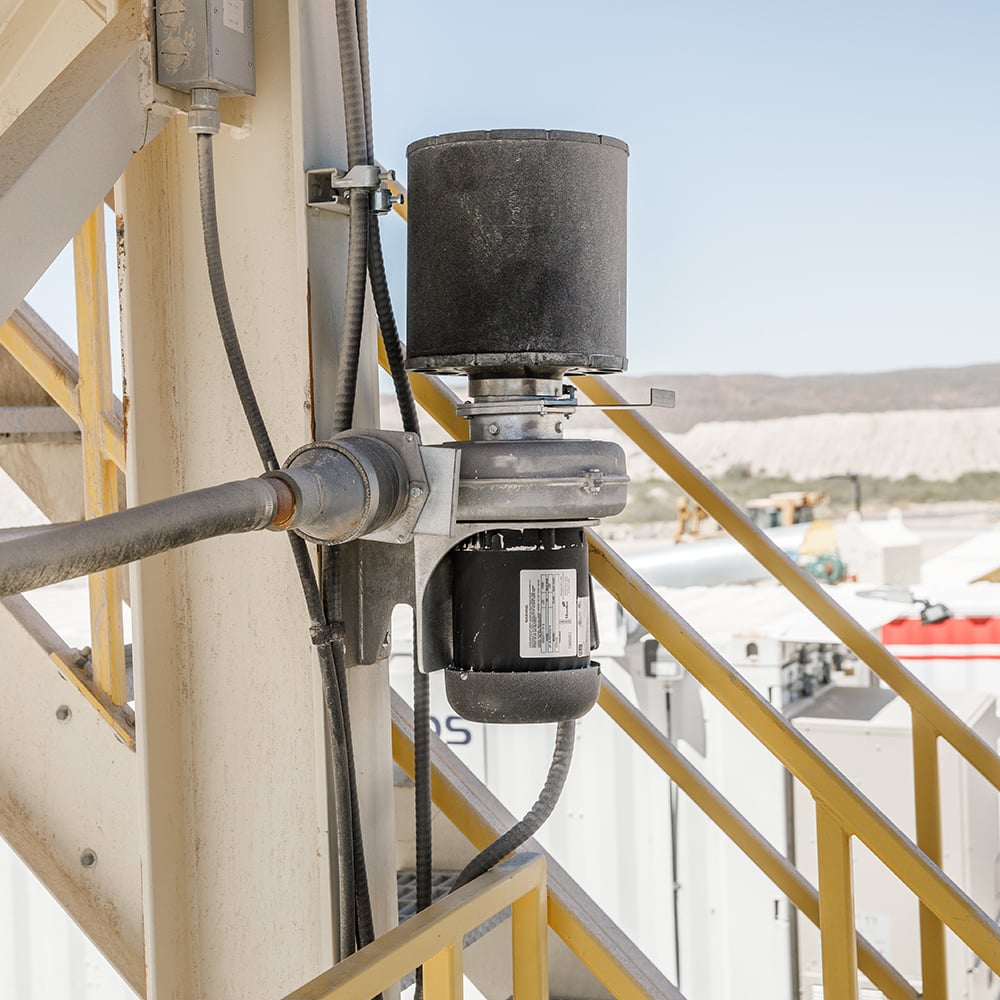
Air Breather 101
According to Theisen, the countershaft box air breather and the oil tank air breather work together to maintain atmospheric pressure in the crusher, and in the ancillary lube and hydraulic units. Their proper operation generates a positive airflow through the machine, keeping dust and debris out of the machine, and away from its head sealing arrangement.
If the crusher runs with a dirty air breather, that positive air flow becomes a negative air flow that sucks dirt and dust into the machine, causing potential contamination to the head seals and lube drainage line. With dirty oil in the system, expensive internal components such as bronze bushings and crusher bearings will incur premature wear and potential failure.
Along with weekly air breather inspection, take an oil analysis sample after each 200 hours of crusher operation. If there is a high amount of silica in the oil, it is likely that there will also be a higher content of tin, lead, and copper in the oil – as those are the three materials contained in a bronze bushing.
Preventitive Maintenance
What you don’t see the air breather, you often forget about it. Sometimes, air breathers are in enclosed areas, behind a door. Make sure that their inspection is on your mental checklist and take the necessary time to complete the task. Your application and environment will determine how often you must replace the air breather. Dry, dusty applications are the hardest on an air breather. If the crusher has a very tight discharge area, such as on a portable plant – or if the crusher is running at an extremely low RPM – those are situations where you may wish to add a blower with an air breather. In any event, never let the often-forgotten air breather remain out of sight and out of mind.
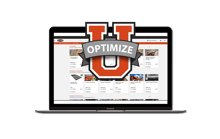
OptimizeU - Strategic Learning
Pursue greater production with comprehensive online courses in crushing, screening, conveying, and washing. Check out the premiere training resource in the construction aggregates industry.
Related Content
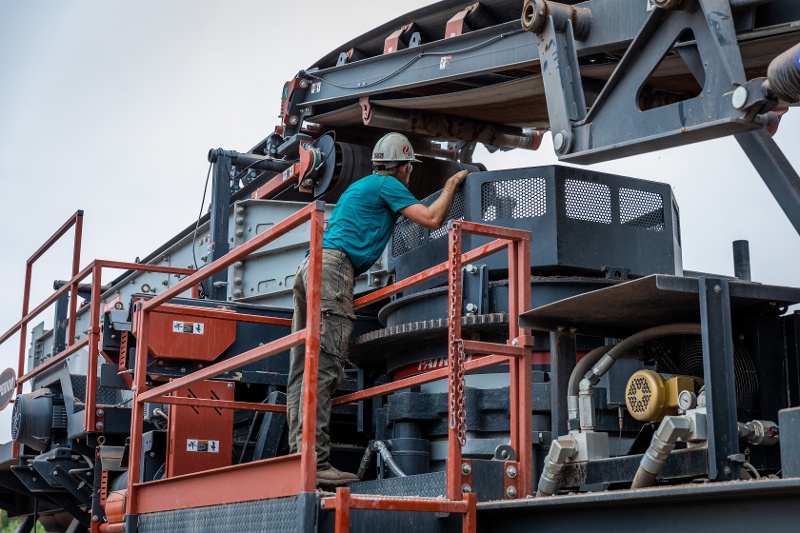
Maximizing Cone Crusher Performance: Achieve Peak Performance in Quarrying & Mining
Maximize cone crusher performance in quarrying and mining with proactive maintenance, proper circuit design, and easy-to-use automation.
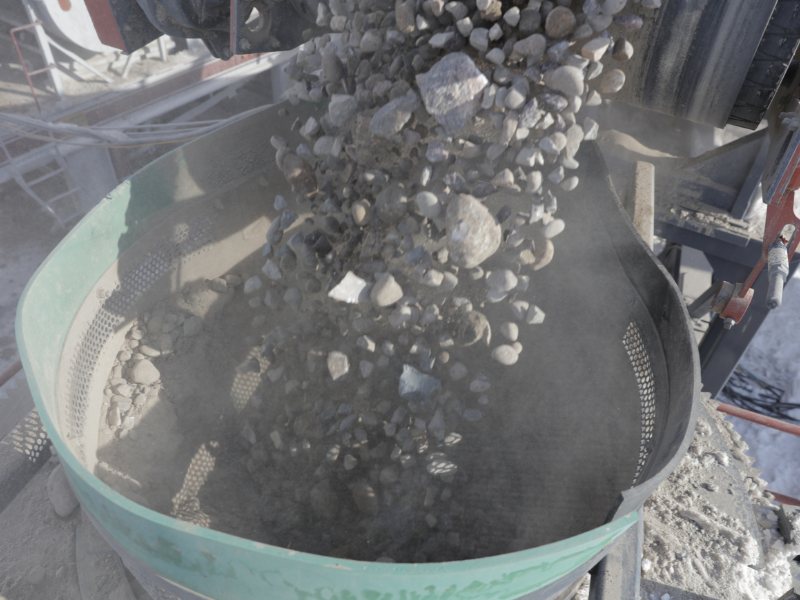
Selecting Jaw CSS: Maintain the Right Closed Side Settings
Ensuring the proper jaw crusher closed-side setting size is essential for proper material flow throughout the entire plant.
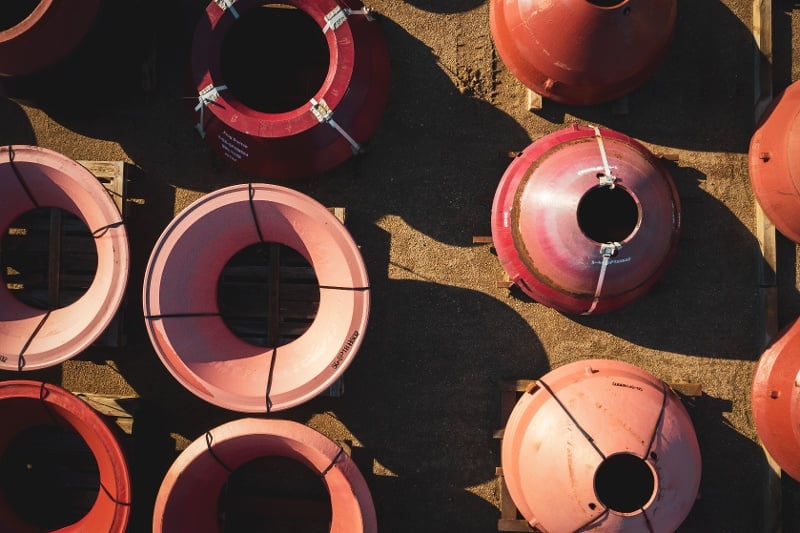
Boost Cone Liner Wear Life: Get Up to 30% More Wear Life
Boost cone crusher liner wear life by up to 30% with proper work-hardening and consistent choke feeding strategies. Enhance efficiency, lifespan, and profitability.